
Ropes and knots are among the most ancient and useful technologies ever developed by man, predating the wheel, the axe and probably also the use of fire. Today, they are fast on their way to become an obsolete technology.
The earliest fossilized fragments of ropes and knots date back 15,000 to 17,000 years, which makes the direct evidence of this technology much older than that of the axe (6000 BC) or the wheel (5000 BC). However, based on indirect evidence (perforated objects, wear marks on artefacts, bone needles, representations in art, etcetera), archaeologists believe that the use of ropes and knots dates between 250,000 and 2,500,000 years old.
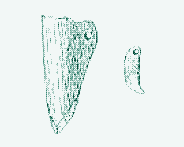
Speculatively, this might even predate the use of fire (400,000 BC) and coincide with the first crude stone tools. It is interesting to note that modern apes have some very elementary skills at knotting and ropework, which suggests that the beginning of knot tying may well have preceded the evolution of the genus Homo.(source)
Few realize the importance that knots and cords have played in human history. It is remarkable that they are not even mentioned in otherwise great books on the history of technology. Yet, it is hard to find any important technology developed over the last 250,000 years that did not, in some way, make use of ropes and knots. Starting in prehistoric times, they were used for hunting, pulling, fastening, attaching, carrying, lifting and climbing.
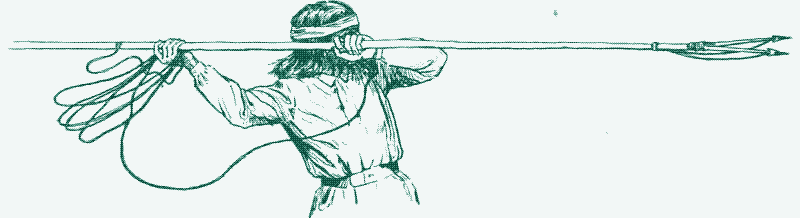
Some early examples of their applications are fishing nets, hunting traps, tying stones to sticks to make spears and harpoons, the construction of bows, building shelters, making baskets, fastening clothes, tying animals (and people), harnessing horses and oxen to chariots, and constructing rafts. Cordage of some kind, and the knots needed to make it work, have played a crucial role in the earliest technological development of man.
Hauling and lifting
With the rise of civilization, the ingenuity in the application of ropes and knots was expanded, used for the hauling of canal boats, the dragging of heavy stones along ramps, and the erection of large obelisks (first done by the ancient Egyptians), the development of cranes, lifting devices and catapults (kicked off by the Greeks and the Romans), the construction of enormous rope bridges and rope suspension bridges (which originated in China), the appearance of sailing vessels, and more.
The construction of the noose to hang people was another application of ropes that was invented by “civilized” people, as well as the ringing of church and monastery bells. Although other materials were involved, notably stone and wood, none of these technologies could have worked without ropes and knots. Apart from all these practical uses, ropes and knots also became an important decorative element, especially but not limited to Chinese and Celtic cultures.
Talking knots
Ropes and knots were also used as record keeping devices, best known in the form of the Peruvian “khipu” or “quipu”. The Inca civilization (1400 - 1530) made extensive use of them for accounting and census purposes - recording the contents of storehouses, the number of inhabitants, etcetera (picture credit and more info).
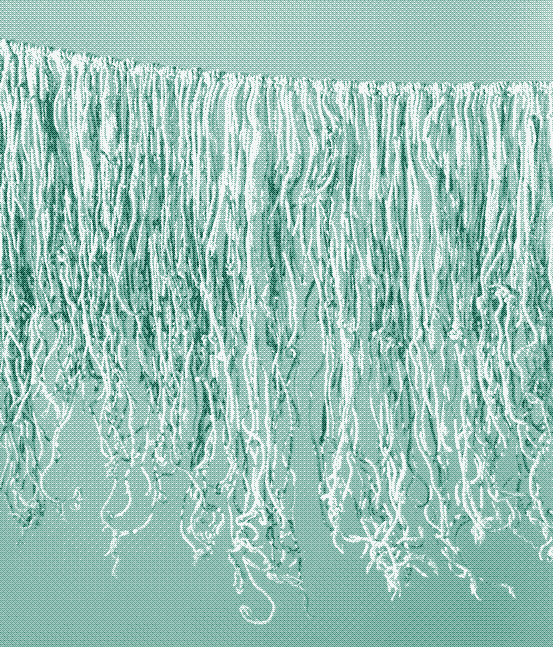
A khipu consists of a long cord from which hang thinner ropes, sometimes just a couple, sometimes many hundred. These pendant cords are tied in a series of small knots. Originally, they were dyed in rich colors. Because the Inca’s, unlike other civilizations, appear to have lacked a written language, one hypothesis is that these bundles of knotted strings also contain narrative information and can thus be regarded as a form of writing (1 / 2 / 3). The khipu was probably developed in pre-Inca times, because less elaborate knotting recording devices already appeared in primitive societies in China and elsewhere (1 / 2 / 3 / 4).
