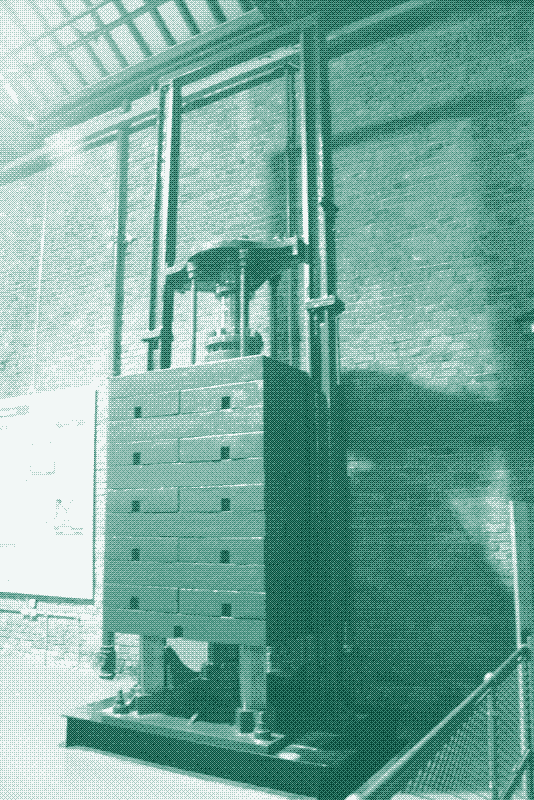
L’utilisation des moteurs à eau était largement répandue en Europe et en Amérique dans la seconde moitié du dix-neuvième siècle. Reliées à un robinet, ces petites turbines hydrauliques pouvaient faire fonctionner n’importe quelle machine aujourd’hui alimentée à l’électricité. Comme nous l’avons montré dans un précédent article, faire fonctionner ces moteurs à l’eau courante n’était pas une solution particulièrement durable. Du fait des niveaux de pression à la fois faibles et irréguliers dans les réseaux d’adduction, ces moteurs consommaient d’énormes quantités d’eau potable.
Tandis qu’aux Etats-Unis les moteurs à eau tombèrent en désuétude au début du vingtième siècle, les Européens trouvèrent une solution pour réduire leur importante consommation d’eau, perfectionnant ainsi la technique de transmission d’énergie par voie hydraulique. Ils déployèrent des « réseaux de force motrice hydraulique », dédiés à la distribution d’eau sous pression pour des usages de force mécanique exclusivement, et les convertirent à des régimes de pression beaucoup plus élevés et constants, rendus possibles par l’invention de l’accumulateur hydraulique.
La quasi-totalité de ces réseaux demeurèrent en service jusque dans les années 1960 et 1970. Comparée à l’électricité, la transmission de l’énergie hydraulique comme force motrice s’avère très efficace, quand elle est utilisée pour alimenter des machines puissantes mais fonctionnant de manière intermittente, lesquelles peuvent être réparties sur une aire géographique de la taille d’une ville entière.
“L’usage de l’eau est un sujet étonnamment peu considéré dans les publications d’ingénierie. Cantonnée à une image romantique ou populaire, la force motrice hydraulique n’a jamais conquis l’intérêt du grand public, contrairement à la machine à vapeur, la locomotive ou même le moteur à combustion interne.” Ian McNeil, Hydraulic Power, 1972
Les bases théoriques de la transmission de l’énergie hydraulique furent établies en 1647 par le jeune prodige français Blaise Pascal. Il découvrit, par le biais d’expériences scientifiques, que l’eau – contrairement à l’air – est un fluide quasi incompressible et transmet la pression de manière uniforme dans toutes les directions.
Les conséquences pratiques de ce qui deviendra plus tard le Principe de Pascal, aussi appelé “paradoxe hydrostatique”, furent démontrées par sa “machine à multiplier les forces”, schématiquement illustrée ci-dessous. Elle consiste en 2 cylindres, reliés entre eux par un tuyau. L’ensemble du dispositif est rempli d’eau et scellé hermétiquement. Le premier cylindre contient un piston de faible diamètre, tandis que le second cylindre contient un piston de diamètre 100 fois supérieur.
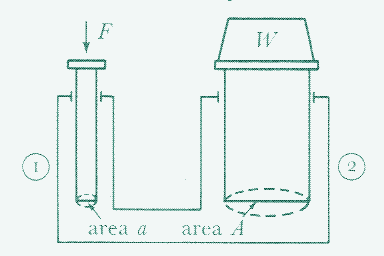
Pascal parvint à démontrer qu’en plaçant un poids sur le petit piston, la force exercée permettrait de soulever un poids 100 fois plus lourd disposé sur le grand piston. En d’autres termes, selon le principe de Pascal, une force peut être appliquée à une petite aire pour exercer une force plus importante sur une plus grande surface : une machine exploitant ce principe pour multiplier une force de la sorte est appelée presse hydraulique. Le rapport entre les forces exercées respectivement sur le petit et le grand piston s’appelle l’avantage mécanique du levier hydraulique – dans l’exemple précédent, il est de 100 pour 1. Autrement dit, il est possible de générer une force résultante de 100 kg en appliquant une force initiale de seulement 1 kg.
Une Machine à Multiplier les Forces
La multiplication des forces était tout sauf une nouveauté au début du dix-septième siècle. Des systèmes plus simples, tels que les poulies, engrenages, cabestans, treuils et grues à tympan (aussi appelées « roues de carrier ») – autant de variantes du bras de levier, vieux de 7000 ans – étaient capable de générer une importante force résultante à partir d’un effort initial moindre. Les Romains, par exemple, construisaient des grues dont l’avantage mécanique pouvait atteindre 70 pour 1, ce qui signifie qu’un seul homme exerçant une force d’environ 25 kg pouvait soulever 1,75 tonnes.
Toutefois, la version hydraulique du mécanisme de levier présente un avantage considérable par rapport aux mécanismes qui l’ont précédée : les pertes d’énergie par friction sont minimes, et indépendantes de l’avantage mécanique. Par conséquent, le rapport de multiplication potentiel est presque infiniment plus grand, et les 2 pistons peuvent être éloignés d’une distance considérable – jusqu’à 25 km environ, comme nous le verrons plus loin.
En hydraulique, les pertes d’énergie par friction sont indépendantes de l’avantage mécanique, le rapport de multiplication des forces est donc potentiellement quasi infini
L’augmentation du rapport de multiplication peut être effectuée soit en augmentant le rapport de taille entre la surface des deux pistons, soit en exerçant une force plus importante sur le plus petit piston. Tout comme dans les dispositifs plus anciens évoqués ci-dessus, l’accroissement de l’avantage mécanique s’accompagne toujours d’une diminution de la vitesse.
Si une force hydraulique faible est convertie en une force plus grande, sa vitesse de fonctionnement sera réduite de manière inversement proportionnelle, dans la mesure où la distance parcourue est proportionnelle à la force. Par exemple, en descendant le petit piston de 10 centimètres vers le bas, on n’élèverait l’autre piston qu’au 1/100ème de cette distance.
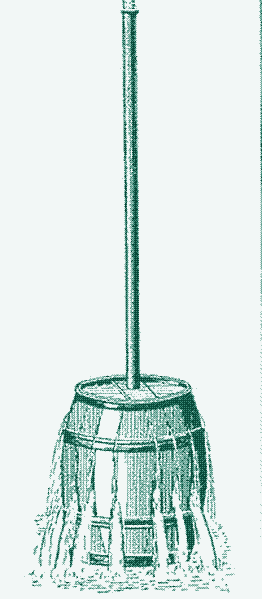
Par conséquent, au sein d’un système en circuit fermé, le poids le plus lourd ne pourrait être déplacé vers le haut que sur une distance très courte, relative à la longueur du bras du piston. Cette limite intrinsèque disparaît toutefois si l’on introduit de l’eau supplémentaire au sein du système et que le petit piston, au lieu de ne descendre qu’une seule fois, réalise plusieurs cycles de montée-descente – c’est-à-dire quand il fonctionne comme une pompe. Dans ce cas, le grand piston continuera de monter.
La Presse Hydraulique
Les matériaux disponibles à l’époque n’étant pas assez robustes pour résister à une telle pression, Pascal ne put faire qu’indirectement la démonstration de son principe. Il faudra attendre un siècle et demi pour que la multiplication hydraulique des forces soit réellement mise en pratique. La première utilisation qui en tira profit n’était pas un engin de levage, mais presque le contraire : il s’agit de la presse hydraulique, générant une force dite de compression.
La traditionnelle presse à vis, en usage à cette époque, avait connu peu d’évolutions depuis son invention par les Romains, qui l’utilisaient alors pour presser les olives et le raisin. Elle nécessitait, pour fonctionner, des efforts conséquents avec d’importantes pertes d’énergie par friction (+80 %), et ne pouvait exercer de pression supérieure à 25 tonnes. (La vis, qui convertit le mouvement de rotation en un mouvement linéaire vertical, consiste tout simplement en un plan incliné “enroulé” en spirale autour d’un cylindre).
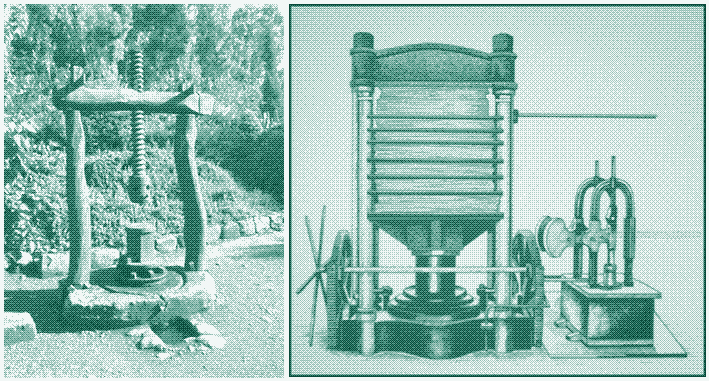
On doit l’invention de la presse hydraulique, en 1796, à un serrurier et charpentier anglais, Joseph Bramah. Son fonctionnement est entièrement basé sur les travaux théoriques de Pascal. Actionnée par une pompe manuelle, la presse hydraulique de Bramah permit d’augmenter considérablement la force pouvant être développée par un humain.
Avec les matériaux disponibles à l’époque, Bramah parvint à obtenir un ratio de 1000 pour 1, ce qui signifie qu’un poids effectif de 60 tonnes pouvait être actionné par un effort initial de 60 kg seulement sur le bras de la pompe. Le rendement de cette presse hydraulique était supérieur à 90%.
Les Ports et Chantier Navals
Bien qu’ils fussent particulièrement adaptés aux opérations de levage, les systèmes hydrauliques firent peu de progrès dans ce domaine pendant la première moitié du dix-neuvième siècle. Cela tient en grande partie aux difficultés rencontrées pour convertir le mouvement linéaire des béliers et vérins hydrauliques en mouvement rotatif des tympans de grue. Si pendant la première moitié du dix-neuvième siècle, la manutention du fret dans les ports, les chantiers navals et les gares était encore réalisée au moyen de divers engins de levage manuels, la nécessité de disposer de grues de plus en plus grandes et surtout plus puissantes se faisait sentir.
A partir des années 1930, l’acier commença à entrer dans la construction navale, de manière concomitante à l’augmentation de la taille des navires. Les systèmes traditionnels de levage n’étaient plus adaptés au regard des charges à soulever. La grue à vapeur, apparue dans les années 1850, fut la solution qui s’imposa alors dans la plupart des pays. Toutefois, une alternative intéressante fit son apparition dans les ports et chantiers navals britanniques : la grue hydraulique.
Pendant la première moitié du dix-neuvième siècle, la manutention du fret dans les ports, les chantiers navals et les gares était encore réalisée au moyen de grues et engins de levage manuels.
C’est au cours des années 1840 que l’ingénieur anglais William Armstrong commença à concevoir et utiliser des grues hydrauliques relativement puissantes. Conscient que les systèmes hydrauliques sont plus adaptés aux mouvements lents et réguliers, Armstrong mis au point une technique permettant de soulever une charge en une seule course de piston ou vérin, démultipliant suffisamment le mouvement par un jeu de poulies.
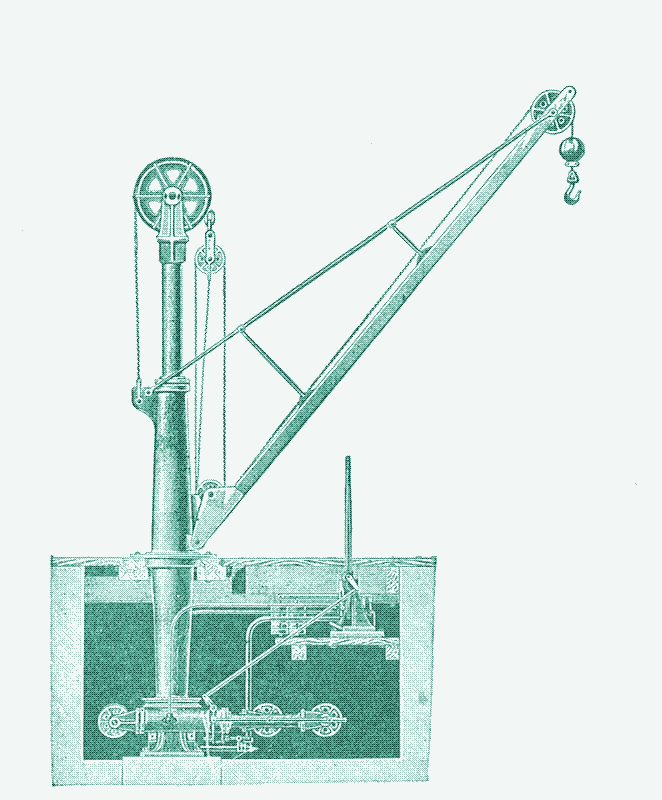
Ses efforts furent cependant mis à l’épreuve par les caractéristiques des réseaux d’adduction d’eau de l’époque, source d’énergie pour ces machines, dont la pression était à la fois faible et variable. La puissance mécanique maximale fournie par une machine hydraulique est en effet déterminée par la pression et le débit d’eau. La hauteur maximale d’un château d’eau étant limitée, il en va de même pour la pression au sein du réseau de distribution qui lui est associé. Un château d’eau d’une hauteur de 50 m (165 pieds) peut ainsi délivrer une pression de 70 psi (4,8 bars environ).
Il en découle que le seul moyen d’accroître la puissance mécanique d’une grue hydraulique alimentée par un réseau d’adduction est d’augmenter le débit d’eau. L’inconvénient est alors double : ceci entraîne d’une part une consommation accrue d’eau potable, et induit d’autre part une augmentation de la taille et du coût des conduites, valves, vérins et autres composants du réseau. En outre, en période de forte consommation d’eau potable de la part des autres usagers, le niveau d’eau du réservoir ou château d’eau diminue, de même que la pression hydraulique au sein du réseau et, in fine, la puissance délivrée en sortie par la machine.
L’Accumulateur Hydraulique
En 1851, Armstrong mit au point une solution alternative qui résolut ces différents problèmes : l’accumulateur hydraulique. Bien qu’étant beaucoup plus compact qu’un château d’eau, ce dispositif pouvait générer une pression hydraulique de 700 psi (48 bars) ou plus – dix fois supérieure à celle du réseau d’eau potable. Cela permettait de fournir une puissance supérieure d’un ordre de grandeur (c’est-à-dire de la multiplier par un facteur 10) sans augmenter la consommation d’eau potable ni surdimensionner la taille des composants.
L’accumulateur hydraulique d’Armstrong consistait en un cylindre vertical dans lequel un vérin ou un piston plongeur exerçait une pression sur l’eau. Ce piston était lesté d’un contrepoids, lequel prenait généralement la forme d’un réservoir de lestage cylindrique entourant le cylindre central (image de gauche, ci-dessous). Ce réservoir était ballasté avec des granulats (pierres concassées), de la ferraille ou tout autre matériau de lestage.
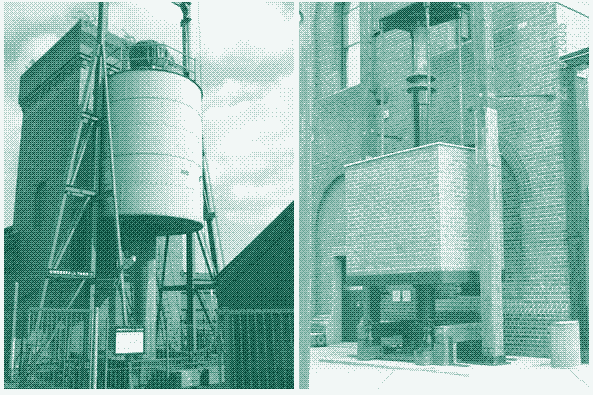
Il fallait, pour obtenir une pression de 700 psi, l’équivalent de 100 tonnes de ballast, appliquées sur un piston d’environ 45 cm de diamètre et d’une course verticale (distance maximale parcourue dans le cylindre) de 6 à 7 mètres. Un autre type d’accumulateur hydraulique fonctionnait avec un ballast briqueté (image ci-dessus, à droite) ou un empilement de brames d’acier (plaques rectangulaires), disposées sur un plateau. Les accumulateurs hydrauliques pouvaient être installés soit en extérieur, soit au sein d’un bâtiment conçu à cet effet.
Un accumulateur hydraulique pouvait fournir une puissance dix fois plus élevée que celle d’un château d’eau, et maintenir une pression uniforme dans l’ensemble du réseau.
Le fonctionnement d’un accumulateur hydraulique repose sur un mécanisme analogue à celui d’un château d’eau. En partie basse du cylindre central se trouvent une arrivée et une sortie d’eau. L’eau du port pouvait être directement introduite dans l’accumulateur par une pompe à vapeur, soulevant ainsi le piston, pour être ensuite envoyée sous pression dans les conduites via la valve de sortie, abaissant alors le piston.
L’énergie était stockée temporairement lors de l’ascension du vérin, puis récupérée lors de sa descente. Le débit de pompage de la machine à vapeur était régulé en fonction du niveau d’eau dans l’accumulateur, soit automatiquement par un système de liaisons mécaniques, soit avec l’aide d’un opérateur.
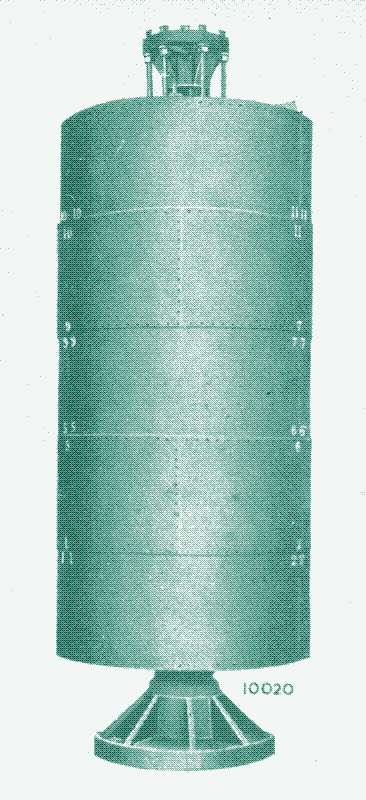
Contrairement à un château d’eau, un accumulateur hydraulique permettait de maintenir une pression uniforme dans l’ensemble du réseau quelque soit le volume d’eau contenu dans son cylindre, car la pression y est générée par le poids du ballast et par non le poids de l’eau elle-même – pour le dire autrement, l’accumulateur hydraulique génère une pression au moyen d’un poids extérieur plutôt que par la seule énergie gravitaire (liée à la différence de hauteur).
Avec un rendement de charge/décharge supérieur à 98 %, et aucune autodécharge, l’accumulateur hydraulique était un dispositif extrêmement efficace sur le plan énergétique.
Des Machines Industrielles Alimentées par la Force Motrice
Son introduction eut deux effets majeurs. Premièrement, elle élargit considérablement l’éventail des opérations susceptibles d’être réalisées par des machines à énergie hydrauliques. Les moteurs à eau connectés au réseau d’eau potable se limitaient alors à de petits appareils domestiques ou des outils d’atelier. Mais Armstrong et d’autres ingénieurs adaptèrent l’usage de l’eau sous haute pression à tout un large spectre d’opérations industrielles nécessitant des puissances importantes, telles que le forgeage, le poinçonnage, l’emboutissage, le bordage, le cisaillage et le rivetage (ancêtre de la soudure).
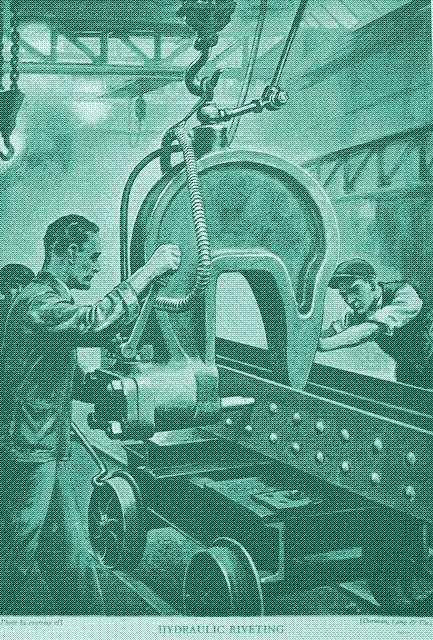
Dans les ports, l’eau sous haute pression servait non seulement à actionner les grues et engins de levage destinés à la manutention de marchandises sur les quais et dans les entrepôts, mais aussi les portes d’écluses, les ponts tournants, ascenseurs à bateaux et cales sèches. Dans les gares de triage, la distribution de force motrice était utilisée pour déplacer le fret et les wagons (au moyen de treuils cabestan hydrauliques) ainsi que pour actionner les plaques tournantes, les monte-charges et engins de transbordement. Toutes ces applications de l’énergie hydraulique auraient été impossibles avec la pression généralement faible et irrégulière au sein des canalisations d’eau courante de l’époque.
Une fois encore, il suffit de regarder l’évolution des techniques de levage pour prendre la mesure du rôle crucial joué par l’énergie hydraulique dans le contexte de l’époque. En 1586, un obélisque de 344 tonnes fut déplacé d’une place de Rome vers une autre place. Domenic Fontana, ancien maçon puis architecte et maître d’œuvre au Vatican, en supervisa le transfert. Il décida, pour assurer cette mission, de soulever l’obélisque et de le poser horizontalement sur un traîneau pour le transporter au centre de la place Saint-Pierre, où il devait être nouvellement érigé. L’opération mobilisa 40 cabestans, actionnés par quelques 75 chevaux et 400 hommes. En 1878, John Dixon érigea un autre obélisque – l’Aiguille de Cléopâtre, d’une masse de 209 tonnes – au moyen de quatre crics hydrauliques de levage, actionnés par quatre hommes.
Les Réseaux de Force Motrice Hydraulique
Deuxièmement, l’accumulateur hydraulique rendit possible le transfert efficace d’énergie sur de longues distances. Dans une canalisation de 30 cm, la perte de charge dans le réseau s’élève à 10 psi par mile (environ 0,4 bar / km), une valeur indépendante de la pression. Par conséquent, en transportant de l’eau à une pression de 70 psi sur une distance de 7 miles (12 km), toute l’énergie initiale est dissipée en sortie. Mais en distribuant de l’eau sur cette même distance à une pression initiale de 700 psi, il résulte une pression de 630 psi à l’arrivée ; le rendement s’élève alors à 90 %.
Le rendement élevé de l’eau sous haute pression comme vecteur énergétique entraîna la construction d’au moins une douzaine de réseaux publics de distribution de force motrice dotés d’accumulateurs – dont la moitié en Grande-Bretagne. Grâce à l’action de machines à vapeur centralisées, l’eau y était pompée vers des accumulateurs hydrauliques, qui distribuaient ensuite l’eau sous haute pression sur un territoire plus ou moins vaste. Un ou plusieurs accumulateurs étaient installés dans chaque station du réseau, tandis que d’autres étaient répartis à des points stratégiques le long des canalisations, comme « sous-stations ».
L’idée d’un réseau de force motrice hydraulique – analogue à celle d’un réseau électrique, qui émergea quelques temps après – avait déjà été esquissée dès 1812 dans un brevet déposé par Joseph Bramah, l’inventeur de la presse hydraulique.
Des années 1870 aux années 1890, des réseaux d’eau motrice sous pression furent ainsi déployés dans les principales villes industrielles de Grande-Bretagne : Kingston upon Hull, London, Liverpool, Birmingham, Grimsby, Manchester et Glasgow. Les compagnies portuaires et ferroviaires furent pionnières dans le développement cette technologie, et en demeurèrent les principales utilisatrices pendant plusieurs décennies.
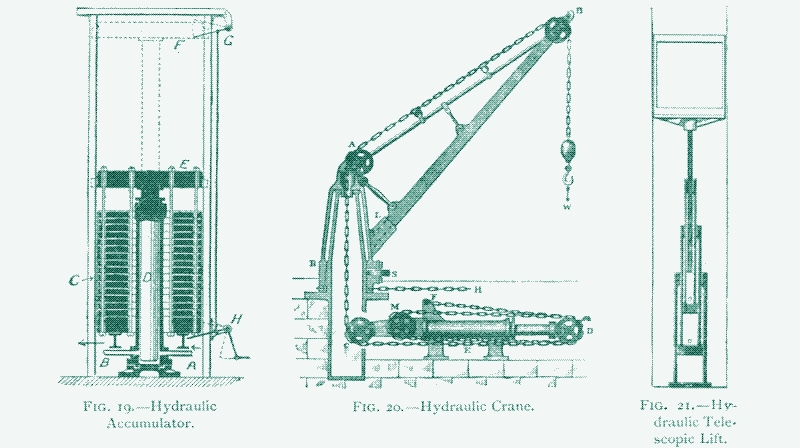
La force motrice hydraulique était en outre utilisée dans des procédés industriels de fabrication, pour actionner les ascenseurs d’immeubles publics, privés et commerciaux, mais aussi différents appareils domestiques et outils d’ateliers artisanaux. Quiconque avait la chance d’être situé à proximité d’une canalisation souterraine pouvait ainsi se raccorder au réseau public. Les consommations d’eau étaient relevées, au même titre que l’eau potable ou l’électricité aujourd’hui.
L’idée d’un réseau force motrice hydraulique – analogue à celle d’un réseau électrique, qui émergea quelques temps après – avait déjà été évoquée dès 1812 dans un brevet déposé par Joseph Bramah, l’inventeur de la presse hydraulique. Mais Bramah, qui avait également imaginé le principe de l’accumulateur et de la grue hydrauliques, était trop en avance sur son temps. Il fallut attendre près de 60 ans pour que ses idées soient mises en pratique par Armstrong et ses contemporains.
La Compagnie d’Énergie Hydraulique de Londres
C’est à Londres que fut construit le plus vaste réseau de force motrice hydraulique, exploité par la “London Hydraulic Company”. À l’apogée de l’entreprise en 1917, pas moins de cinq centrales interconnectées assuraient le pompage d’eau sous haute pression vers une douzaine d’accumulateurs hydrauliques et près de 300 km de conduites souterraines, alimentant en énergie plus de 8 000 machines réparties dans presque toute la ville. Dans les théâtres et autres équipements culturels de Londres, l’eau motrice était utilisée pour déplacer les décors, les consoles d’orgues, les rideaux coupe-feu et les plateaux de scène. La machinerie hydraulique du Tower Bridge était également actionnée par de l’eau sous pression, pompée dans six accumulateurs par des moteurs à vapeur, permettant la levée des bascules.
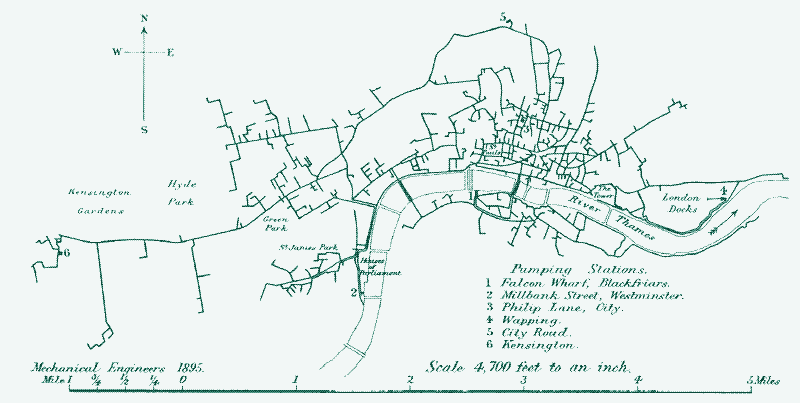
Les bornes à incendie bénéficiaient elles aussi du système haute pression, et plusieurs centaines d’entre elles étaient raccordées au réseau de la London Hydraulic Power Company. Ces dispositifs anti-incendie permettaient par ailleurs d’augmenter la pression au sein des canalisations domestiques en y injectant de petites quantités d’eau sous haute pression, au moyen de pompes à jet. En effet, l’eau comprimée fournie par le service d’eau motrice n’était pas disponible en quantité suffisante pour avoir un réel impact contre les incendies majeurs, tandis que l’eau potable domestique était abondamment disponible, mais à une pression trop faible pour atteindre les derniers étages des immeubles.
À Londres, cinq centrales interconnectées assuraient le pompage d’eau sous haute pression vers une douzaine d’accumulateurs hydrauliques et près de 300 km de conduites souterraines, alimentant en énergie plus de 8 000 machines réparties dans presque toute la ville
Une autre application notable de l’eau sous haute pression à Londres fut le Silent Dustman, un système d’aspiration à énergie hydraulique commercialisé en 1910. Plusieurs grands hôtels en furent intégralement “équipés” : de l’eau courante était utilisée par une pompe à jet pour générer du vide dans un conduit principal, sur lequel venait se brancher le système d’aspiration. Le long de ce conduit, un certain nombre de buses permettaient de brancher des tuyaux souples. La poussière était ainsi aspirée vers le tube principal puis évacuée vers les égouts. Ce système, au fonctionnement à la fois silencieux et efficace, demeura en service jusqu’en 1937.
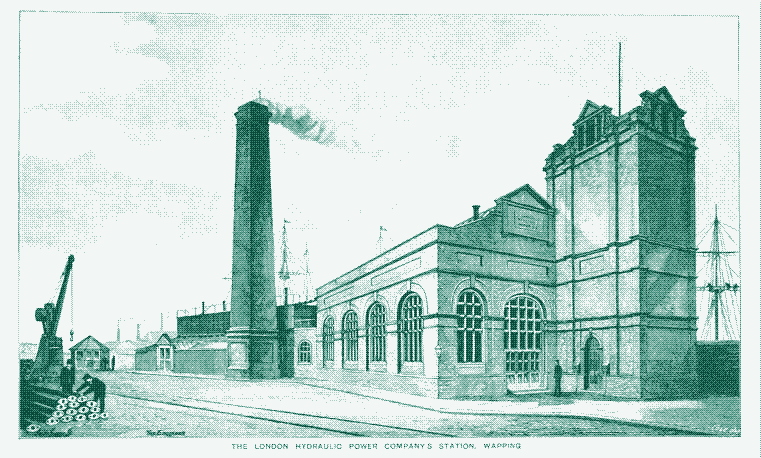
Malgré cela, à Londres, la force motrice hydraulique ne semble pas avoir eu d’impact réellement probant sur la vie quotidienne des habitants. Dans The Hydraulic Age (1980), Brinley Pugh avance que cela est “potentiellement lié au fait que la main d’œuvre domestique était à l’époque abondante et bon marché. Avec les conditions actuelles, l’histoire aurait été différente, dans la mesure où les potentialités offertes par l’énergie hydraulique étaient alors équivalentes à celles de l’électricité aujourd’hui.”
Dans la plupart des réseaux, l’eau était distribuée à une pression de 700 à 800 psi (48 à 55 bar), à l’exception de Manchester et Glasgow où l’eau était comprimée à 1120 psi. Ces deux villes rencontraient en effet une forte demande en énergie à destination de presses hydrauliques, utilisées pour la mise en balle du coton, une opération qui nécessitait une pression plus élevée.
Les Réseaux de Force Motrice en dehors du Royaume-Uni
Les réseaux britanniques firent des émules en inspirant la création de réseaux similaires ailleurs dans le monde : à Anvers en Belgique, Buenos Aires en Argentine, Melbourne et Sydney en Australie. Si les réseaux australiens étaient directement inspirés de ceux déployés au Royaume-Uni (avec 80 km de canalisations, celui de Melbourne fut le second plus grand jamais construit), le système argentin servait au pompage des eaux usées, tandis que le réseau d’Anvers était quant à lui conçu pour la production combinée – on parle aujourd’hui de “cogénération” – d’énergie mécanique et d’électricité. Cette dernière technique visait à palier les importantes pertes en ligne du transport d’électricité à cette époque.
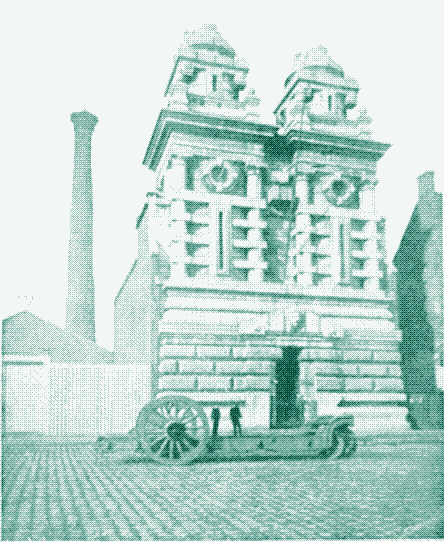
Dans The Hydraulic Age, