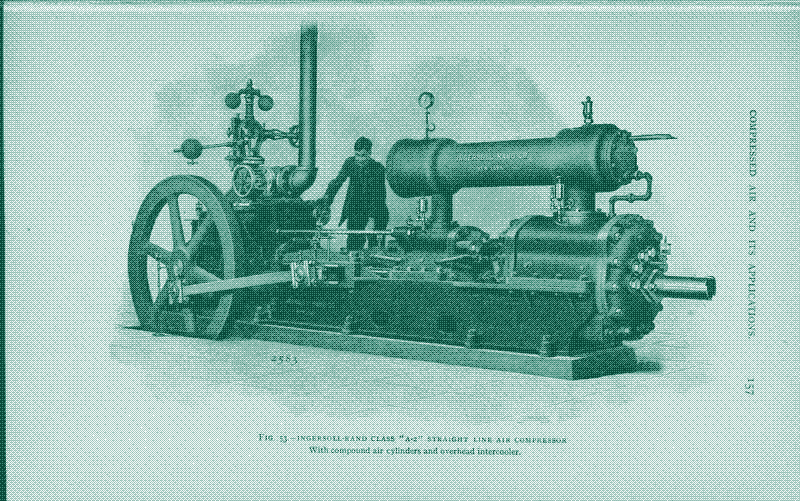
Le stockage d’énergie par air comprimé (CAES - Compressed Air Energy Storage) est un élément clé d’un réseau électrique renouvelable, car il pourrait stocker à grande échelle l’excédent d’énergie des éoliennes et des panneaux solaires. Cependant, sous sa forme actuelle, la technologie souffre de pertes énergétiques importantes et dépend du gaz naturel pour fonctionner.
Il suffit de jeter un oeil sur la longue histoire, vieille de 4000 ans, de l’air comprimé pour montrer que ce n’est pas indispensable. Bien que nos ancêtres utilisaient des technologies avec des rendements énergétiques moins bons, ils se servaient de l’air comprimé de manière plus intelligente ce qui leur permettait d’avoir moins de pertes liées aux conversions d’énergie et d’être indépendants des combustibles fossiles.
Les systèmes à air comprimé du passé semblent détenir la solution pour concevoir un système de stockage d’énergie low-tech, bon marché, robuste, durable et relativement économe en énergie. L’économie de l’air comprimé pourrait être l’alternative pratique et réaliste à l’utopie de l’hydrogène ou du tout électrique.
La promesse de l’air comprimé
Bien que le potentiel de l’énergie éolienne et solaire soit plus que suffisant pour répondre à la demande électrique des sociétés industrielles, ces ressources ne sont disponibles que par intermittence - est un moyen de faire face à la variabilité et l’incertitude des énergies renouvelables, mais elle a ses limites. Par conséquent, un réseau électrique renouvelable a besoin d’un minimum de stockage d’énergie, et il en va de même pour un système hors réseau basé sur l’énergie solaire ou éolienne.
Aujourd’hui, plus de 99% de la capacité de stockage électrique dans le monde se compose de centrales hydroélectriques de pompage-turbinage, où le surplus d’énergie électrique des centrales solaires ou éoliennes est stocké pour une utilisation ultérieure en pompant l’eau d’un réservoir inférieur à un réservoir supérieur. Le stockage d’énergie par pompage-turbinage est assez efficace et low-tech, mais il nécessite un environnement approprié avec deux grands plans d’eau, séparés verticalement, et un ou deux barrages. Il inonde également de vastes étendues de terre. Par ailleurs, la plupart des sites adaptés sont déjà utilisés, ce qui signifie qu’il y a peu de potentiel pour une croissance future. 12
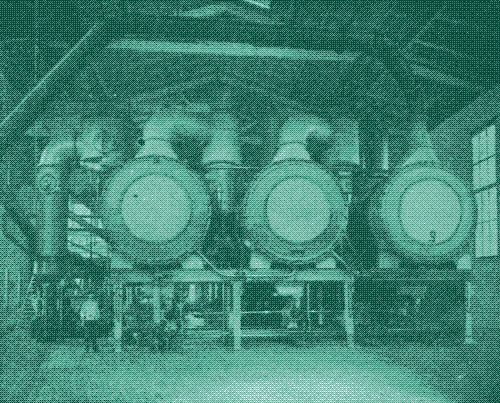
C’est pour cela que de nombreuses personnes voient une alternative prometteuse dans le stockage d’énergie par air comprimé (CAES), une autre forme de stockage d’énergie mécanique. Dans ces systèmes, de l’électricité est utilisée pour comprimer de l’air, qui est stocké dans un réservoir souterrain. Pour utiliser l’énergie stockée, l’air est décompressé et reconverti en électricité.
Bien que les systèmes CAES nécessitent également une géographie adaptée pour fournir les réservoirs souterrains de stockage d’air, on pense qu’il y a beaucoup plus de sites appropriés dans le monde que pour le stockage d’énergie hydraulique. 3
Si l’énergie stockée pendant toute la durée de vie d’un appareil de stockage est comparée à la quantité d’énergie primaire requise pour construire l’appareil, le système CAES est largement supérieur aux batteries électrochimiques.
Une chose notable est que le système CAES est le stockage d’énergie le plus durable qui soit. Contrairement au stockage d’énergie par pompage-turbinage, le stockage d’énergie par air comprimé ne présente aucun problème environnemental causé par l’inondation des terres et le barrage des rivières.
