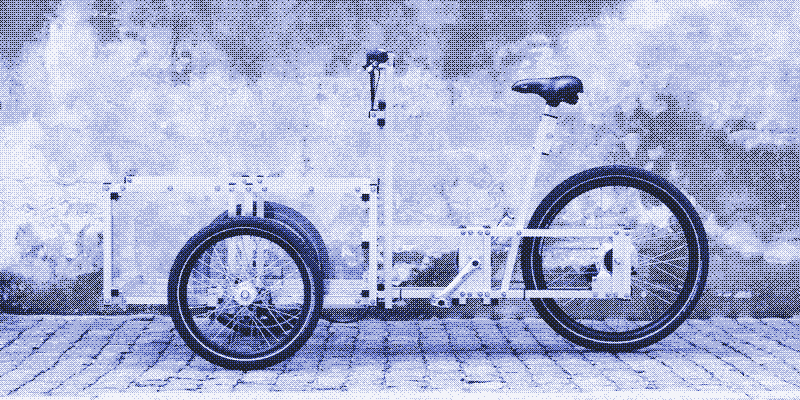
Following more than two years of research and development, the Danish art collective N55 has presented its modular cargo cycles: the two-wheeled XYZ Cargo Bike (90 kg loading capacity) and the three-wheeled XYZ Cargo Trike (150 kg loading capacity). The assembled versions sell online for about half the price of similar cargo cycles on the market. Because their design is open and modular, the XYZ Cargo Cycles are even cheaper to build yourself, and easy to customize.
XYZ Cargo brings together two technologies that have been praised at Low-tech Magazine: open modular hardware and cargo cycles. Modular consumer products, whose parts and components could be re-used for the design of other products, would bring important benefits in terms of sustainability, while they would also save consumers money, speed up innovation, and take manufacturing out of the hands of multinationals.
Cargo cycles, on the other hand, could handle an important part of cargo traffic in cities, paving the way towards sustainable and free-flowing traffic, while at the same time offering important economic advantages to tradesmen, artisans and service providers. The open modular cargo cycles built by N55 in collaboration with designer/artist Till Wolfer combine all those benefits.
Innovation
The market for cargo bikes is booming. This was the overall feeling at the International Cargo Bike Festival in Nijmegen (the Netherlands) and at the Berliner Fahrradschau in Germany this spring. The sales figures are skyrocketing and there is plenty of innovation going on.
A growing number of vehicles features an auxiliary electric motor, while many cargo trikes are now available with tilting mechanisms for fast cornering. Another innovation concerns the steering mechanism; several manufacturers have presented systems that obviate the need for a conventional fork, allowing for better control and increased cargo space.
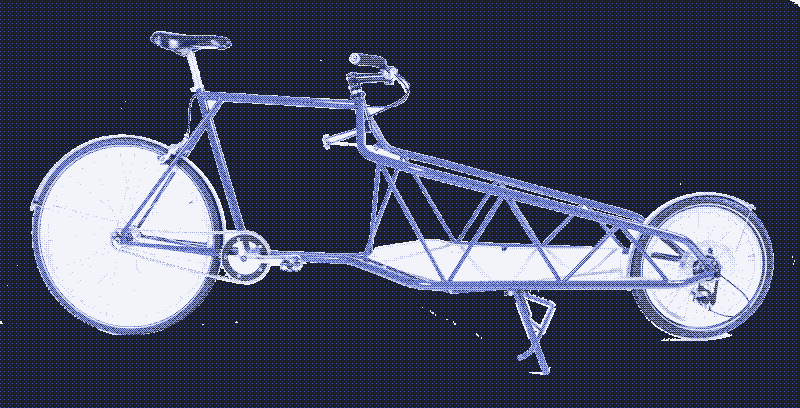
Unfortunately, these innovative vehicles often come with a hefty price tag. The prettiest cargo cycles such as the Elian Cargo Bike (a racing version of a cargo bike with steering in the front hub), or the electrically assisted Butchers & Bicycles MK1 (with tilting mechanism) set you back at least four or five thousand euro ($ 5000 - $ 7000), without any options.
These cycles are well worth the money, but they are obviously not within reach of everybody. Less fancy cargo cycles still have minimum prices of around 2,500 euro ($ 3,500).
Modular Cargo Cycles
This is why the affordable XYZ Cargo Cycles deserve our special attention. The assembled versions of the XYZ Cargo Bike and XYZ Cargo Trike sell online for 1,350 euro and 1,600 euro, respectively ($ 1900 - $ 2,220), which is about half the price of similar cargo cycles on the market. However, the cycles are not less interesting or innovative, on the contrary. For example, they feature a revolutionary steering mechanism inspired by motorcycles, which increases the cargo space considerably.
The low price is largely due to the modular nature of the vehicles. The XYZ Cargo Cycles are not built in a traditional way. Unlike the singular load-bearing tube seen in conventional bike structures, the main structure is an orthogonal spaceframe of standard aluminum square tubes of varying lengths in which holes are drilled.
The spaceframe is based on XYZ Nodes, which is a modular construction system developed by N55. It builds upon an old, well-known principle of joining timber or steel struts together. Structurally, the connection system shares similarities with lashed joints used for example in the traditional wooden frames seen in inuit kayaks, or with rivet constructions such as airplane hulls or old ship hulls.
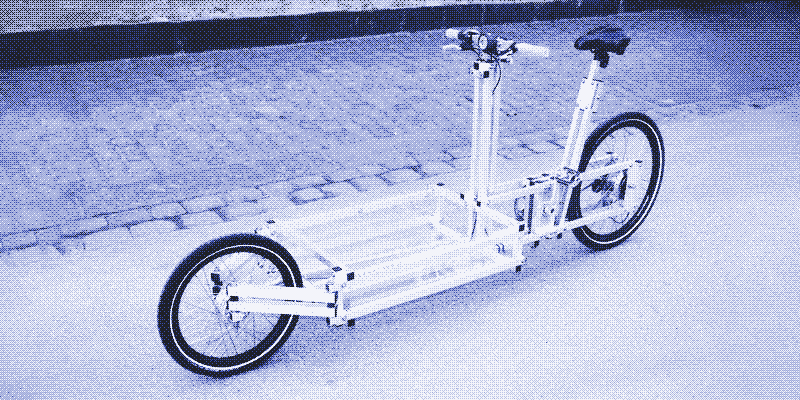
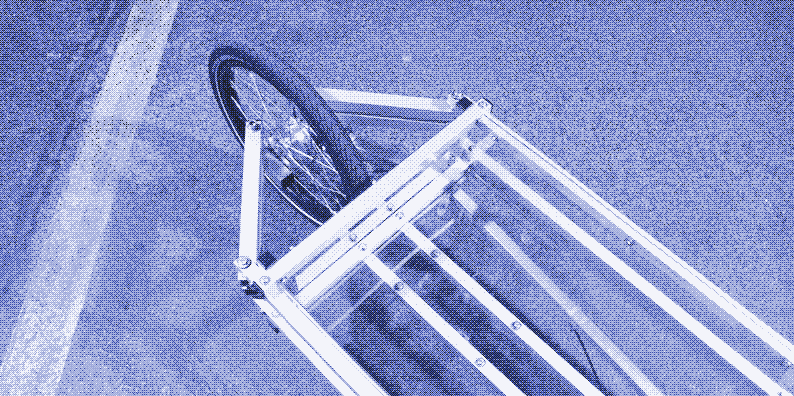
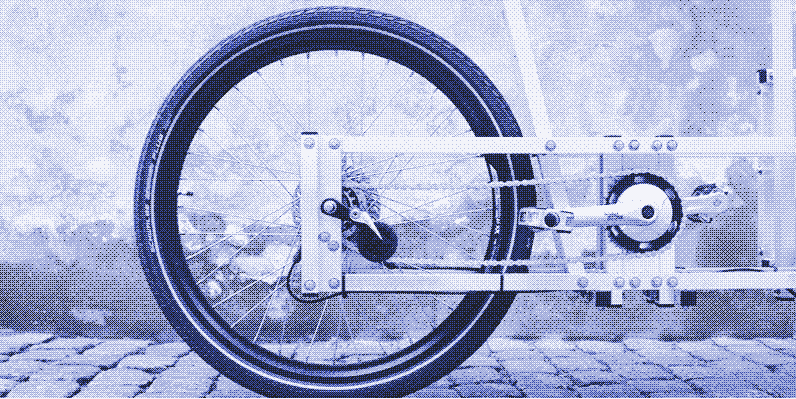
It’s a simple method of building light-weight things from durable materials in a low-cost way. XYZ Nodes forms rigid corners that become flexible when exposed to forces that would break other joining methods like a welded joint. The consequence is that it allows for rigid frames relying on corner connections that are not necessarily triangulated for greater strength, hereby leaving a free open space inside the frame. This made it possible to place gear wheels and chains within the frame, away from the users.
Easy to Build and Customize
The cargo cycles are open source concepts which you can modify yourself. The designs — including any new construction principle used in the system — and the XYZ construction and connection principle are open source provided under the rules of Creative Commons CC BY-NC-SA 3.0. Users are free to use available designs, as long as it is for non-commercial purposes and any use of the work includes proper credits.
This means that you can obtain the cycles even cheaper if you buy standard aluminium tubes and cycle parts, available all over the world, and build the cycle yourself. The frame is assembled using stainless steel bolts, washers and nuts. The assembling requires only simple hand-held, non-specialized tools, like a drill and a metal saw. No welding process is required.
Like all modular systems, XYZ nodes enable people to build things based on the principle of a few different parts repeatedly used to create an overall structure, similar to construction sets like Lego, Meccano and Erector. Because of the open and modular design, the XYZ Cargo Cycles are easy to customize and to rebuild. For example, a cover or a body to improve wind resistance and protect from the weather can be applied — turning the cargo cycle into a velomobile.
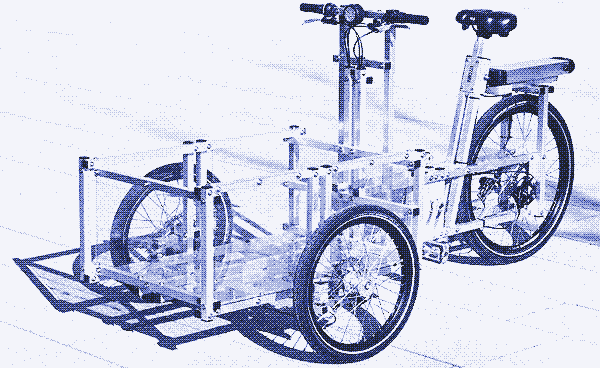
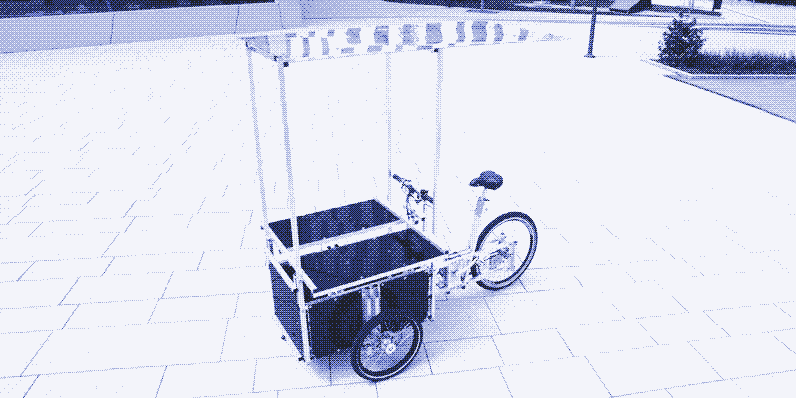
Several modules have been developed that can be put on top of the XYZ Cargo Trike to transform its functionality: a roof and table module, a passenger seat module, a kitchen module with table, roof and sink, and a platform module. The latter transforms the cargo cycle into a 1.5 x 3 m large movable space, while from a legal point of view remaining a bicycle. The platform module was used to create a ParkCycle Swarm, which empowers people to build an instant public park whenever and wherever they want to.
N55 is not a commercial enterprise, but a non-profit organization that aims to restore local production in a socially just and environmentally sustainable way. This is another reason for the modest prices. All the money earned with the sale of cycles will be invested in the further development of the technology. N55 gives away the building plans and offers the assembled bikes for a low price because they want to see as many of them on the road.
