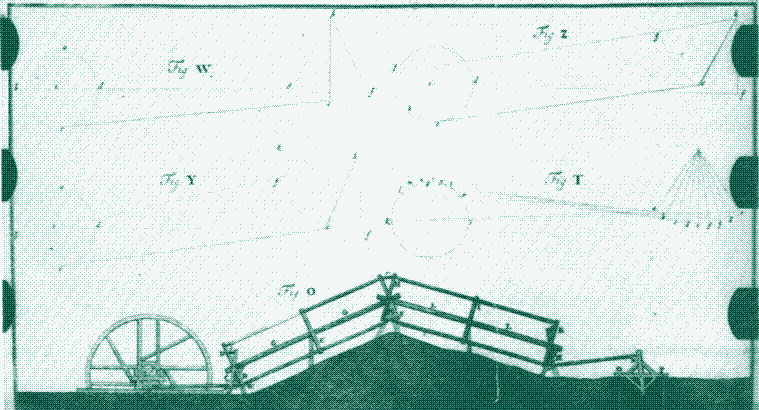
Long-distance power transmission predates the invention of electricity by almost four centuries. From the 1500s onwards, engineers developed mechanical power transmission and distribution technologies, called “Stangenkunsten”, that became ever more sophisticated.
Networks of pivoted, wooden field rods conveyed power from water wheels in the valleys to mining machinery up the mountains over distances of up to 4 km, operating pumps and bellows, hoisting ores, and transporting miners up and down shafts.
Later systems replaced wooden rods by steel cables. Many Stangenkunsten remained in use well into the twentieth century, long after the introduction of steam engines and electricity.
Revival of the Mining Industry
Electricity allows us to build power plants in distant locations because it is easy to transport using power transmission lines. Before the advent of electricity, however, the configuration for any wind or water-powered industrial process usually placed both the machinery and the power source in the same location.
A mill not only housed the sails or the wheel, but also the machinery that it operated. The power generated by wind or water was transferred to the machinery over a very short distance via a set of wooden gears or cranks. This meant that factories and workshops using wind or water as an energy source could only be operated in locations were a mill was available.
However, this was not always possible. Power production was especially problematic in the mining industry, since mines are situated in relation to mineral deposits, regardless of whether wind or water power is available. Mines needed mechanical energy for draining and ventilating mine shafts, for hauling up ores, for transporting miners, and for processing ores.
European mining activity had declined substantially after the demise of the Roman Empire, but an urban revival at the turn of the millenium brought a revival of the mining industry along with it. New mines were discovered and exploited, most notably in Germany. The Rammelsberg mines in the Harz Mountains were opened in 968 AD, followed by the Freiberg mining field in the Ore Mountains (“Erzgebirge”) in 1168 AD. Silver, copper and lead were the most important products of these famous mines, which would remain active for many centuries.
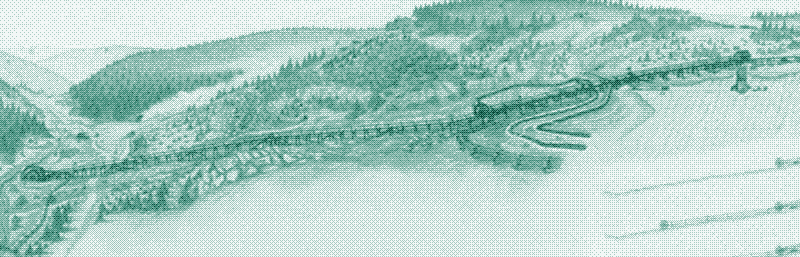
Initially, mining operations required relatively little energy, as ores were extracted from shallow depths. Hauling up the ores and draining the mine of unwanted water, if necessary, was done by means of human-powered machines. However, when the most easily accessible ore deposits became exhausted and miners were forced deeper underground, more powerful machines were needed.
The Rammelsberg mines resorted to this in the twelfth and thirteenth centuries, with the Freiberg mines following in the fourteenth century. The main problem the mines faced was drainage: once you dig shafts and tunnels below groundwater level, flooding becomes a constant concern. Hauling up water to the surface requires more energy as the mine gets deeper, as does hauling up ores.
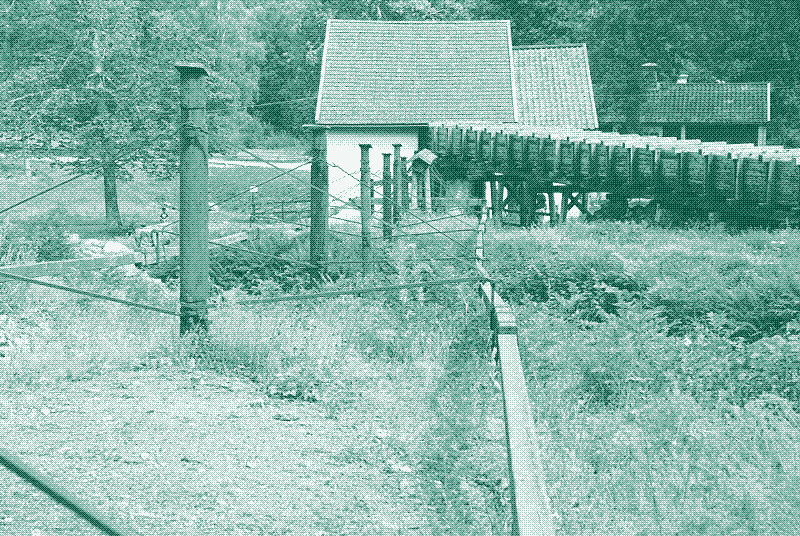
One solution, already applied by Roman miners, was the construction of drainage adits. These gently sloping tunnels, which could be many kilometres long, connected the mine and a neighbouring valley. Excess water drained into the valleys by gravity alone. However, this only worked as long as the adit could be built above ground level. If miners dug deeper than the valley floor, the problem persisted. Initially, the solution lay in more efficient pumps and in substituting animal-powered lifting machines for human-powered lifting machines.
However, horse whims were very expensive to operate and water-powered machines soon replaced them. (Wind power was not very practical for use in mining.) This implied, of course, that a running stream of water was available at the mine shaft. Most often, this was not the case.
Solution One: Bring Water to the Mine
The common method of sourcing water involved the construction of leats, derivation channels, tunnels and aqueducts. This solution also took care of energy storage by using dams and ponds. The Romans had done it before: one Roman gold mine in Spain (Las Medulas) used seven aqueducts, carved in the rocks, to tap water from local rivers. Starting in the late Middle Ages, ever more sophisticated water distribution networks were built.
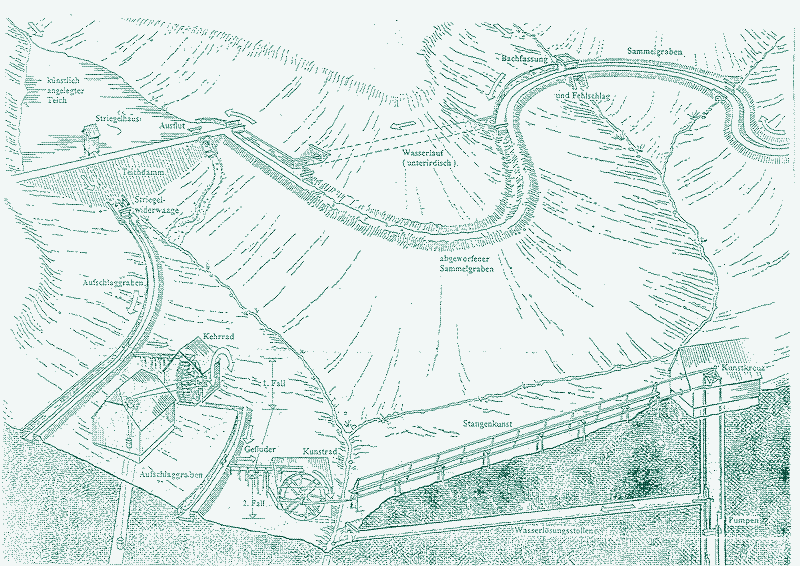
The water management infrastructure in the Freiberg mining field had some 50 km of covered ditches, connecting about a dozen large dams. Most of it was built in the sixteenth century, with further extensions in the eighteenth, nineteenth and early twentieth centuries — today, the system is used to supply drinking water to the city.
The water management infrastructure in the Harz Mountains, the largest pre-industrial water management system ever built for mining operations, had more than 600 km of canals and more than 140 dams. Nearly all the infrastructure was built in the sixteenth and seventeenth centuries, with some further improvements added in the nineteenth century. By 1868, the system powered 200 waterwheels.
Stangenkunst: Transporting Water Power Uphill
However, these hydraulic engineering works only made sense when the waterwheels were lower than the river because gravity distributes the water. If the machinery was on a mountain and the river in a valley, quite common in mining operations, a means for energy to be transported uphill was necessary. It was in this context that mechanical power transmission originated during the 1500s. Power was transmitted from a waterwheel in a valley stream to machinery on a mountain by means of long lines of linked levers, rocking back and forth on pivots. This is how it worked:
Wooden rods were hooked together lengthwise, extending from the waterwheel to the mine shaft. The rods were hung from wooden poles, set in the ground along their path at sufficiently close intervals to prevent any undue sag between the points of suspension. Wooden hangers that swung like pendulums were hooked to the top of the poles and to the rods, holding the line up and allowing it to swing back and forth in a reciprocating motion.
Each swing bracket acted as a lateral guide and a support, so that side-wind pressures did not deflect the rods far from a straight line. Friction was reduced to a minimum by the attachment of a strip of wood, against which the swinger rubbed only if deflected from a straight line. The size of the timber used for the rod lines depended on the power to be transmitted. A crank was used (video) to convert the circular motion of the waterwheel to a reciprocating motion that moved the rods back and forth — a mechanism that was already applied in Roman water-powered stone sawmills.
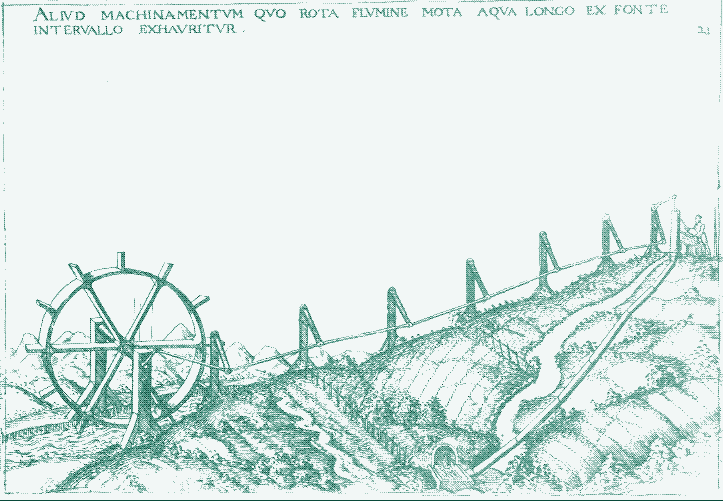
The system became known as “Stangenkunst”, where “Stangen” can be translated as “rods” and “Kunst” refers to a mechanism. Mining nomenclature is largely German in origin, because it was especially German metallurgists who pioneered and exported more sophisticated mining technology from the 1500s onwards, leaving their mark on metal production in large parts of Europe.
According to Graham Hollister-Short, one of the few historians who dedicated himself to the history of the Stangenkunst, the technology was probably invented in 1510 by Italian metallurgist Vanoccio Biringuccio, who designed a contraption that allowed a waterwheel to work the bellows at four separate forges at an ironworks. Though his system was used for distributing rather than transporting energy, some decades later the Germans applied the same approach to the transmission of mechanical energy over much longer distances.
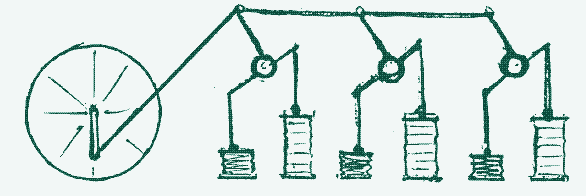
The first Stangenkunst was introduced in the Ore Mountains in 1550 and at the Harz Mountains in the 1560s. By about 1590, the Stangenkunst was introduced at the Kopparberg mines in Sweden, and by 1600 it had reached Italy, England and what is now Belgium. By 1700, the system was extensively used in North and Central European mines.