The hardware: ropes
In rope making, four basic steps are identified: preparing the fibre, spinning the fibres together to form yarns, twisting the yarns in bunches to form strands, and winding the strands in rope (see the illustration on the right).
At each stage the twisting is performed in the opposite direction from the previous stage, in order to overcome the natural tendency for each yarn, strand or rope to unravel. Most ropes consist of three twisted strands (called a Hawser laid rope).
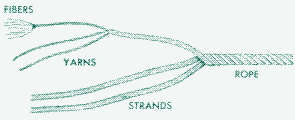
It is likely that the earliest “ropes” in prehistoric times were naturally occuring lengths of plant fiber, such as vines, followed by the first attempts at twisting and braiding these strands together to form the first proper rope in the modern sense of the word. This must have been a time-consuming process, more related to weaving plant fibers into mats and baskets than to later ropemaking methods (more info: 1, 2, 3 and 4).
For centuries afterwards, ropemaking remained a manual process, without the use of tools. It could be done alone, or by two people working together. In the latter case, one person held the two strands, one of them in his hand and the other tied to his big toe, while his companion standing some distance away twisted them together (source).
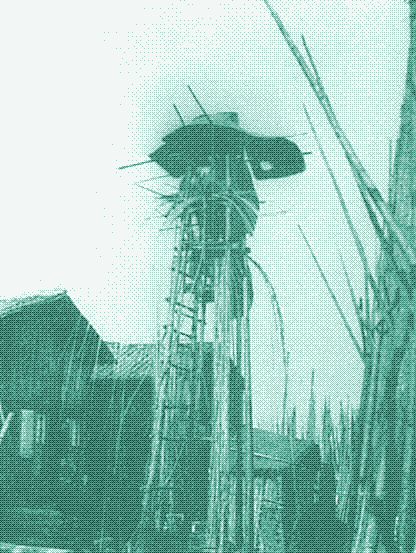
Another simple method was used in China when making bamboo ropes. Two workers on a high wooden tower corded bamboo strips which had been cut several metres long and hung down from the working platform so as not to become entangled, see the picture above left (source). The ancient Egyptians (from 4000 BC on) were the first to develop a special tool to assist the making of rope, using a hand held spindle (source). Much later, similar devices appeared in Europe and China (illustration above, right).
Ropewalks
International trade by sailing vessels skyrocketed in late medieval Europe and naturally, so did the demand for ropes. Sailing ships required rope for anchors and rigging (supporting the masts and managing the sails), and could easily carry with them 35 kilometres (around 20 miles) of rope. The arrival of larger sailing vessels (and the growing importance of the mining industry) meant there appeared a need for much longer, stronger and thicker ropes.
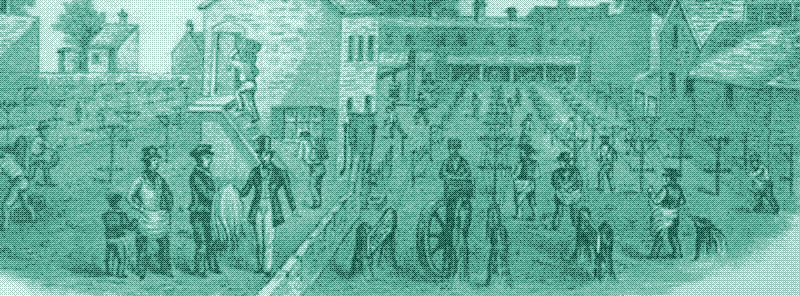
This led to the construction of some of the most remarkable industrial workshops and buildings in history: ropewalk factories. Because the spinning of the fibres (illustration above, England, 1770) and the twisting of the yarns and strands (illustrations below) had to be done in a straight line, the length of the rope was set by the length of the workshop. This resulted in strange looking narrow buildings which were typically 350 to 450 metres (1150 to 1475 feet) long by the 18th and 19th centuries, a time when navigation and mining kept pushing the demand for ever longer ropes. One ropewalk factory in Australia at the end of the 19th century was 760 metres long (2500 feet, source).
Several (human-powered) machines were added to make the process more efficient (illustration below - note that the illustrator made the ropewalk look much shorter than it was). At the beginning of the Industrial Revolution, these were scaled up and converted to steam power. In Europe, the US and Australia, some ropewalks remained in operation until the middle of the 20th century, after being converted to be powered by electricity. In some “lesser developed” countries they are still being used.
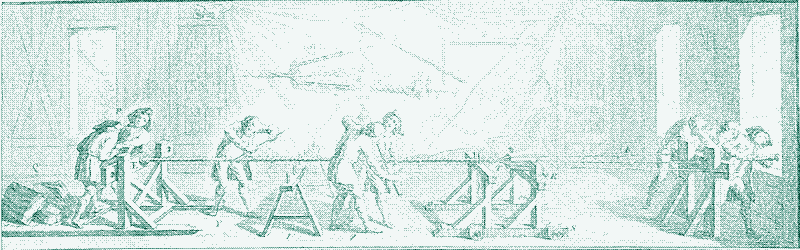
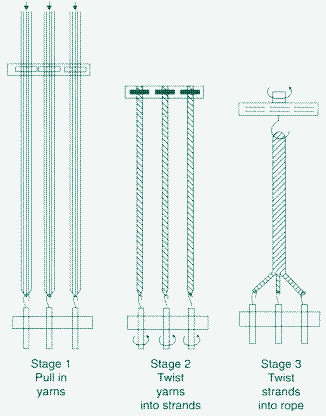
The ropewalk method - which was also in use in China - is very simple. Describing it is a little more difficult. I came across many lengthy and sometimes puzzling explanations, but the one I found in the book “Handbook of Fibre Rope Technology” makes it quite clear (the accompanying illustration comes from the same source):
“At one end, there is the jack, which has three hooks that can be rotated. At the other end, there is a carriage with a single, rotatable hook. In stage one, three sets of yarns are pulled off bobbins and are held along the length of the ropewalk.”
“In stage 2, an assistant turns the crank handle of the jack so that the yarns are twisted into strands by the rotation of the three hooks on the jack. Twist causes the lengths to contract, so that the carriage has to move along the ropewalk, under the control of the ropemaker.”
“In stage 3, the hook on the carriage rotates in order to twist the strands into the rope. In the usual mode of operation, the initial strand twist is made as high as possible without kinking. When the single hook on the carriage is released, the high torque in the strands causes the hook to rotate, and this, in turn, cause the three strands to twist together and form the rope. The ropemaker controls the production of the rope by continually pushing back its form of formation to give a tight structure. Meanwhile, the assistant continues to rotate the crank to make up for the loss of twist in the strands.”
Remaining Ropewalks
Most ropewalks were set up outdoors, sometimes underneath a wooden shelter. Some were housed in a brick or wooden building, which dates back to the beginnings of the 19th century.
The majority of earlier communities, irrespective of their size, had their modest ropewalk. Coastal towns, due to necessity, had several of them. For example: Boston (US) had 14 ropewalks in 1794, Plymouth (UK) had 14 of them in 1816 (source).
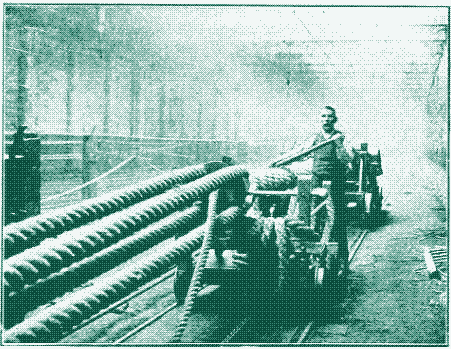
Ropewalks were mostly located outside the city or town, because of the fire risk they posed. In wooden structures especially, the combination of dried hemp and the open flames of the tarring vats was very risky (tar, made from pine trees, was used to make hemp cords more water-resistant).
Nothing remains of the smaller medieval ropewalks, nor of many later ropewalks in open air or in wooden buildings. However, some ropewalks housed in brick buildings are still intact. The ropewalk at Chatham Dockyard, UK, constructed in 1790 and the only one which is still producing rope commercially today (see these images) has an internal length of 346 metres (1,135 ft.). In the US, a 250 foot section of an early 19th century rope walk (the Plymouth Cordage Company Ropewalk) is preserved at the Mystic Seaport Museum in Connecticut.
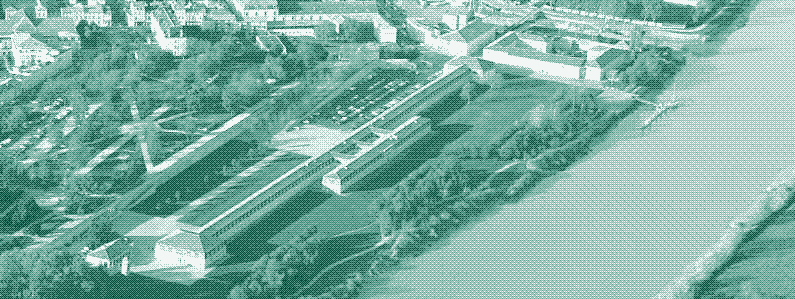
The largest rope walk still standing dates from 1666 and was in operation until 1867: “La Corderie Royale” in Rochefort, France. With an internal length of 374 metres (390 metres external length), it was the longest brick building of the 17th century (aerial view of it above, source) and could produce ropes with a length of up to 246 metres. (Twisting the strands into rope shortened the length of it, naturally. The final rope was about two thirds of the length of the yarns used.)
The software: knots
By themselves, ropes are essentially useless. They have to be tied to something (be it an object, another rope or to themselves) and therefore they need knots to function. A simple comparison would be that if ropes are considered the hardware, knots would be the software. While knotting technology must have been very simple in prehistoric times, it became a highly specialized art over time.
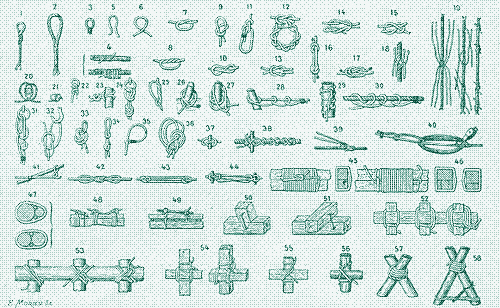
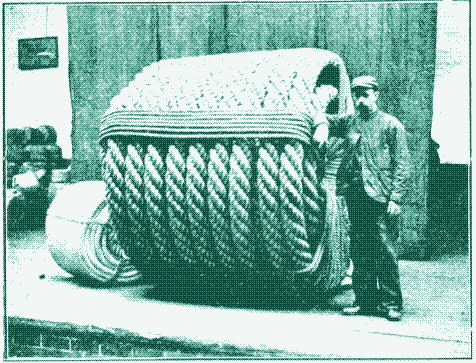
The sheer number and diversity of knots that was once in use would be bewildering to the modern city-dweller. About 4,000 different knots exist, ranging from the very simple to the extremely complex. Not so long ago, each profession or trade had adopted the knots best suited to its requirements, and knotting was part of their daily lives. Today, only campers, boy-scouts, climbers and sailors acquire some knowledge of this once imperative technology.
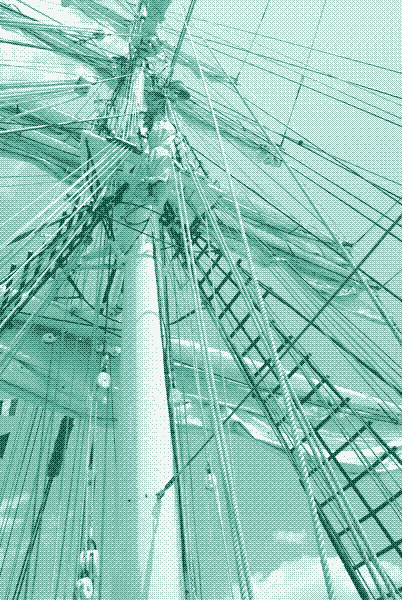
There are two reasons for the demise of knotting. Firstly, many technologies that were once dependent on ropes and knots have disappeared. These are most notably sailing ships, but we have also stopped hauling canal boats and using pack trains or catapults (we have bombers and diesel engines now), as well as hundreds of more mundane tools and devices that once made use of ropes.
The demise of natural fibres
Secondly, the hardware has changed. From prehistoric times to midway the 20th century, ropes were made from vegetable fibres (and to a much lesser extent from animal fibres such as sinews and hairs). Egyptian rope was generally made of papyrus plants or date palm fibre. In Eastern Asia, bamboo, grasses, and coconuts were used.
Hemp, which use originated in China in the third millennium BC, became for many centuries the material of choice for rope manufacturing in Europe and, from the 17th century onwards, North America.
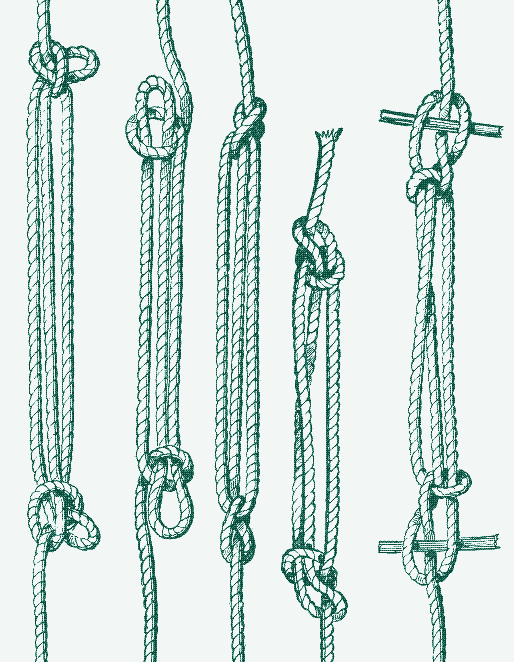
In 19th century Europe and North-America, hemp (and flax) were largely superseded by imported tropical fibres: mainly manila (made from the leaves of the abaca plant), but also coir (made from the shell of coconuts), sisal and henequen. Cotton and jute were also used to make (weaker and less durable) ropes.
Beginning in the second half of the nineteenthy century, many ropes made of natural fibres were superseded by “ropes” made of steel. Elevators, cranes and suspension bridges, for instance, are now fully dependent on steel “wire ropes”, while modern sailing yachts make use of steel wires. Gradually, wire ropes also supplanted natural fibre ropes for mining and mooring purposes.
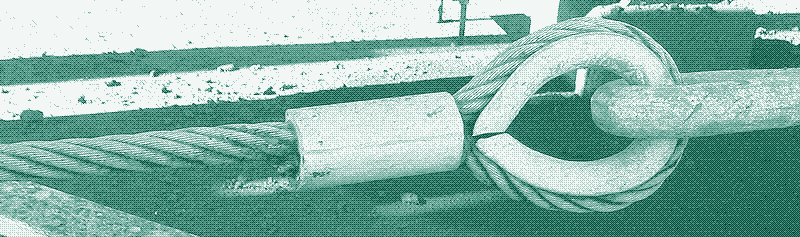
Where “real” ropes are still used, for example in the fishing industry, for water sports equipment, parachutes, hot air balloons (illustration below) or for mountaineering (including industrial rope access), they are now almost always made out of synthetic materials, based on refined oil - a trend that kicked off in the 1950s. Today, the market for natural fibre rope has all but disappeared.
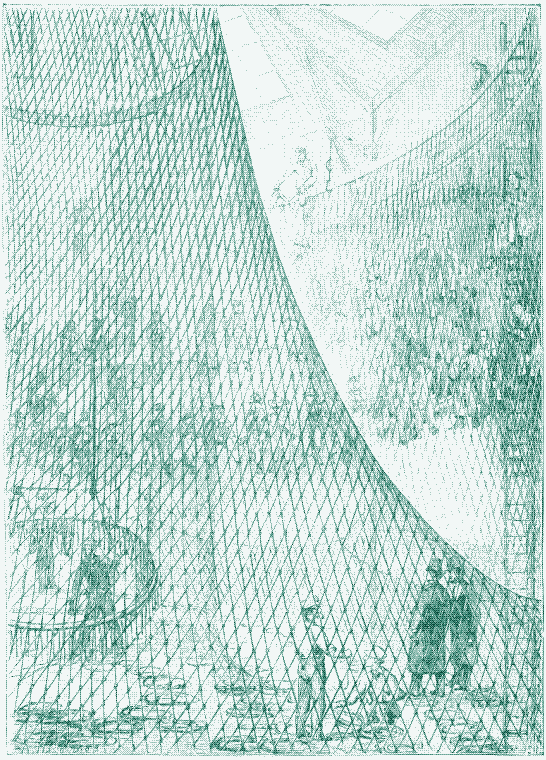
Polymer-based ropes are stronger and lighter than ropes made from natural fibres, naturally replacing them in no time. Nylon came out of the laboratory at the end of the 1930s, and today it is the most frequently utilized material for the production of ropes. Polyester and Polypropylene arrived on the market in the 1940s and the 1950s respectively - these materials are not as strong as nylon but much cheaper than natural fibre ropes.
Today we have - among many others - Kevlar, Technora, Twaron, Vectran, Zylon and Ultra High Molecular Weight Polyethylene ropes (the latter are 10 to 100 times stronger than steel). Amazon books arrive in boxes tied together with adhesive tape, gadgets come in boxes held together by plastic strapping. The only natural fibre rope that I could find in my apartment was the cat-scratching post.
Of course, contrary to natural fibre ropes, the manufacturing of synthetic cordage requires expensive, high-tech (and at present digitalized) machinery.
Knot-holding ability
None of these new materials is compatible with knots. This speaks for itself in the case of steel wires, adhesive tape and plastic strappings, but the same goes for synthetic ropes: most have very poor “knot-holding ability” - this is why shoelaces are mostly still made of natural fibres. Knots have thus been replaced by an array of other fastening technologies, made out of plastic, steel or aluminium (illustration below).
Moreover, most natural fibre ropes sold today when compared to those sold one hundred years ago are of inferior quality, and are more likely to be made water-resistant by the use of biocides and chemical preservatives instead of using tar (source, pdf).

Interestingly, natural fibres keep losing terrain to their synthetic alternatives. Manufacturing a wire rope is somewhat similar to making one from natural fibre: the individual steel wires are twisted into a strand, and these strands are again twisted around a core. Until recently, this core was made out of hemp, or another natural fibre, but these days this is becoming increasingly rare. Instead, steel or plastic (Polypropylene or PVC) cores are now commonly used. And if a hemp rope is still used as the core of a wire rope, it is impregnated with PVC (source).
Roped, wired, wireless
Synthetic fibres and steel might be stronger than hemp rope, but this progress comes with a price. Synthetic ropes release toxic fumes when they alight, they are not bio-degradable (which is why they don’t rot) and they cannot be recycled (some of them can in theory, but not nylon, which is the most used).
Natural fibre ropes, on the other hand, were extensively recycled throughout history, either for making new (lesser quality) ropes or to produce “oakum”, which was driven into the seams of wooden ships to render them water-tight.
Both steel and plastic ropes and wires are much more energy-intensive to produce than natural fibre ropes, and they are fully dependent on fossil fuels for their existence (steel could be produced by renewable energies, but in reality this does not happen). It also means that their cost is dependent on the price of oil, which is not the case for locally grown natural fibres.
In short, fastening technologies are now dependent on non-renewable sources, while natural fibre ropes and knots are not. This sounds familiar, because it is true for most of our modern technologies. Of course, because all our machines are adapted to stronger steel and plastic ropes we can’t go back to natural fibre ropes unless we adapt the machinery itself.
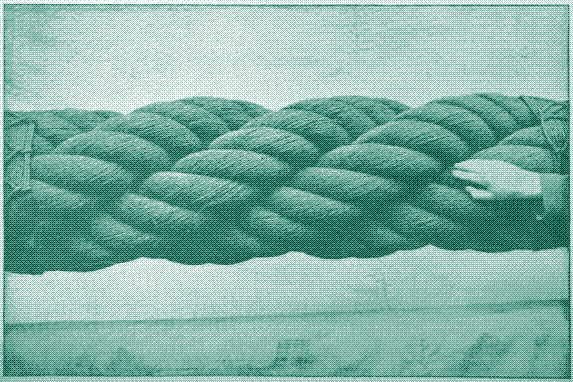
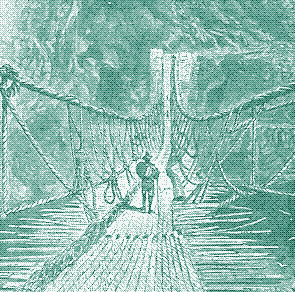
While ropes have disappeared, our society has become ever more “wired” - the arrival of electricity and modern communications technologies around the turn of the twentieth century have brought with them an explosion of wires or, more correctly termed, cables (because they always consist of bundles of wires).
While I was wandering around my apartment in search of ropes, I had no trouble finding cables. In just one hundred years, we evolved from a “roped” society to a “wired” society. And more recently we seem to have entered the “wireless” age, with mobile phones, internet over the airwaves and - if we let the engineers have their way - wireless electricity. Since all these new applications keep pushing fossil fuel consumption up, it is a safe bet that before the 21st century is over, society will return to ropes, ropewalks and knots.
Additional sources :
- How to tie the world together: Online knotting reference books
- History and Science of Knots, JC Turner & P van de Griend (1996), free access in some libraries - Rope, Invention & Technology Magazine (1991)
- Cordage and cordage hemp and fibres, Thomas Woodhouse (1919)
- Handbook of Fibre Rope Technology, H.A. McKenna (2004)
- The history of rope, Bill Fronzaglia (pdf) - Ropes and cordages (website)
- Noeuds et brêlages (La Nature, 1889)
- Corderie, Encyclopédie Diderot (1751-1772)
- Corderie (Planches), Encyclopedie Diderot (1751-1772), better quality scans here.
- How to build a ropewalk for ship models (diy)
- More primitive technology
- More articles on obsolete technologies.
Reactions
To make a comment, please send an e-mail to solar (at) lowtechmagazine (dot) com. Your e-mail address is not used for other purposes, and will be deleted after the comment is published. If you don’t want your real name to be published, sign the e-mail with the name you want to appear.
Reactions
humanoid
Brilliant.
Stephen Paulger
Interesting article. I don’t think knots are lost knowledge though, mountaineers and climbers still use a lot of knots.
M
You are amazing. Amazing. What a gift you give!
Kris De Decker
If this would be “the second demonstrably false statement” on this entire website (which has some 80 articles), you’re not getting me worried. Nobody’s perfect, and if I would not welcome criticism there would be no comment section.
But is the statement false?
“The low friction of UHMWPE fibres leads to poor knot-holding ability so don’t ever think about constructing your own dyneema sling - even with a super-duper-ultra safe knot. It will unravel when you least want it to.”
http://www.rockclimbingspain.com/Rock-Climbing-Protection.html
“Aramid fibers are high strength (5x stronger than steel), hold up to high tension quite well, and are quite UV and weather resistant (can’t even dye the fibers). Aramids under tension have low abrasion resistance and they generally have poor knot holding ability as they are somewhat slippery.”
http://forum.slackline.com/archive/modules.php?name=Forums&file=viewtopic&p=2055
“The decrease in strength with use is a worry for any of the Technora, Kevlar or Vectran materials. The Gemini and the Spectra-A are also extremely stiff and difficult to tie and untie.”
“The knot efficiencies for these materials, which are very low in new material, may be higher when the cord is used and more flexible, but further testing is needed to determine this.”
http://www.xmission.com/~tmoyer/testing/High_Strength_Cord.pdf
As far as I know, there is no scientific study that compares the knot-holding ability of natural and synthetic ropes. It could be that some synthetic ropes have better knot-holding ability than others. But the quotes above seem to indicate that there is an issue here.
Tree Beard
I do ground work for tree climbers and they use knots to tie ropes to limbs which they cut, then lower to the ground. They use part of the tree they are in, or an adjacent one, as a pulley to gain some mechanical advantage so they won’t be pulled out of the tree along with the branch they are lowering. The knots they use have to hold tight, not slip, and then be able to be easily untied when the limb reaches the ground.
The days of a climber tying his own harness out of rope are gone - haven’t seen that for 40 years. Only the old timers know how to do that. And if they are still climbing, they are using a commercially made sling.
Tree climbing usually involves the use of spikes and a belt or rope looped around the tree - ascenders are not usually used by tree guys. That’s all I know about that.
Kelly
In your list of uses of rope (and cord), many textiles could also be included as the technology is quite similar and many of the same materials are used (flax, hemp, cotton). The difference is really a matter of scale. Fibers are straightened (carded or combed), twisted (spun), then plied. Knots are used to make fabric and rugs. It has been argued that knitting is basically using two sticks to knot yarn into fabric, and some histories of knitting refer to “finger knitting” in which yarn is knotted with the fingers to produce fabric. Elaborate decorative knots of yarn and string are also used to make buttons and fasteners.
Smoke Eater
Knots were the hardest part of my Firefighter exam (for me, anyway). I went from hating them to loving them over time. We use the all the time in the fire rescue service.
Remarksman
“[…] the same goes for synthetic ropes: most have very poor “knot-holding ability” "
I’ll call BS on this one. Fisherman’s nets are now made out of synthetic rope. Have you ever tied and set a knot in a polypro rope? It doesn’t want to come untied. In lots of rope rescue experience (where we use all synthetic rope, which is nearly miraculously strong and useful) I’ve never seen a knot come untied.
I appreciate the articles on this site, but this is the second demonstrably false statement I’ve seen here, which is disappointing.
John
“There is no scientific study that compares the knot-holding ability of natural and synthetic ropes”
On the contrary, there is a substantial body of knowledge on the comparative properties of natural and synthetic ropes and the knots that are effective with them. Certain fibres are well known to be ‘slippery’ and require specialist knots. For example, fishermen have to use particular knots to tie monofilament nylon.
Climbing was only made possible as a safe sport by the development of synthetic ropes. These are designed with some stretch under a shock load to provide a soft(er) deceleration in the event of a fall. Natural fibres (except perhaps silk, which would be prohibitively expensive and would require far too many silkworms and mulberry trees!) do not have the necessary properties. However, climbers must use particular knots that will not slip on the synthetic braided sheathing of the ropes.
But it is simply wrong to say “None of these new materials is compatible with knots.” A wide range of synthetic ropes are used in numerous applications, and many of them are routinely knotted. All of the knots illustrated in the article can be tied satisfactorily with synthetic rope.
Many knots do significantly weaken the rope (of any type) in which they are tied, by measurable factors that have been thoroughly researched. To avoid this, for maximum strength it is necessary to use certain knots. Sometimes adding extra turns can help. Climbers tend to use figure-of-eight knots where other people might use an overhand knot. This is one reason why other fastenings are used instead of knots.
Another issue is untying a knot after it has had a load on it. For example, a bowline or a figure-of-eight knot will usually be easy to untie, even after heavy loading.
I also don’t believe that “the manufacturing of synthetic cordage requires expensive, high-tech (and at present digitalized) machinery”. In essence, aside from the production of the fibre, synthetic ropes can be laid in the same way as natural fibre ropes. A simple rope could be laid in a 17th century rope works whether its fibres were polypropylene or hemp. If the rope is a complex braided climbing rope, then the machinery to lay it will necessarily be more complicated, but this is driven by the rope design, rather than the fibre.
Of course, modern machinery will be much faster and reliable than having many men walking up and down a long building turning handles, so there will be a saving in resources here.
Finally, if synthetic fibres can be “10 to 100 times stronger than steel”, there are potentially enormous savings of resources, both in energy and material resources used in manufacture, and weight saved in use. And if the ropes last longer in service, that is a further saving of resources.
kris de decker
John, thanks for your comment. Let me correct my earlier statement: “As far as I know, there is no scientific study that compares the knot-holding ability of natural and synthetic ropes and costs less than 5,000 dollars”. It was much easier to find information on obsolete rope manufacturing than on contemporary technology. This kind of specific technical information seems only to be accessible through very expensive industry reports. Your comment gives the answers to the doubts that I had.
One thing, and you know it yourself because you insert the word “potentially”: If synthetic fibres can be 10 to 100 times stronger than steel, there are potentially enormous savings of resources, both in energy and material resources used in manufacture, and weight saved in use.
This did not happen. We have used the progress in rope technology mainly to design much bigger and more powerful machines and applications. Much larger fishing nets, for example.
Nick
Great article. I strongly believe there are some knots and rope lovers in Japan which will keep their tradition in very sophisticated knotting….
KTH
A basic clove hitch and and a Bowline should be a mandatory life skill, right after tying your shoelaces ;-)
Jesrad
I’m pretty sure the hemp-rope industry is still alive and kicking, to the delight of many a bondage enthusiast ;)
Dan Lehman
My “LPO” should be “PBO”, with a tradename “Zylon” –a VERY low-stretch, strong, & expensive (& UV sensitive) new material.
Toby
I believe many of the “slippery” new fibers like spectra etc. tend to be jacketed with less difficult synthetics like nylon and polypro, a good compromise solution. They are expensive, but there are applications where they make sense (I’m not a sailor, but I think modern rigging uses them, and I remember reading that some of the recent Mars landers used them as well - we may well have sent knots to another world!)
There are some other knots we climbers use that are well worth learning for everyday life, for example the Alpine Butterfly:
https://en.wikipedia.org/wiki/Alpine_butterfly_knot
There are multiple ways to tie it, and they are all quick and easy - an irresistible combination.
stephen
In the Boy Scouts (USA) in the late 1960s we made a length rope from twine as part of a merit badge project.
BK
Riggers I am a Show Rigger for Movies and Stage where it all originated from the sailing ships and then adapted to stage.
Ben
I really enjoy the content on this website. While reading this article I was thinking that the technique of making rope probably developed by braiding leather or entrails in an effort to reinforce a single strand that wasn’t strong enough for the task at hand and was later applied to plant fibers.
Judith Martin
No-one has mentioned circus. New circus is hip and fast, not only slick (Cirque de Soleil), and trapeze uses a lot of rope and knots. [21]: The backdrops for the Harry Potter movies were hung by ropes made in Somerset, at West of England Ropewalk, by a 5th-generation rope maker (sadly no longer around, but there might be a 6th generation). Then there’s Guédelon, the modern recreation of a mediaeval castle in France, where they have vast hand-made ropes for moving stones etc. in the construction. At the very least, the technology will survive in the heritage field - think of all the sailing ships fondly restored. Everything would be easier if makers were allowed to grow hemp for the manufacture, without government hysteria (thought I thought, #16, the bondage crowd preferred something smoother/harder ;-) ). A lovely website, thank you.
pulsatorius
There is an International Guild for Knot Tyers, IGKT. http://www.igkt.net/
Martin M
Fantastic article. Thanks for this. The writing style, varied use of images and, most importantly, level of detail is perfect. Thanks for sharing such great content!
Sean
Interesting article and some good points made.
I would add farmers to the groups who still extensively use natural fiber rope and knots. While it has, to some extent been supplanted by plastic rope, netting, or even wrapping with plastic sheets, natural sisal fiber ‘baler twine’ is still a popular option for holding together hay bales. Natural fiber is easier to cut and knot, less dangerous if accidentally eaten by livestock, biodegrades if left in a field, and its larger diameter reduces cutting and blisters on hands when one is lifting and throwing bales all day. (It is also more picturesque for public-facing uses.)
When a square bale is opened to feed to animals, it leaves two knotted loops of twine about 4 ft long; a highly useful length. It’s a rare farmer who will not have several loops in his pocket or tractor toolbox as he does his daily chores. He is skilled with a number of simple, but effective knots, even if he doesn’t know their proper names. He uses them throughout the day to close gates, temporarily repair fence, secure items to tractors or in truck beds,secure livestock, tie down tarps, or gather together wood and other bulky items for easier carrying.