Available Models and Free Plans
The freshly opened webshop of XYZ Cargo offers two models for sale. The XYZ Cargo Bike weighs 26 kg and measures 245 x 56 x 105 cm (LxWxH), while the XYZ Cargo Trike weighs 34 kg and measures 208 x 94 x 105 cm (LxWxH). The cargo box of the Trike measures 55 x 80 cm and the plating is made of transparant Polycarbonate sheets. Both cargo models can be equipped with electric hub motors and batteries.
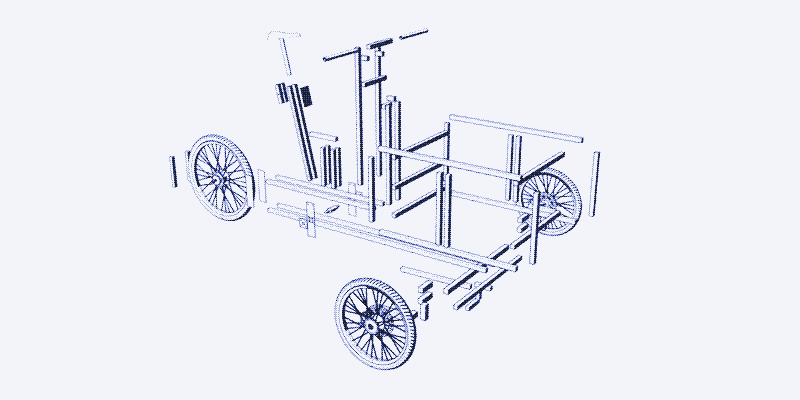
Two other vehicles have been produced, the XYZ One Seater (20 kg) and the XYZ Two Seater (34 kg). These pedal powered vehicles (with or without electric assist motor) are recumbent tricycles with one or two seats. The Two Seater can also be equipped with a cargo platform instead of a second seat. These cycles are not for sale, but the open designs are online at N55’s website. The XYZ One Seater’s construction drawings are available for download here and those for the XYZ Two Seater are here.
See and read more: XYZ Cargo / XYZ Spaceframe Vehicles / N55. And don’t miss the Eight-Wheeler Cargo Cycle, which got most of the attention at the Cargo Bike events.
Kris De Decker & Jo van Bostraeten
Reactions
To make a comment, please send an e-mail to solar (at) lowtechmagazine (dot) com. Your e-mail address is not used for other purposes, and will be deleted after the comment is published. If you don’t want your real name to be published, sign the e-mail with the name you want to appear.
Reactions
Roland Smith
@Jason (#2)
The biggest cost will probably be labor. There is a lot of assembly on these bikes.
Gear hub and shifter will be in the order of € 200. A single disk brake set will be € 60-100. 20" rims are around € 10-15 a piece. 20" tires € 12-20, inner tubes around € 5.
Jason
Something doesn’t seem ‘right’ about the pricing of these; I use similar aluminum and stainless steel bolts to construct solar panel racks and I find it hard to believe these runs over a few hundred; UNLESS theres some serious coin in the gearing/wheels; I’d like to see a price breakdown of parts in a parts list, X# Bolts, X# Lengths of aluminum, then the seat,etc. etc,.
Marc
I rode the recumbent cargo trike model about two years ago. I thought the idea is great but the trike is really awfull. Handling is downright scary even unloaded and I’m not scared very easy and rode only at 15-18km/h.
Since I own a recumbent trike (ICE Sprint) and use it for my daily commute (20.000km+ so far) I know quite well how a recumbent trike should handle even at 50-60km/h.
kris de decker
Since they presented the cycles “after more than two years of research and development”, I guess you were riding an early prototype.
salloignon thibaut
I’m also working on my own modular bike concept build from aluminium profils.
The frame is 100% mecanicly assembled without any drilling, that means you can reuse the tubes and connectors.
https://sites.google.com/site/cycleentransition/services/modular-bike
laceration
Bicycle frames take a lot of stresses, hence the welded frame. You don’t see a lot that varies much from the classic double triangle for good reason. I’m wondering about the robustness of this. That’s a lot of bolts to have to tighten. Every bolt on every bicycle needs to be tightened periodically.
thibaut
The bike is stiff, a little bit heavier than a regular bike (16kg). Diamond frame is great for sport bikes but we don’t need that mutch stiffness for utilitary bicycles. The bolts are “vibrarion ready”, the connectors are made for industrial machines with a lot of vibration. The first goal of this bike is to make a quickly and cheaply adjustable prototype.
It’s really great to add or remove pieces of frame or connect two bike together, make it long or short,… And every one can do it, so I hope to help people to be creative with bikes with this concept.
Mike Nomad
Great idea & concept.
Sleeves of a different material to isolate the bolt from the tubing would address stress at the join of different tensile materials, people over-tightening fasteners during the build, and perhaps the corrosion issues mentioned.
The only questions are: Which material for the sleeves (and) drill bigger holes or use smaller diameter bolts?
And, locking nuts w/ nylon inserts would keep things snug.
BTW, I don’t see any mention of torque settings…
zeev
this is a terrible idea for a bike, but a great idea for prototyping.
there are companies that make these types of struts that let people build mecano style construction at full scale.
there are MANY DEDICATED BLOGS TO TRIKES AND CARGO BICYCLES IN EUROPE AND AMERICA——and they look at the practical aspects of making these machines
unfortunately, because these cargo style hpv’s are not yet popular , they remain fairly expensive compared to ordinary bikes,but the prices are coming down radically.
the TRIKE is far more practical for hauling cargo than the bike because it does not have balance issues with windage and at slow speeds and acceleration breaking.
cargo bikes are not made for high speed cornering , so the only ‘high speed’ issues that a cargo vehicle has are breaking issues. the more weight you add the harder breaking is, especially downhill or in an urban setting where rapid breaking may be required.
there are substantial debates both in the bike world over the ’long john’ versus ’long tail’ design. but one thing is clear, the Single big wheel combined with load bearing small wheel has become the standard go to setup for both.
in the trike world, it has long been accepted that the 2 wheel in back ( delta) design is ideal for urban cargo whereas the 2 wheel in front with center of gravity VERY low to the ground is optimized for sport riding and speed riding ( with electric hotrodding trikes proving that a 4kilowatt small motor can easily propel a small unfaired trike to 90 miles and hour on a drag strip .
there are a few new innovators building fully double wishbone suspension systems for cargo/dual rider style urban trikes . these new styles allow the rider to sit high, with or without extra weight (as passenger and cargo) while retaining the benefits of 2 front wheel breaking and steering.
in the trike world ( motorized and nonmotorized) many years of experience have shown that the benefits and simplicity of the delta design which result from single wheel steering separated from leaf spring simple rear suspension) come directly at the cost of trading off better front steering with two wheel—and the simplicity of power transmission to one back wheel WITHOUT having to use an axle or differential that is the benefit inherent in the tadpole design)
furthermore the suspension of the front and back wheels are fare more complex in a tadpole design As well as the possibility of dual wheel transmission being very difficult to impossible.
many designers have tried innovating their way around the essential tradeoffs between delta and tadpole designs by implementing such designs as ‘rear wheel steering’ in tadpole designs. These efforts are generically failures and yet they are attempted AGAIN AND AGAIN. other exotic modification ‘solutions’ include the ’tilting’ back axis delta designs that have been tried many many times to find a way to improve the tipping tendency of delta designs at high speed. other have tried experimenting with very low center of gravity ‘delta’ designs and other even attempting to use tilting mechanisms for the back two wheel .
the problem of complexity is ever present in all of these pseudo solutions.
essentially —-the delta versus tadpole design tradeoffs are ‘mature’ in the engineering sense, and most all attempts at solving the problem leave much to be desired .
the modular cargo cycle above dispenses with any attempts at solving the problem with utilizing the tadpole design for cargo. and simply copies the designs of the past and existing front loading cargo trikes (see worksman cycles for existing front loader cargo style trikes)
in this way, they have chosen an inferior design , inherently limited to far slower speeds than a delta style urban cargo carrier—and have chosen to use expensive modular technology to bring down the cost of labor ordinarily priced into the bike’s retail price at delivery.