Vertical Power Transmission
The development of mechanical power transmission that followed the contours of the landscape, paralleled the development of a similar technology for vertical power transmission in mine shafts. These can only be understood in relation to each other.
Ever deeper mineshafts required a new power source to operate pumps and hoisting machines, as well as new types of pumps and hoisting machines. During the course of the fifteenth century, two new drainage machines appeared that allowed for deeper mining below adit: the rag and chain pump (around 1430) and the bag hoist (around 1470). By the 1530s, however, the limits of these machines had been reached. In his treatise on mine-pumping machinery, Graham Hollister-Short writes:
“Rag and chain pumps could raise water no more than 80 metres, while bag hoists, able to manage about 150 metres, worked so slowly that only modest inflows could be handled. As extraction neared these limits, the prospect of enforced abandonment of mines on a large scale must have appeared alarmingly close.”
Under these circumstances, a new type of pumping machine appeared: the rod pumping engine. In this machine, water was transported upwards via a series of communicating suction pumps and water boxes placed above one another. The basic design of the rod engine involved “the rotation of a horizontally acting assembly through 90 degrees so as to produce a vertically operating system”. In other words, it was a Stangenkunst turned on its side.
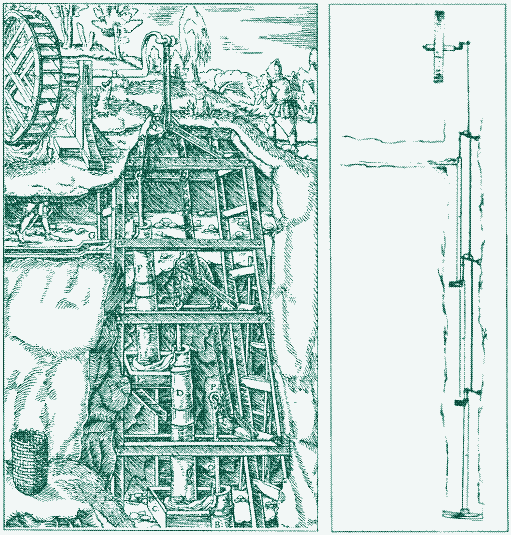
One of the first prototypes appeared in Georgius Agricola’s famous 1556 book on mining, De Re Metallica, in which the author notes that the machine had been around for ten years. The rod engine spread rapidly during the second half of the sixteenth century, gaining several improvements.
Horizontal “field rods” and vertical “shaft rods” were connected to each other by means of an “engine cross” (or “Kunst Kreuz”), which switched the line of motion by 90 degrees. One beam of the cross was attached to the field rods, the other held the shaft rods.
In fact, from the late seventeenth century onwards, many writers defined the Stangenkunst as the combination of field rods, shaft rods, and a power source (one or more waterwheels), instead of just referring to the reciprocating field rods. It is this definition which is now generally accepted.
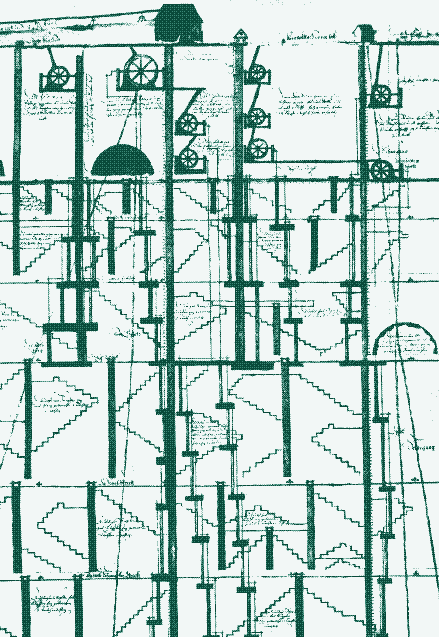
Round Corners, Up-hill, Down-dale
Over the course of three centuries, the technology used to transmit power from waterwheels to mineshafts became more sophisticated. During the 1590s, engineers developed a set of balanced rods, resembling a pantograph, which was more efficient than the single-rod machines because less energy was lost through friction. Single-rod systems remained in use whenever power was abundant, but the double-rod system offered great benefits when this was not the case. Graham Hollister-Short explains:
“There are now a series of pairs of legs, each pair carrying an iron axle on which the swing arm is mounted. The ends of the swing arms support the upper and lower field rods in a rather complex fashion. The ends of each swing arm are cut out to provide slots. The slots housed not only the rods but also the small pivoted pieces of hard wood on which they reciprocated.”
The efficiency of the double-rod system allowed for longer power lines. By the 1600s, the system was used to transmit energy over a distance of up to 2 km. By the 1700s, it reached up to 4 km.
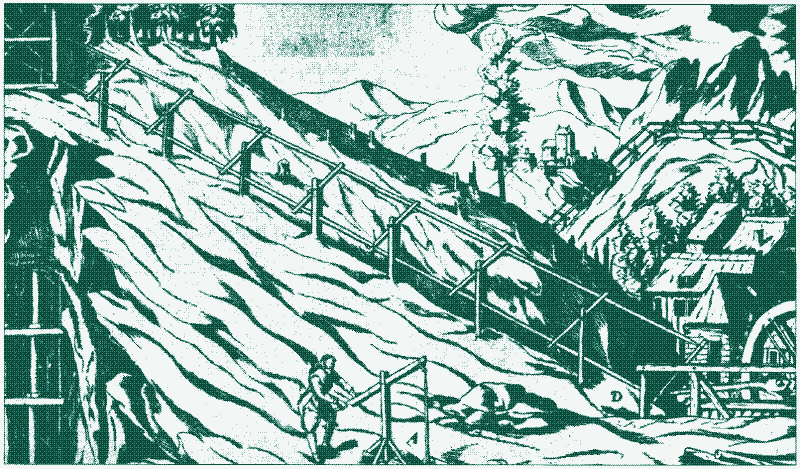
Initially, every Stangenkunst ran in a straight line, but by the 1640s, engineers had learned how to transmit power round corners as well as up-hill and downhill. They managed to round corners using a ‘Kunst Kreuz’ or ’engine cross’, a lever in the shape of a cross. It was this same component that was used to connect horizontal field-rods and vertical shaft-rods, but turned on its side.
The engine cross also allowed the attachment of a new branch of wooden rods to the line, so that one waterwheel could power machines in several locations. V-rods allowed for a change of direction up or down a slope.
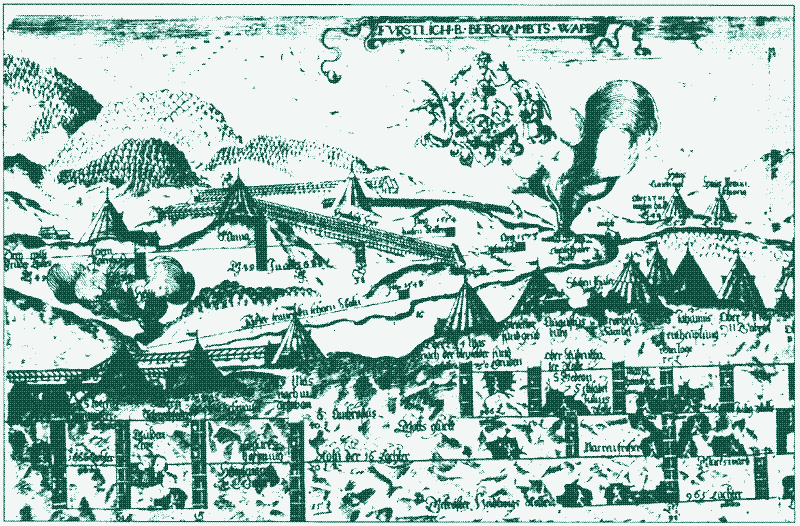
While most Stangenkunsten were used to drive drainage pumps, they were also connected to bellows for ventilating mine shafts, and to pestles for processing ores. In order to further improve the scope of power transmission, the Stangenkunst could be combined with water management infrastructure; for instance, an aqueduct was used to supply a waterwheel which operated a Stangenkunst. Finally, even the horse whim was integrated in the power distribution network by connecting it to a Stangenkunst.
The Hoisting Machines of Christopher Polhem
The water-powered machines designed by Swedish engineer Christopher Polhem between 1690 and 1710 further extended the possibilities of the Stangenkunst. On the one hand, Polhem built several ’traditional’ Stangenkunsten for Swedish mines, connecting pumps in mine shafts with waterwheels up to 2,500 m away. The picture below shows the rods of a Stangenkunst at the Bispberg mine. Polhem used a double set of wooden rods, which sat parallel to each other. The system is similar to the pantograph system, but turned on its side and with metal hangers instead of wooden ones.
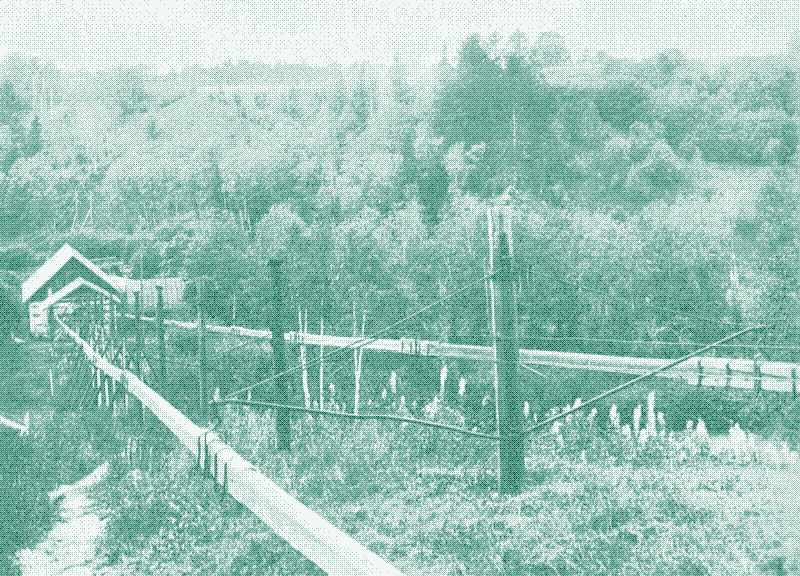
On the other hand, Polhem also constructed rod systems for hoisting up ore from mines shafts. Strictly speaking, these were not Stangenkunsten (they were called “Hakenkunsten”), but the design principle was nearly identical.
The first Hakenkunst was completed at Blankstöten in the Falun copper mine in 1694. The water-powered machine hoisted buckets loaded with ore out of a mine shaft, carried them to a dump, emptied them, and automatically returned the empty buckets to the mine. The whole mechanism was operated by reciprocating rods.
The energy from a waterwheel was transmitted via horizontal rods to the mine shaft. The horizontal rod was joined to two pairs of hooks furnished with vertical poles suspended into the pit. Buckets were hooked onto the poles at the lowest level, and then lifted vertically to a higher pair of hooks by the alternate motion of the pairs of poles. This motion continued until the bucket was raised up the surface. The buckets were emptied by means of an iron chain which hooked onto the bottom. The vertical poles were 60 metres long and had 15 pairs of hooks.
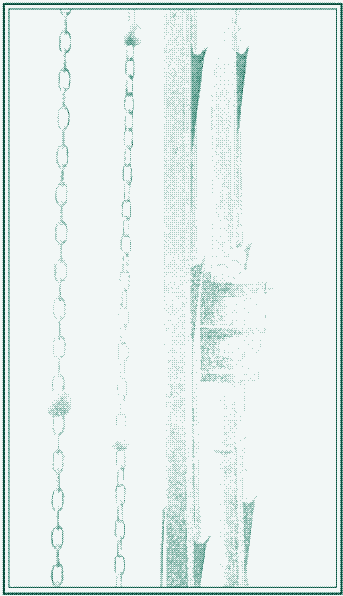
A similar hoisting machine was completed in 1698 for the Humboberget mine. This machine consisted of two sets of poles with attached hooks. One set brought the loaded carriers to the surface, while the other brought the empty carriers down the mine. In 1701, Polhem completed another hoisting machine for the King Karl XI shaft at the Falun mine. He used two rope drums for raising the ore barrels, which were rotated by a complicated wooden rod transmission from a reversible water-wheel with one crankshaft.
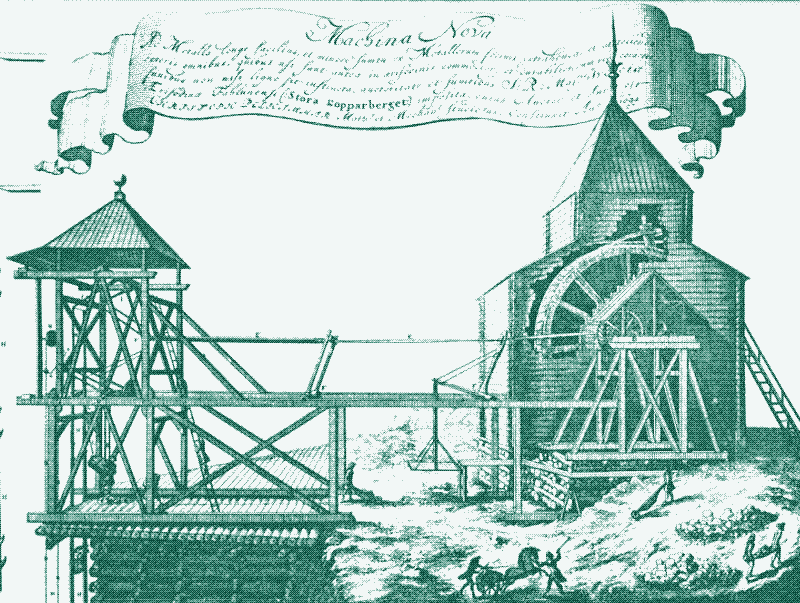
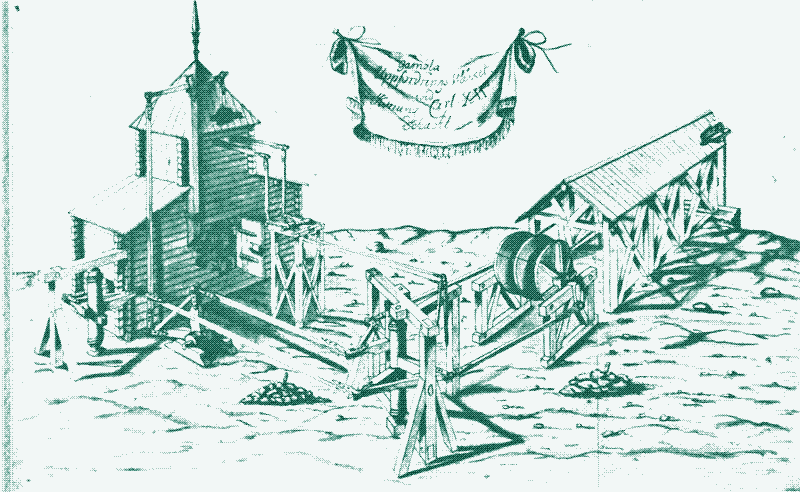
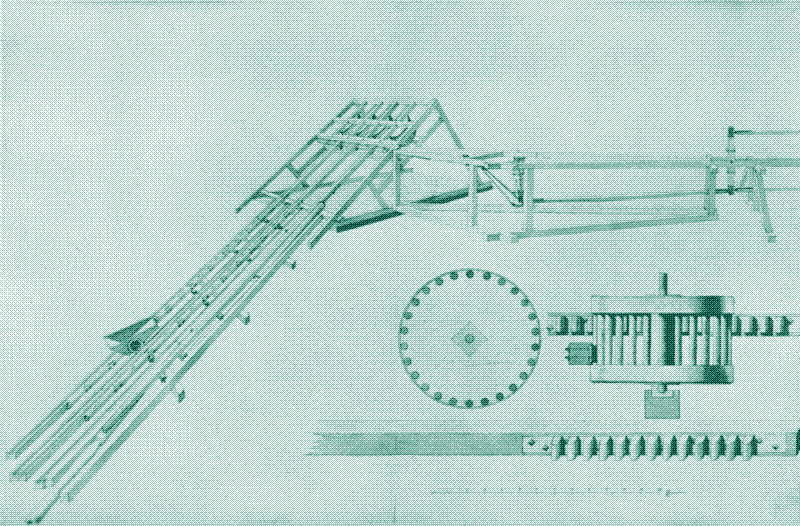
Man Engines
As mines became deeper, miners needed more time to descend and ascend mine shafts, and it could take up to two hours to ascend a mine which was 500 to 600 m deep. This led to the development of the “man engine”, also known as the “power-ladder”, which was another adaption of the Stangenkunst. The principle of operation was identical to that of the bucket hoists designed by Polhem, but applied to the transportation of miners. The man engine allowed the miners to ascend and descend the mine about three times faster and with less energy.
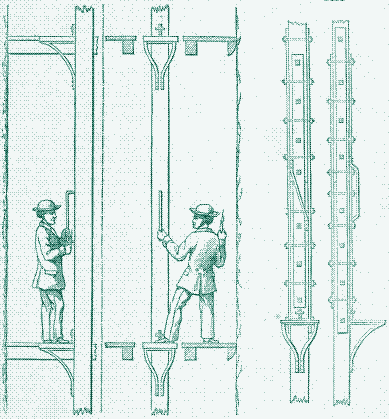
The first man engine was installed in 1833 in the Harz mining region. From there the design spread to Belgium, England, Austria-Hungary, Norway, France, Australia, and the United States. In total, more than 100 man engines were built from the 1830s to the 1880s. The average man engine reached a length of 400 to 500 m, with the longest reaching 1,009 metres in 1883. It was not always necessary to hang new rods in the shaft, as the rods needed for pumping could be used at little increased cost.
Man engines were built as single or double-rod systems. In the first case, the single rod was furnished with steps, while a series of platforms was fixed at different levels of the shaft. In the second case, miners jumped between platforms from two reciprocating rods. The miner, quitting one step, waited on the platform until the next step reached him. The rods, which were fastened together and reached to the bottom of the mineshaft, offered a reciprocating motion of typically 3-5 m. (These animations show how double-rod and single-rod man engines work). Counterweights — large boxes filled with stones — were installed in order to avoid the full weight of the shaft and men weighing on the top linkage.
Single-rod engines could be used simultaneously by miners ascending and descending, provided that there was sufficient room upon the fixed platforms, while double-rod engines did not have this advantage. The person operating the engine regulated the supply of water according to the number of miners ascending. For descent, no power was required to set the man engine in motion thanks to gravity. Descending miners could also raise the men who had finished their shifts by gravity alone, with the waterwheel only regulating motion and reducing friction.
Stangenkunsten during the Industrial Revolution
Steam engines started replacing waterwheels from the 1860s onwards. Contrary to waterwheels, steam engines were not dependent on the proximity of a stream or river, and could thus be located close to the mine shaft. This eliminated the need for mechanical power transmission. Furthermore, steam engines could be placed at the bottom of the mine to power the pumps directly, making the vertical transmission of power redundant.
However, the Stangenkunst did not disappear. On the contrary, many systems remained in use well into the twentieth century, long after steam engines had been replaced by gas engines, petrol engines and electric motors. Moreover, new systems continued to be built. In fact, most Stangenkunsten appeared after, rather than before, the invention of the steam engine.
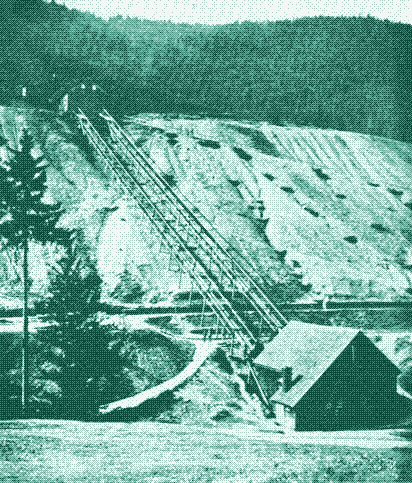
There were three reasons for the persistent use of this technology. For one, not all regions were quick to replace waterwheels (and wind mills) with steam engines. By 1900, the mine shafts in the Harz Mountains were more than 1,000 m deep, and both suction pumps and man engines were still powered by waterwheels and wooden field rods. This was probably because the technology worked well, suggests Robert Mulhaus in his treatise on mine pumping technology:
“The connection between the urgency of the problem of mine drainage in England, and the invention of the steam engine, has often been suggested. Perhaps the ‘backwardness’ of Germany in steam engine experimentation, and later in the introduction of the Newcomen engine, was to some extent due to the adequacy of existing machinery to meet the problem of mine flooding, for it is not clear that this problem existed on the continent.”
In the Harz Mountains, some Stangenkunsten powered by waterwheels operated until the 1970s. Even on the British Isles, which were at the forefront of the Industrial Revolution, some water-powered Stangenkunsten could be seen in the 1940s.
Stangenkunsten on Rails
A second reason for the survival of the Stangenkunst was the evolution of the technology during the Industrial Revolution. Most improvements were made possible by the availability of much cheaper and more durable iron and steel.
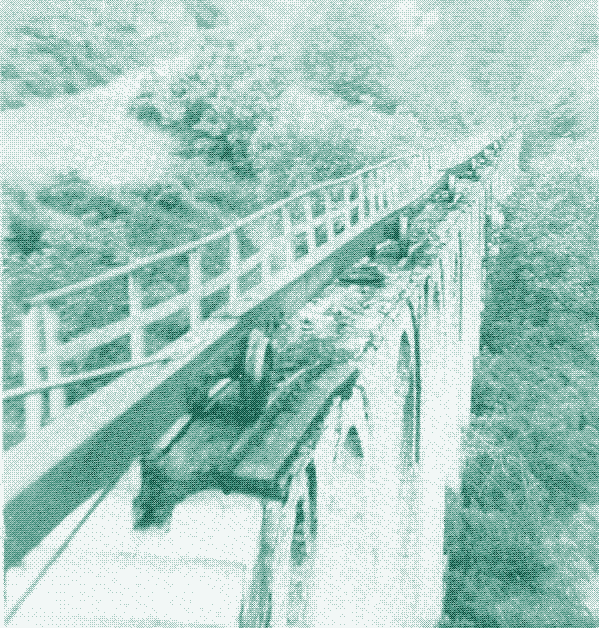
One such innovation was the use of rails, which reduced friction and made it possible to transmit greater amounts of power. (A similar innovation was applied around the same time for turning windmills towards the wind). A good example of this is the Lady Isabella waterwheel on the Isle of Man — one of the most powerful water wheels ever built. It operated from 1850 to 1929, powering mine pumps up to 200 m away by means of wooden rods, and transmitting about 150 horse power. The wooden field-rods, which ran over a viaduct and worked to and fro with a 3 m stroke, were not supported by metal hangers but ran on wheels, which in turn moved back and forth on rails.
Steel Cables Replace Wooden Rods
The most important innovation, however, was the replacement of wooden rods by round iron bars or steel cables with forged eyes at the end. These metal rods, rocking back and forth, lay either in grooved wheels, which revolved in the tops of forked posts, or were supported by rocking posts. Angle bobs (supported by wheels running on rails) drove the field-rods around corners, while V-rods changed their direction down or up a steep slope. The four pictures below show some examples of their use in England. These devices are part of a Stangenkunst powered by waterwheels and used to drain mines:
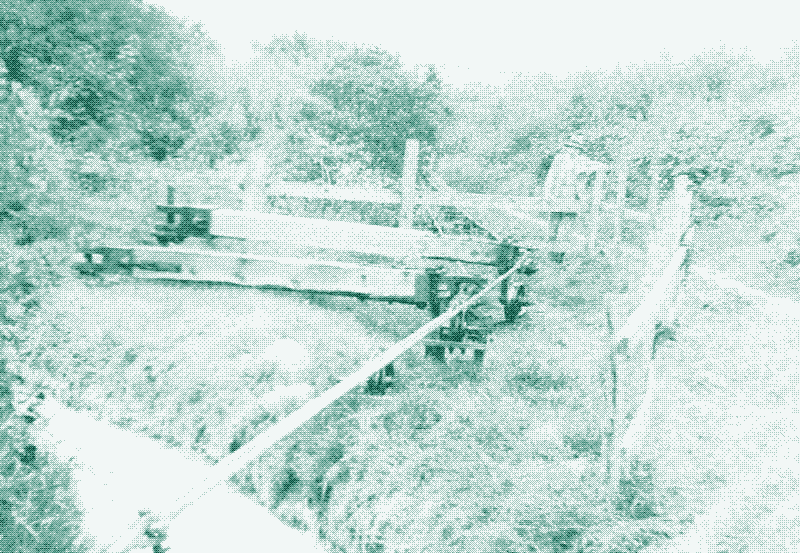
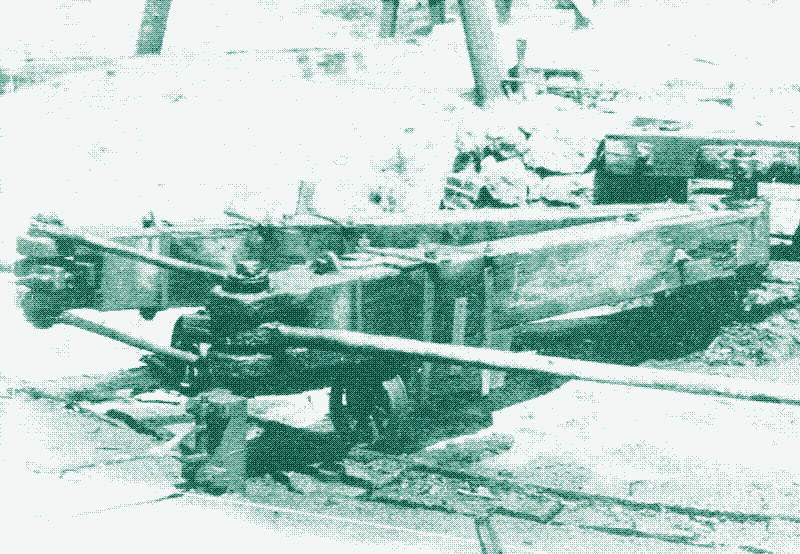
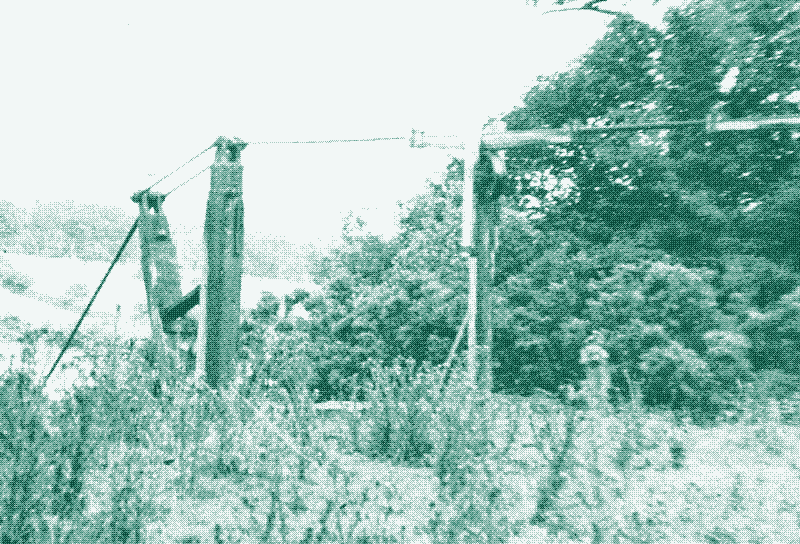
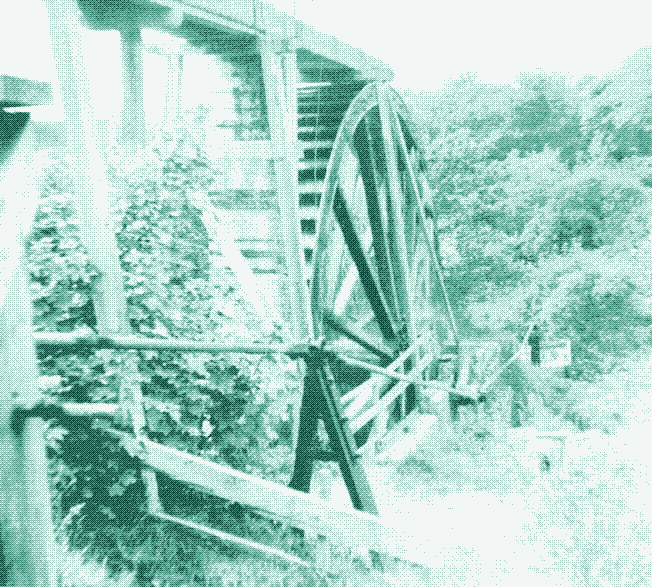
Clay Works in 1935. Lines of rods entirely supported on rocking posts have been used elsewhere. Image: “Steam engines and waterwheels: a pictorial study of some early mining machines”.
The use of metal rods was more durable, less maintenance-intensive, and allowed for a more flexible system when transmitting mechanical energy over long distances: the steel or iron field rods could easily pass through roofs, bushes, forests, and tunnels. An account of this is given in Frank D. Woodall’s book the 1975 book Steam Engines and Waterwheels: a Pictorial Study of some Early Mining Machines:
“Even in 1946 it was still possible to see waterwheels driving pumps in the china clay works of Cornwall. At Wheal Martyn near St. Austell a 35ft diameter waterwheel drove a remarkable layout of rods. Following them away from the wheel one soon found difficulty, for the rods passed through the roof of a large clay-drying shed. Making a detour the observer saw a smaller waterwheel and the rods from the large wheel close at hand. A footpath, presumably used by the man who oiled the wheels in their forked posts, helped one to follow the rods through a thicket of prickly bushes to another hazard. The rods worked in a low tunnel through a mass of made ground.”
As Woodall notes, systems like this were still in use in the 1970s:
“Not many years after Wheal Martyn finished working the pumping shaft was caved in during WWII the only other set of flat rods, at Carloggas near St Austel, fell into disuse, but although it was the last flat rod system to work in Britain a similar system remained in use in Germany. Two waterwheels each driving two lines of rods were seen working at Bad Kreuznach in 1965. The rods were not on wheels but on inverted pendulums and looked to be of recent construction. Other waterwheels driving pumps can be seen at the salt springs in the Bavarian town of Bad reichenhall.”
The Stangenkunst Embraces the Steam Engine
The third reason for the sustained popularity of the Stangenkunst was the fact that field-rods were combined with steam engines (and later also gas and petrol engines as well as electric motors) instead of waterwheels. In this way, one steam engine could operate multiple pumps, which was cheaper than setting up a steam engine (or other power source) for every mine shaft or pump.
Apart from pumping water out of mine shafts, or operating man engines, this configuration found a new application in oil production, initially in the United States but eventually all over the world. It was in the oil industry that the Stangenkunst reached the pinnacle of its development. See part 2: Jerker line systems.
Sources:
- “The first half century of the rod-engine (c1540-c1600)”, Graham Hollister-Short, in “Bulletin of the Peak District Mines Historical Society”, Vol. 12, No. 3, Summer 1994. Historical Metallurgy Society Special Publication: Mining before powder. - “The vocabulary of technology”, Graham Hollister-Short, in “History of Technology”, second annual volume, A. Rupert Hall and Norman Smith, 1977
- “Mine pumping in Agricola’s time and later”, Robert P. Multhauf, in “Contributions from the museum of history and technology: paper 7”, United States National Museum Bulletin 218, 1959.
- “Polhem, the mining engineer”, Herman Sundholm, in “Christopher Polhem, the father of Swedish technology”, William A. Johnson, 1963 (original version in Swedish, 1911)
- “Steam Engines and Waterwheels: a Pictorial Study of some Early Mining Machines”, Frank D. Woodall, 1975
- “Dictionary of arts, manufactures, and mines containing a clear exposition of their principles and practice”, Part 3, Andrew Ure, 1875
- “Fahrkünste - vom Harz in die Welt”, Thomas Krassmann, 2010
- “Stronger than a hundred men: A history of the vertical water wheel”, Terry S. Reynolds, 1983
- “De Re Metallica”, Georgius Agricola, 1556
- “Histoire générale des techniques, Tome I, II, III.”, Maurice Daumas, 1962
- “Contemporary reviews of mine water studies in Europe”, Christian Wolkersdorfer and Rob Bowell, in “Mine water and the environment”, 2005, 24.
- “Revierwasserlaufanstalt Freiberg” & “Lower Harz Pond and Ditch System”, Wikipedia in English and German, retrieved December 2012.
- “A textbook of ore and stone mining”, Clement Le Neve Foster, 1894
Reactions
To make a comment, please send an e-mail to solar (at) lowtechmagazine (dot) com. Your e-mail address is not used for other purposes, and will be deleted after the comment is published. If you don’t want your real name to be published, sign the e-mail with the name you want to appear.
Reactions
Minor Heretic
I read somewhere about the Amish in Pennsylvania transmitting power from small waterwheels with pairs of ropes. The ropes would be suspended off the ground on wooden T posts, with the ropes going through greased leather guides. Each rope would pull alternately on either end of a horizontal lever.
On a more modern scrapyard note, a friend told me about a junkyard owner who built his own waterwheel and transmitted the rotational motion through a series of scrap steering wheel assemblies up the hill to his shop.
Rui
Your blog is simply wonderful.
Thank you so much for the good quality articles.
Ruben
Kris, this is amazing. Do you have any idea of the efficiency of these systems?
Kris De Decker
These systems can be more efficient than electricity over short distances, say 1 or 2 km. In the next post we’ll discuss efficiency when we talk about the improved systems from the twentieth century.
Chris Hall
Great post Kris - most informative. I had no idea about Stagenkunst.
Roy
Amish commonly uses this in Pennsylvania
AT
“Single-rod engines could be used simultaneously by miners ascending and descending, provided that there was sufficient room upon the fixed platforms, while double-rod engines did not have this advantage.”
It appears to me that double-rod engines would also have this advantage.
Shyam
Your blog is so simply with beautiful.
Thank you so much for the good quality articles.
bas
movie of stangenkunst
https://www.youtube.com/watch?v=ycN8nR9SD4w
red
There is an historical restoration of a jerker rod system serving three oil wells at Moraine State Park between Butler and Newcastle, PA. A shed houses a restored Bessemer gas engine that powers the jerker gearing in an adjacent shed using a wide drive belt. Three rods leave the gearing house in different directions. Each is supported by a minimum of three tripods between the shed and the well. I think the maximum rod length is about fifty feet.
It appears that this may be powered up from time to time during the summer for demonstrations. One of the well heads appears to work; at least there’s a barrel there to receive the pumped liquid.
Michael Kesper
A better plural form would be Stangenkunstwerke (Kunstwerk = artwork). Stangenkunsten sounds totally blinkenlights-speak.
Martin
Why did they move from cogwheels (I have seen some in medival water mills) to those connections? The rod of a cogwheel seems a pretty analogous contraption.
Melwin S Fernandez
I was looking for some idea to transfer reciprocal motion over some distance, after going through it seems wire ropes/cables do well.
Moritz Moeller
I always wonder how German words end up with these weird changes when they get replicated in English. It seems someone got it wrong and other authors just replicated (incl. this one). It’s Stangenkunst (no ’en’ postfix)[1]. This literally translates to “the art of rods”.
The postfix makes it sound like the plural of the word in a Scandinavian language or maybe Dutch. But it’s neither. The German plural (not used) would be Stangenkünste (Stangenkuenste, with the umlaut written out). This would translate the “arts of rods”
[1] https://en.wikipedia.org/wiki/Flatrod_system