De plus, si l’énergie stockée pendant toute la durée de vie d’un appareil de stockage est comparée à la quantité d’énergie primaire requise pour construire l’appareil, le système CAES surpasse le stockage d’énergie par pompage-turbinage et est largement supérieur aux batteries électrochimiques, qui nécessitent 10 à 100 fois plus d’énergie grise pour une capacité de stockage donnée. 3
Il s’agit d’un avantage crucial car un besoin énergétique élevé pour la production du stockage d’énergie peut diminuer considérablement la durabilité d’un réseau électrique renouvelable
Le problème avec l’air comprimé
Malgré tous ces avantages, il n’y a actuellement que deux usines CAES à grande échelle dans le monde : une en Allemagne, construite en 1979 et une aux États-Unis, construite en 1991. 4 Cet engouement limité est principalement attribué au fait que plus de la moitié de l’énergie est perdue lors du chargement et du déchargement d’une «batterie» d’air comprimé.
Alors que le stockage par pompage-turbinage a une efficacité de charge/décharge de 70 à 85% et que les batteries chimiques atteignent 65 à 90%, les usines CAES en fonctionnement en Allemagne et aux États-Unis ont une efficacité électrique-électrique de seulement 40 à 42% et 51-54%, respectivement. 256
Ce faible rendement de conversion énergétique est notamment dû au fait que l’air chauffe lorsqu’il est comprimé à des pressions élevées (les deux usines CAES fonctionnent à 50-70 bar, ce qui représente 10 à 20 fois la pression d’air dans un pneu de vélo). Et puisque la densité énergétique de l’air diminue avec l’augmentation de la température, les deux usines CAES retirent la chaleur avant le stockage et la rejettent dans l’atmosphère. Cela représente une source importante de perte d’énergie. 78
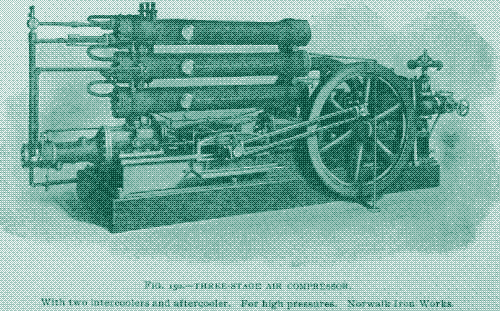
En outre, lorsque l’air est détendu depuis une haute pression, la température diminue à un point tel que la vapeur d’eau dans l’air peut geler, endommageant ainsi les vannes et le détendeur du système de stockage. Pour éviter cela, et augmenter la puissance de sortie, les deux usines CAES chauffent l’air dans des brûleurs à l’aide de gaz naturel avant la détente. De toute évidence, cela diminue encore l’efficacité énergétique de l’ensemble du processus et rendent les systèmes CAES actuels entièrement dépendants des combustibles fossiles pour leur fonctionnement. 179
Une efficacité de conversion de 40 à 50% signifie que la capacité de production d’énergie éolienne ou solaire doit être doublée pour compenser cette perte. Par conséquent, nous avons besoin de plus d’énergie, de plus de matériaux et de plus d’espace pour la même production d’énergie. De ce fait le caractère durable du système CAES s’en trouve fortement diminué à cause de sa faible efficacité.
De plus, le faible rendement de conversion énergétique des systèmes CAES est intrinsèquement lié à la faible densité énergétique de l’air, ce qui signifie qu’ils dépendent de très grands réservoirs de stockage. En principe, la densité énergétique de l’air comprimé peut être considérablement améliorée en utilisant des pressions d’air plus élevées, mais à mesure que la pression d’air augmente, plus d’énergie est perdue en chaleur et le rendement de l’ensemble du processus se détériore davantage. Par conséquent, un système CAES – dans sa configuration actuelle – est toujours un compromis entre rendement et densité énergétique.
4 000 ans d’histoire
La très faible efficacité énergétique des systèmes de stockage d’énergie par air comprimé d’aujourd’hui est remarquable dans un contexte historique. L’utilisation de l’air comprimé remonte à plus de 4 000 ans et a toujours été un moteur important du progrès technologique. Bien que ces applications historiques ne visaient pas le stockage d’énergie, elles offrent une inspiration pour améliorer à la fois l’efficacité énergétique et la densité énergétique des systèmes CAES d’aujourd’hui.
L’utilisation de l’air comprimé la plus ancienne et sans doute la plus importante de l’histoire a été d’alimenter le feu. On l’a retrouvé dans la cuisine et dans tous les processus de production à base de chaleur, mais c’était particulièrement important dans les procédés de fabrication des métaux. Un feu de charbon de bois non assisté pouvait atteindre 900 °C, mais en activant cette combustion avec de l’air comprimé cela pouvait élever sa température à près de 2000 °C. 10
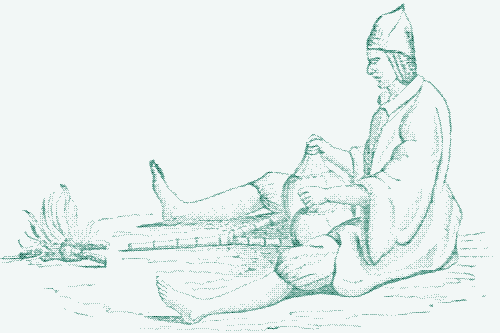
Bien qu’il y ait des différences régionales importantes, l’histoire de la fusion des métaux montre une évolution des métaux depuis des points de fusion relativement bas, tels que l’étain (230 °C), vers les métaux avec des points de fusion plus élevés, d’abord le cuivre (1050 °C) puis le fer ( 1500 °C).
Ces progrès ont été en partie dus aux améliorations de la technologie des compresseurs d’air : cela a évolué depuis des formes de foulage d’air à l’aide de sacs, puis des cylindres et pistons en bois et de diverses formes de soufflets, tous fonctionnant à l’huile de coude, vers des soufflets d’accordéon beaucoup plus grands et plus puissants, en bois et en peaux de taureaux, à double effet et actionnés par l’énergie hydraulique. 11
Les progrès dans la fusion des métaux sont en partie dus aux améliorations de la technologie des compresseurs d’air
À partir des années 1860 et dans les années 1900, l’air comprimé (ou «pneumatique») a été au centre d’une autre révolution technologique. Cette fois, la pneumatique s’est imposée comme la technologie de transmission de puissance la plus polyvalente et la plus utilisée avant l’introduction de l’électricité. 12
En raison du fait que l’électricité était encore distribuée à basse tension («hydraulique») représentaient une manière plus efficace de transmettre de l’énergie sur de plus longues distances. En outre, l’air comprimé avait un avantage très pratique sur l’eau sous pression : l’air est disponible partout et son échappement ne pose aucun problème, tandis que les systèmes hydrauliques nécessitent une alimentation en eau suffisante ainsi qu’un moyen de vidanger le fluide après utilisation.
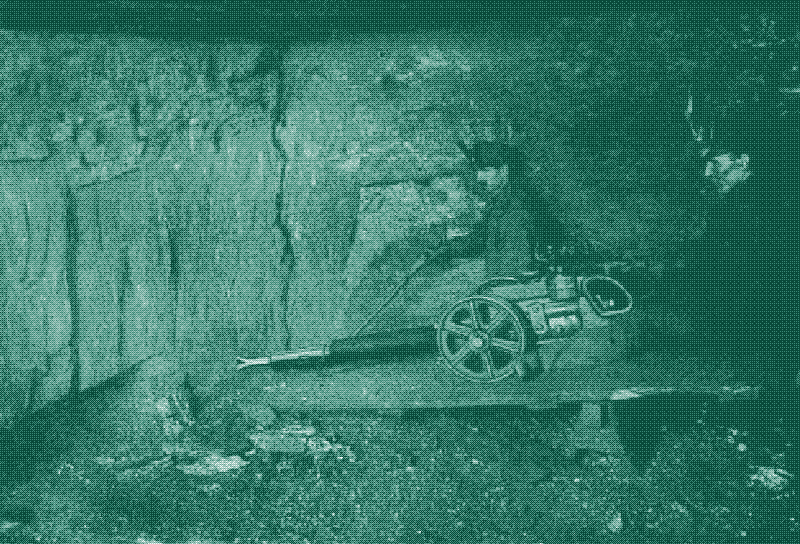
Utilisé en tant que technologie de transmission d’énergie, l’air comprimé a d’abord été appliqué à l’industrie minière et dans les tunnels. Cela répondait au besoin pressant d’avoir des foreuses mécaniques pour la construction de canaux et de voies ferrées, car la construction de tunnels constituait un goulot d’étranglement majeur. Dans des conditions difficiles de roche dure, l’avancement du tunnel avec un forage manuel - à l’aide d’une pioche et d’explosifs - se mesurait en pouces par jour, et des tunnels d’une longueur d’à peine un kilomètre pouvaient prendre des années. 12
Avec cette nouvelle technique, les moteurs à vapeur en surface produisaient de l’air comprimé qui était acheminé dans les puits ou les tunnels. L’avancée majeure de la transmission d’énergie à air comprimé et des outils de forage pneumatiques s’est ainsi produite avec le creusement du tunnel du Mont Cenis de 13,7 km de long dans les Alpes, qui a été achevé en seulement 14 ans (1857-1871). La technologie s’est rapidement répandue dans l’industrie minière, et en particulier aux États-Unis, où l’air comprimé alimentait non seulement les foreuses, mais également d’autres machines, telles que des bocards à mine, des machines de transport et de pompage. 1213
Le réseau à air comprimé de Paris
Avec son efficacité démontrée de manière si spectaculaire dans le forage, l’air comprimé a été adapté à un éventail croissant d’opérations industrielles : martelage, rivetage, peinture et pulvérisation, manipulation sous pression de fluides et une multitude d’autres utilisations. Aux États-Unis, la pneumatique s’est largement répandue comme énergie auxiliaire dans la fabrication à partir des années 1880. Le recensement de 1900 a fait référence à l’introduction généralisée de petits outils pneumatiques comme probablement «le développement d’outils le plus important de la décennie». 12
Environ à la même époque en Europe, les Français sont allés plus loin dans le développement de l’énergie pneumatique en créant un réseau de distribution à l’échelle de la ville de Paris. Il resta en service pendant plus de 100 ans (de 1881 à 1994), distribuant de l’air comprimé à une pression relativement basse de 5-6 bar sur un réseau de plus de 900 km de réseau (au final), desservant plus de 10 000 consommateurs. 1213
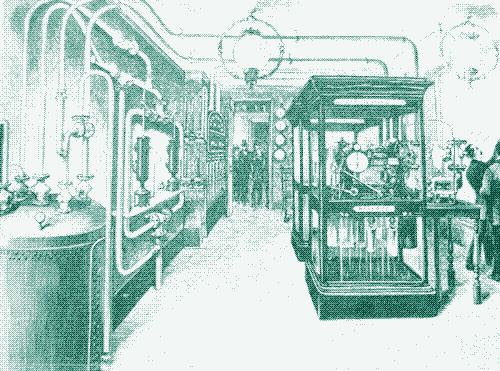
Le réseau d’air comprimé de Paris a commencé comme un système conçu exclusivement pour régler les horloges par des impulsions d’air comprimé envoyées via des tuyaux souterrains. En 1889, le réseau parisien régulait 8 000 horloges sur 65 km de réseau. Le service de régulation d’horloge a été retiré en 1927, lorsqu’il est devenu clair que l’électricité était mieux adaptée pour ce travail. Cependant, à cette époque, le réseau d’air comprimé à Paris avait connu un grand succès dans les petits établissements industriels et de services. 12141516171813
Les Français ont mis en place un réseau de distribution d’énergie à l’échelle de la ville de Paris, qui a servi plus de 10 000 clients et est resté en service pendant 100 ans
Déjà en 1892, F.E. Idell écrivait que «parmi les plus petits usages industriels pour lesquels les moteurs pneumatiques sont utilisés à Paris, je trouve la conduite de tours pour le métal et le bois, de scies circulaires, de perceuses, de polisseuses et bien d’autres. Ils sont également utilisés dans les ateliers de charpentiers, menuisiers et ébénistes, de forgerons, de fabricants de parapluies, de fabricants de cols, de relieurs, et naturellement dans de nombreux endroits où les machines à coudre sont utilisées, aussi bien par les couturiers, les tailleurs, et cordonniers, de la plus petite à la plus grande échelle. » 13
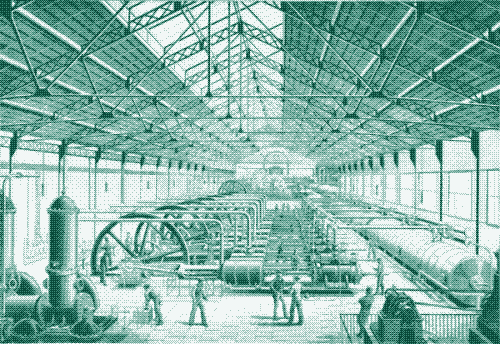
Au fil des ans, l’utilisation commerciale et domestique de l’air comprimé a diminué, au profit de l’électricité qui est devenue bien plus importante. Cependant, la consommation industrielle d’air comprimé a continué de croître et de nombreuses grandes usines parisiennes – des constructeurs automobiles aux fabricants de verre – ont été connectées à ce réseau de distribution unique jusqu’à sa toute fin. Les dentistes sont devenus de nouveaux utilisateurs dans les années 1970 et 1980. 1213
Première leçon : éviter les conversions d’énergie
Que peut-on apprendre en comparant les technologies historiques et actuelles basées sur l’air comprimé ? Une première différence cruciale est le nombre de conversions d’énergie impliquées. Dans les systèmes historiques, l’énergie mécanique (par exemple via une roue à aubes ou une machine à vapeur) était directement convertie en air comprimé (à l’aide d’un compresseur à air), puis – le plus souvent – reconvertie en énergie mécanique (par exemple pour déplacer un marteau pneumatique). Par conséquent, il n’y avait que deux sources de pertes de conversion d’énergie: dans le compresseur et dans le détendeur.
L’air comprimé est toujours vital pour la productivité de nombreuses industries et services à travers le monde et est utilisé dans des milliers d’applications – de l’emballage alimentaire ou la fusion des métaux à la fabrication de micropuces et de plastiques. Cependant, l’air comprimé est maintenant produit par des compresseurs d’air fonctionnant à l’électricité. Cela introduit deux sources supplémentaires de perte d’énergie : le générateur électrique (qui convertit l’énergie mécanique d’une source d’énergie en électricité) et le moteur électrique (qui reconvertit l’énergie électrique en énergie mécanique pour faire fonctionner le compresseur d’air).
En conséquence, aujourd’hui l’utilisation industrielle d’air comprimé est très inefficace : en supposant que chaque convertisseur est efficace à 75% et sans aucune autre perte d’énergie, seulement 30% de l’énergie consommée est convertie en sortie utile. 19
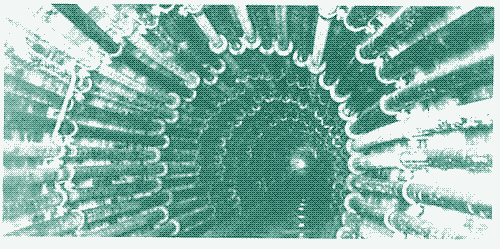
L’efficacité globale des deux centrales CAES existantes est encore pire que cela : non seulement il y a l’étape de conversion supplémentaire au début de la chaîne (la perte d’énergie dans la génératrice de l’éolienne et dans le moteur électrique qui fait fonctionner le compresseur), mais aussi en fin de chaîne. Elles se démarquent des applications industrielles, où le produit final est de l’air comprimé car une usine CAES, elle, reconvertit encore l’air comprimé en électricité.
Lorsqu’on dit que le rendement d’une centrale CAES est de 40 à 50%, cela ne fait référence qu’aux pertes dans le compresseur d’air et le détendeur d’air (rendement électrique-électrique). Cependant, si nous incluons les conversions vers et depuis l’énergie électrique, le rendement global du système diminue à moins de 20%, en supposant à nouveau que chaque convertisseur a un rendement de 75%.
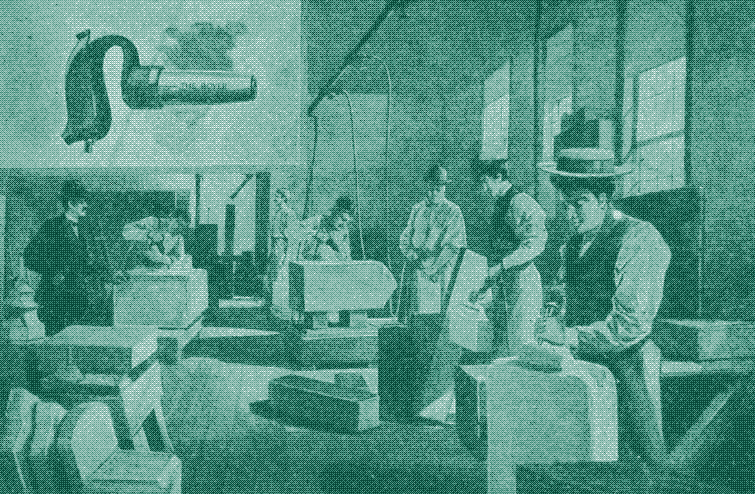
Imaginez maintenant qu’une usine utilise l’électricité d’une centrale CAES pour alimenter ses compresseurs d’air industriels - un scénario parfaitement possible. Nous obtenons alors la chaîne de conversion d’énergie suivante : l’énergie mécanique est convertie en électricité, l’électricité est convertie en air comprimé, l’air comprimé est converti en électricité, l’électricité est convertie en air comprimé et l’air comprimé est converti en énergie mécanique. Ce n’est pas deux ou quatre, mais six sources de pertes de conversion d’énergie. En supposant que chaque convertisseur est efficace à 75%, l’efficacité globale du système tombe désormais en dessous de 10%.
Si nous connections une centrale CAES directement à une usine qui utilise des outils pneumatiques, en connectant l’air comprimé de l’une à l’autre, il ne serait pas nécessaire de convertir l’air comprimé en électricité et vice versa.
En revanche, si nous connections une centrale CAES directement à une usine qui utilise des outils pneumatiques, en connectant l’air comprimé de l’une à l’autre, nous ne subirions que quatre sources de perte d’énergie (générateur, moteur, compresseur, détendeur). Dans la centrale CAES, il n’est plus nécessaire de reconvertir l’air comprimé stocké en électricité, tandis qu’en usine, il n’est pas nécessaire de comprimer l’air une deuxième fois, en utilisant de l’électricité. Il suffit de respecter une distance entre la centrale CAES et l’usine jusqu’à 25 km – la distance jusqu’à laquelle l’air comprimé peut être distribué efficacement.
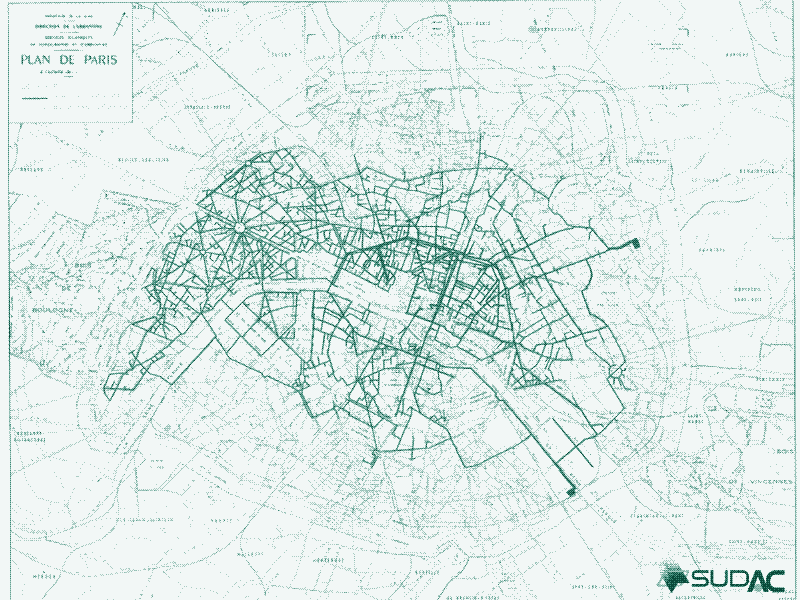
La prochaine étape évidente consiste à comprimer l’air dans une centrale CAES en utilisant une liaison mécanique directe entre l’éolienne et le compresseur d’air, évitant ainsi la conversion de l’énergie mécanique directe en électricité et vice versa. Une telle approche – qui a été démontrée à petite échelle, dans des configurations légèrement différentes 82021 – rendrait les systèmes CAES entièrement indépendants de l’électricité et ramènerait les étapes de conversion d’énergie à deux, comme dans tous les systèmes historiques. Les seules pertes de conversion d’énergie restantes seraient dans le compresseur d’air et dans le détendeur d’air.
Une connexion directe entre l’arbre de l’éolienne et le compresseur d’air améliorerait également l’efficacité d’une centrale CAES qui n’est pas connectée à une usine mais qui fournit de l’électricité à des fins générales, bien que le gain d’efficacité soit plus faible. De toute évidence, la compression mécanique de l’air ne fonctionne qu’avec des éoliennes et non avec des panneaux solaires photovoltaïques, qui ne produisent pas d’énergie mécanique.
Deuxième leçon : Utiliser la chaleur et le froid pour d’autres finalités
Une deuxième différence notable entre les utilisations actuelles et historiques de l’air comprimé est de savoir comment gérer les différences de température causées par la compression et la détente de l’air. Pour améliorer leur efficacité, les deux centrales CAES en service utilisent plusieurs compresseurs d’air. La compression à plusieurs étages augmente progressivement la pression et refroidit l’air après chaque étape de compression, en utilisant un circuit d’eau de refroidissement qui est ensuite acheminé vers une tour de refroidissement pour rejetter l’excédent de chaleur dans l’atmosphère. 2223
Aujourd’hui, la plupart des ingénieurs CAES se concentrent sur l’amélioration de cette efficacité en utilisant la chaleur résiduelle de compression pour réchauffer l’air comprimé lors de la détente. Cette méthode est appelée «Advanced Adiabatic CAES» (AA-CAES) ou «fuelless CAES» et élimine le besoin de réchauffer l’air au gaz naturel comme dans le système CAES «diabatique» standard. Cette technologie devrait atteindre une efficacité globale d’environ 70%, ce qui la rapprocherait de l’efficacité des batteries chimiques et des installations de stockage par pompage-turbinage. 7
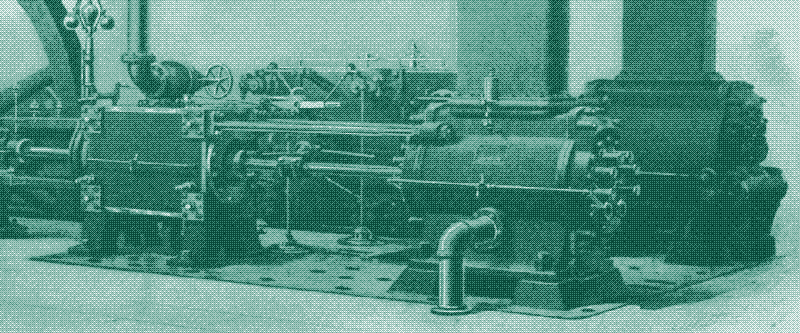
Cependant, la technologie AA-CAES reste non éprouvée jusqu’à présent : un certain nombre d’installations ont été proposées, mais aucune n’a encore dépassé le stade de la conception. 2223 Le problème est double : premièrement, cette amélioration du procédé augmente les coûts d’une centrale CAES de 20 à 40% ; deuxièmement, la réutilisation de la chaleur résiduelle du processus de compression est un défi technologique. Pour transférer de la chaleur à un débit élevé avec une différence de température minimale, il faut une très grande surface de contact. 7
Dans le réseau à air comprimé de Paris, le refroidissement fourni par la détente de l’air a été utilisé pour la réfrigération, la congélation, le refroidissement et la ventilation
Si nous regardons les anciens systèmes pneumatiques, nous voyons qu’il existe d’autres moyens plus faciles de tirer parti des différences de température dues à la compression et à la détente. Dans le réseau électrique à air comprimé de Paris, les ingénieurs ont profité du refroidissement apporté par la détente de l’air. À Paris, l’air comprimé était généralement chauffé par un feu de charbon avant d’être utilisé par un moteur pneumatique, augmentant la puissance de sortie d’une manière très similaire à l’utilisation du gaz naturel dans les systèmes CAES actuels.
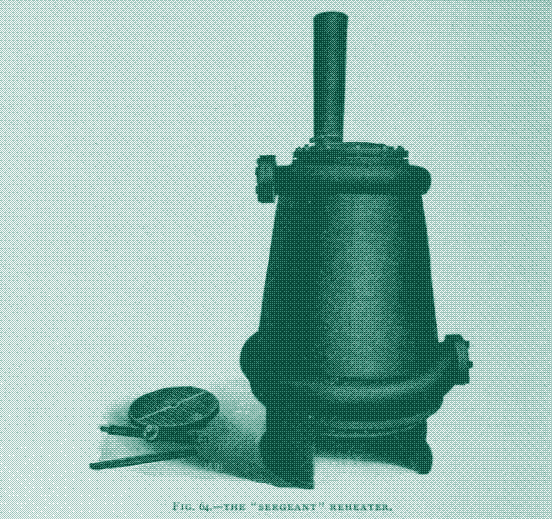
Cependant, dans les bars et restaurants, ces réchauffeurs n’étaient pas utilisés. Au lieu de cela, l’air froid a été utilisé à des fins de réfrigération, de congélation, de refroidissement ou de ventilation. En 1892, F.E. Idell a décrit un restaurant parisien où «l’évacuation a été transporté à travers un conduit de brique dans la cave à bière. Dans ce conduit, les carafes pouvaient geler et de gros blocs de glace étaient également fabriqués pour être utilisés à table, tandis que l’air était encore assez froid en passant à travers la cave à bière pour rendre l’utilisation de la glace pour le refroidissement tout à fait inutile, même par le temps le plus chaud.» 13
L’utilisation d’air comprimé pour le refroidissement ou la congélation allait parfois de pair avec la production d’électricité pour l’éclairage, en entraînant une dynamo. Dans ces cas, les moteurs pneumatiques étaient essentiellement utilisés pour leur échappement, la lumière électrique étant le sous-produit. L’exploitation des différences de température s’est avérée utile également dans le secteur minier évoqué précédemment, où l’échappement des foreuses aidaient à refroidir (et à ventiler) les mines.
Une idée similaire et prometteuse aujourd’hui est le stockage d’énergie par l’air comprimé combiné au stockage thermique pour fournir simultanément électricité, chauffage, refroidissement, réfrigération et/ou ventilation. En fait, cette approche permet d’éviter également plusieurs conversions d’énergie, car elle pourrait remplacer les réfrigérateurs, les congélateurs, les climatiseurs et les systèmes de chauffage fonctionnant aujourd’hui à l’électricité. Cette méthode pourrait fonctionner au niveau d’un quartier d’une ville ou d’une zone industrielle 23, mais elle serait particulièrement intéressante pour le stockage décentralisé de l’énergie, en utilisant des réservoirs de stockage artificiels et hors sol.
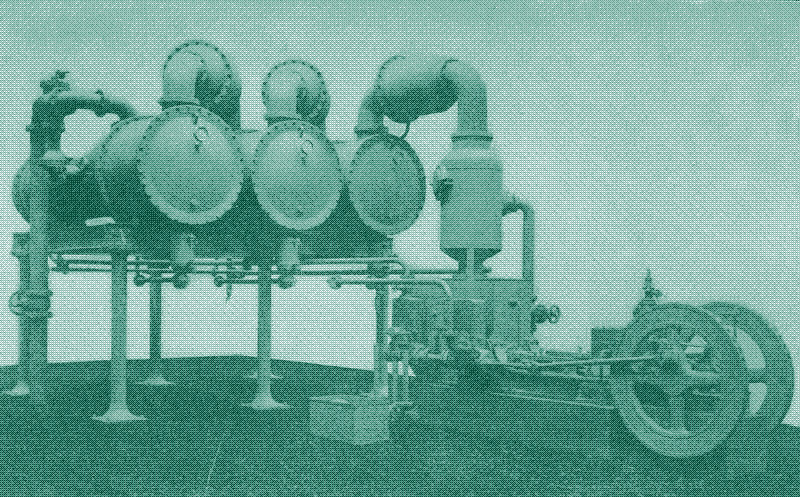
Comme nous l’avons vu, l’augmentation de la pression d’air peut réduire considérablement la taille du réservoir de stockage d’air comprimé, mais uniquement au détriment de l’augmentation des pertes de chaleur. Dans des habitations, l’espace pour les réservoirs de stockage est limité, mais il existe une forte demande de chaleur et de froid ainsi que d’électricité. L’augmentation de la pression de l’air rend le réservoir de stockage plus petit et augmente la production de chaleur et de froid, répondant à tous les besoins énergétiques d’un ménage.
Certaines propositions de conception suivent d’autres approches pour faire face à la génération de chaleur lors de la compression, et celles-ci pourraient fonctionner à la fois pour les systèmes CAES à grande et à petite échelle. Une idée intéressante est un système de stockage d’énergie par air comprimé fonctionnant à l’énergie éolienne et solaire. 24 L’énergie éolienne serait stockée sous forme d’air comprimé via une connexion directe au compresseur, comme dans les autres centrales CAES. Cependant, l’énergie solaire provenant d’une parabole serait, elle, stockée dans un réservoir solaire thermique isolé et utilisée pour réchauffer l’air comprimé avant la détente. Puisque la chaleur du processus de compression n’est plus nécessaire pour réchauffer l’air lors de la détente, elle peut être utilisée pour produire de l’eau chaude.
Un concept similaire de conception hybride de stockage d’énergie thermique et d’air comprimé utilise le chauffage électrique au lieu de l’énergie solaire thermique. 25 Étant donné que la charge de ces systèmes passe d’une conversion pure à un investissement partiel dans le stockage thermique, des densités énergétiques bien supérieures à celles d’un système CAES traditionnel peuvent être atteintes et la taille du stockage d’air peut être réduite.
Troisième leçon : Améliorer le compresseur d’air
Une troisième façon d’améliorer le rendement du stockage d’énergie par air comprimé consiste à utiliser des compresseurs et des détendeurs d’air plus économes en énergie. Cette stratégie est opposée à celle que nous venons d’expliquer précédemment. Au lieu de profiter de la chaleur et du froid pour rendre le système plus efficace, il essaie de minimiser la production de chaleur pendant la compression (et, par conséquent, de limiter le refroidissement pendant la détente).
Encore une fois, cela vaut la peine de se tourner vers le passé pour trouver l’inspiration. Étonnamment, le Saint-Graal de la compression d’air «isotherme» – dans laquelle aucune chaleur résiduelle n’est produite – a été découvert il y a au moins 400 ans. Le compresseur d’air hydraulique – ou «trompe», comme on l’appelait à l’origine – était une invention italienne mentionnée pour la première fois en 1588, mais peut-être déjà connue dans l’Antiquité.
À partir des années 1600, des dizaines de «trompes» ont fourni un jet d’air continu aux premiers fours de fusion du fer et du laiton dans les Pyrénées françaises/espagnoles. 2627 Comparé à une roue à aubes faisant fonctionner un compresseur à piston en bois, ce système était à peu près trois fois plus efficace, permettant une production de fer plus élevée avec moins de ressources hydrauliques.
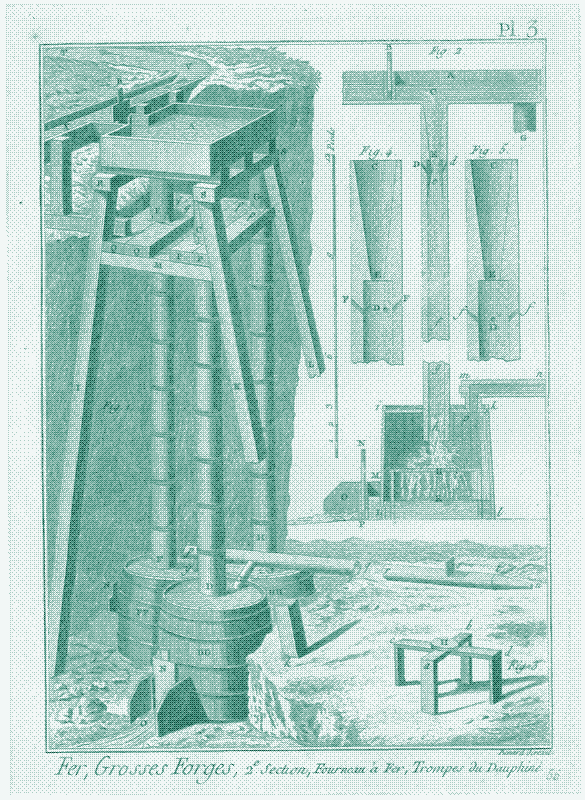
Le trompe consistait en un ou plusieurs tubes verticaux en bois à travers lesquels l’eau se déversait par gravité. Lors de sa descente, l’eau absorbait de l’air à travers des trous le long du tube et agissait comme un piston continu en comprimant l’air. Au fond du tube, l’air était séparé de l’eau dans un récipient, après quoi il était envoyé à la buse du four par pression réglable. Fait remarquable, le compresseur d’air hydraulique produit de l’air comprimé sans aucune pièce mobile, autre que des vannes d’arrêt pour couper le débit d’eau entrant. Cela en fait un appareil extrêmement fiable. 2628
Le compresseur d’air hydraulique produit de l’air comprimé sans aucune pièce mobile, ce qui en fait un appareil extrêmement fiable et efficace
Au XIXème siècle, la conception du compresseur d’air hydraulique a encore été améliorée, le rendant plus efficace et fonctionnel. En 1861, un compresseur d’air hydraulique a été construit pour alimenter les foreuses de la construction du tunnel du Mont Cenis dans les Alpes, mais la technologie n’a atteint son apogée qu’à la fin du XIXème siècle, cette fois dans l’industrie minière.
A partir de 1896, et pendant 33 ans, dix-huit gigantesques compresseurs d’air hydrauliques ont été construits, principalement aux États-Unis, au Canada, en Allemagne et en Suède. Dans les plus grandes de ces installations, qui ont été partiellement ou entièrement construites sous terre, l’eau et l’air chutaient à travers des tubes et des arbres – creusés dans la roche – qui pouvaient faire plus de 100 mètres de profondeur et jusqu’à 4 mètres de largeur. La pression de refoulement s’élevait à 8 bars et la puissance de sortie pouvait atteindre 3 000 kilowatts. 2930
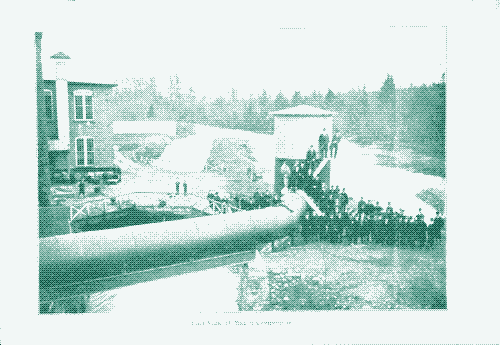
Les premières installations utilisaient une multitude de petits tuyaux d’air descendants, comme dans le trompe d’origine, tandis que les installations ultérieures n’utilisaient que deux arbres. Des conduites forcées apportaient de l’eau à différents modèles de mélangeurs air-eau et l’air comprimé était souvent subdivisé pour aller vers différentes mines et acheminé sur des distances de plusieurs kilomètres. La plupart des compresseurs d’air hydrauliques ont fonctionné pendant des décennies, le dernier jusqu’en 1981. 2930
Des tests de performance effectués de temps à autre entre les années 1890 et les années 1950 indiquent que l’efficacité de conversion de l’énergie hydroélectrique en pneumatique variait entre 53% et 88%. Des recherches plus récentes ont abaissé ces chiffres pour tenir compte des effets de la solubilité du gaz, rapportant des rendements de 40 à 78%. 2928 Bien que la compression hydraulique de l’air produise peu de chaleur perdue, un nouveau type de perte d’énergie est introduit : une partie de l’air se dissout dans l’eau et contourne ainsi le processus de séparation air-eau, réduisant le débit massique d’air à la sortie. 29
Récemment le compresseur d’air hydraulique a connu un regain d’intérêt. Une équipe de recherche canadienne a mis au point une plate-forme de démonstration de compresseur d’air hydraulique de 30 m de haut dans un ancien puits de mine. 2931 Le «Projet de démonstration HAC» mesure et vérifie le potentiel d’économies d’énergie de la technologie principalement pour les applications minières d’extraction en profondeur. Cependant, cela pourrait également être une alternative pour les compresseurs à plusieurs étages utilisés dans l’industrie et dans les centrales CAES. Notamment car cette nouvelle configuration peut être mise en place avec une boucle fermée, en utilisant une pompe au lieu d’une colonne d’eau naturelle.
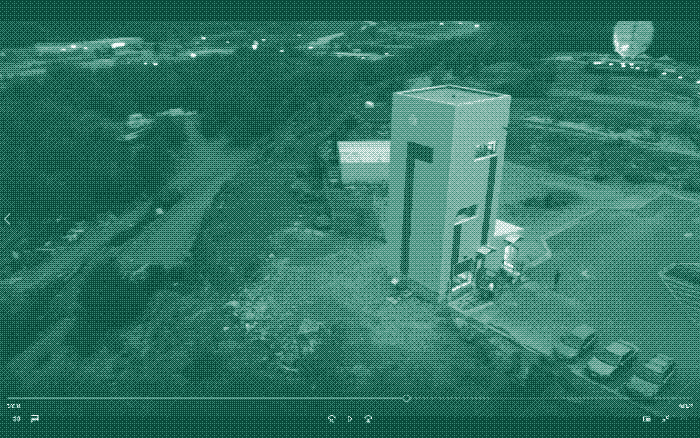
Bien que la pompe entraîne une consommation d’énergie supplémentaire, une configuration en boucle fermée présente deux avantages importants. Premièrement, cela pourrait s’appliquer n’importe où et pas seulement à proximité d’une source d’eau exploitable présentant une grande différence de hauteur. Deuxièmement, cela permet de supprimer les effets indésirables des propriétés physiques de solubilité, par exemple en ajoutant du sel au circuit d’eau.
Selon les chercheurs, un compresseur d’air hydraulique en boucle fermée pourrait avoir un rendement de 75%, en prenant en compte la consommation d’énergie supplémentaire de la pompe. C’est 13% plus efficace qu’un compresseur centrifuge à trois étages, et les avantages en termes de coûts seront meilleurs en raison des exigences de maintenance moindres. 2931
Le compresseur d’air hydraulique semble être une combinaison parfaite pour les systèmes CAES à grande échelle avec des réservoirs souterrains. En fait, de nombreux compresseurs d’air hydrauliques des XIXème et XXème siècles utilisaient également le réservoir inférieur de séparation d’air pour le stockage d’énergie de l’air comprimé, ce qui pourrait être considéré comme la première utilisation à grande échelle de CAES. Le stockage – qui pouvait atteindre 5 600 m3 – été utilisé pour répondre à une demande d’air excédentaire de courte durée, ce qui signifie que le compresseur d’air hydraulique n’avait pas besoin d’être conçu pour les charges maximales. 28
L’avenir de l’air comprimé
Aucune de ces idées ne rendra les centrales CAES 100% efficaces. Cependant, elles pourraient les aider à atteindre des rendements similaires à ceux des batteries, mais avec des impacts environnementaux beaucoup plus faibles et un apport énergétique nécessaire bien moindre. Dans le prochain article, nous nous concentrons plus en détail sur les systèmes CAES à petite échelle, qui promettent d’être une alternative durable aux batteries chimiques dans les installations hors réseau
Merci à George Fleming.