this is an exercise in helping people build their own devices, not in helping people who need cargo solutions find a highly superior solution as found in copying or even improving upon the modern high quality designs that already exist.
furthermore, the 800 pound gorrilla in the cargo bike and trike world is ELECTRIFICATION, which is already hitting new york city as pedicabs illegally add electric kits to their trikes, increasingly using the ‘direct’ drive clamp on motors which are concealed below the undercarraige, as opposed to the hub motors which are exposed in the front wheel of a delta pedicab—available for police to see them.
if modular design is a good thing, the question is for what is it good for? generically it is used for buildings and static objects.
modular toy and electronic kits are sold on the market for designing electronics education kits for children teens and adults for learning and experimenting with electronics. they allow you to make a multitude of objects and bring SKILLS directly to human beings for cheap, even helping people to learn how to fix things instead of throw them out and make them disposable.
with a modular bike kit, i’m not sure you are learning these skills on how to fix, design or otherwise ‘work’ on bicycles. this almost looks more like an attempt at ‘pre-fab’ bicycles that can be easily ‘put together’ by the user. i don’t see a big advantage in this when the parts themselves are not only more expensive but inferior in quality to less expensive standardized bicycle/tricycle components per pound of metal per unit of stiffness. bicycle tubing is generically the best design. modular I and T beam types components just don’t measure up in this basic performance metric for carrying a cargo load.
Andrew
I agree with many of the above comments.
When carrying serious loads, especially for custom purposes like street stalls etc, a stronger frame is necessary, requiring decent engineering. A modular frame like this would have to be heavily over build due to less optimal tube joining, load distribution etc.
Cost of the frame does not have to be a big issue. Most of the high retail prices are due to bouquet brands charging high prices just because they can. You can get frames mass produced in China like everyone else and have those (currently) $2000-$5000 bikes retail for $1000. At least you could, if there was enough of a market to build and sell them at sufficient volumes.
JohnMc
Note to authors, your reference to plans for the two open source bikes refer to the same set of plans.
Christina
Regarding salt water and aluminum: You can D.I.Y. anneal the aluminum… or apply paste wax meant for cars… or apply baby oil. Regarding screws versus welded: Washers made of rubber will absorb the vibrations, and also enable the screws a tighter fit.
Karl
I have tried to find 20" front wheels with disk brakes and a open axle of 12mm without any success. Such wheels are used in the cargo trike project.
Have anyone found such wheels?
Lehel Matyus
Why is the cargo area in the front and not in the back? just makes it harder to steer in my opinion. why not just have a normal bike pull a little wagon?
Steve
Great concept!
This might be a fantastic way to provide transportation to those with physical challenges. Each bike can be easily customized & adjusted as the user has changes in what they need. A welded frame is more efficient for some things and modular is good for others.
Bitex makes hubs for the front wheels but they did not return my email.
Sherwood Botsford
There is something wrong when any kind of bike costs a significant fraction of the cost of a car.
Assuming building out of steel, the price should be roughly proportional to their weight. A semi standard (not performance) car is about the same price per pound as hamburger. (Performance cars come in at prices comparable to good steak)
Since a bike has a smaller fraction of highly machined parts (not much in a bike requires sub thousandth of an inch tolerances) it should be cheaper per pound.
The pricing reflects that they are for all practical purposes hand made. To be viable, they need to become as cheap as a run of the mill bike.
That said, it may make more sense to make trailers instead of special purpose bikes. I see families here pulling around a 2 kid trailer when going out. Now they aren’t cheap either, but I think a cargo trailer would be a matter of a pair of sturdy wheels, a plywood box, and a pivoting hitch.
Pascal De Wilde
Well, well… yes, this thread is years old, but if I came here, some others probably will, so why not revive it?
First, Sherwood, I understand your reasoning, but I also dare assume you haven’t hauled a trailer with a bicycle very often, or you didn’t really load it.
I’ve had the opportunity to compare trailers, two-wheeled front-loading and back-loading cargobikes (a very old original Danish Long John, a Mike Burroughs-built Eight Freight and a basic version Bullitt) and old school three-wheelers (triporteur, pivot under the load platform), and in my experience a trailer is just as hard to pull as an old-school threewheeler is hard to push. The Eight Freight and the Bullitt on the other hand were a pleasure to ride, even heavily loaded, despite the balance problems and the strenght required at very low speeds when heavily loaded (in the starting and stopping phases, and in urban manoeuvring). Even the Long John was fun, although I never really loaded it, because that old frame was seriously rusty - which didn’t stop me from sitting in it while my mate drove it, big fun in the big city :)
The only humane bicycle trailer to pull is the one-wheeled type that attaches to the rear heel axle of the bike (Bob Yak or similar), two-wheelers are torture. And when you say plywood, I assume with even more certainty that you’re a car driver - or you’ve never or rarely carried anything weighty with pedal power. Plywood is much heavier than steel,if you want similar strength. Let alone aluminium.
I’m not sure what you mean by “pivoting hitch”, but anything else from the Bob Yak system feels like driving your bicycle with the handbrake on.
It may be tolerable at low weight on flat runs without too much stopping and starting, but as soon as it goes up and down or stop and start, it’s a good means to convince you to buy a car instead. Unless you’re super-young, super-healthy, and of the masochistic super-sports type ;-)
Moreover, your comparison with car and meat prices gives me the idea we’re not exactly on the same wavelenght…
The production volumes and scale economies in the automobile industry are not comparable to the small scale production of cargo bicycles, so please do not compare apples and oranges.
I’ve worked on bicycles for more than forty years, I’ve been a bicycle mechanics teacher for about twenty, and I’ve built a few recumbent frames and done loads of custom modifications to ‘standard’ diamond frames. I know how much work it is to build a custom frame without automation, mass production or far eastern ultralow-wage slavery. You can’t do that cheaply.
(Mind you, the leaders in the cargo-bike segment most certainly have their frames built in Asia, as it’s the only place you can find competent welders working for ridiculously low salaries - and still they can’t benefit from mass production scale economies).
I am, right now, in the process of deciding wether I’m going into business building cargobikes in Belgium on a non-industrial scale, and that’s how I got here (but I’ve been a fan of LowtechMagazine for years!). I don’t think I can compete with all those outsourcers who get their frames built in Asia and use machine built wheels, even though I know my product quality will be equal or better. Handmade frames and wheels are expensive. Most customers don’t see the difference in quality before they’ve been able to extensively test and compare the bikes(let’s be frank and call them ‘mechanically stupid’ - they’re not educated to see the difference in the marketing media, they need physical experience and comparison to feel the difference, and that calls for more than a few miles of test ride). So you need to reach the very small ’niche’ that appreciates and can afford paying for your product. Not easy.
Getting back to the original topic, I have enough experience building and repairing (bent or broken) frames to say that this kind of bolted assembly will never be as stiff as a well-designed and correctly welded one. And the reason a bicycle frame needs to be stiff is this: you waste less pedal energy in warping. You can feel the difference on a ‘standard’ bike, when you go cargo the problem is much, much bigger.
What’s worse, I don’t see any form of triangulation in that frame. So it can’t be stiff in any way. Must be awfully floppy.
I’d like to try that thing for a laugh, but I doubt I’d appreciate it very much. An unloaded test ride will be enough ;-)
But, as said above, for experimental purposes, the system can be very useful. Only flaw is, it’s probably so floppy you can’t draw any conclusions from it.
Ivo Tichelaar
@Pascal, I have read some reviews from people that have ridden the recumbent XYZ trikes and they were positive. No mention of flex or low efficiency. Of course I don’t know how experienced those reviewers are. I know that I have always had good bicycles, but I currently have a stiff high tech bike and it is unbelievable how much stiffer and efficient that is. The type of attaching beams as used in the XYZ system is familiar from budding with wooden beams and is actually relatively stabile compared to other construction style. The square beams locked together tightly block movement in one or two dimensions. There are locations on the bike where three beams are interlocked that way, so in principle would block movement in all directions. I think when building with the explicit intention to take it apart and use the same beams for another construction, this makes sense. Even if it isn’t as good as a welded frame with lots of diagonals etc.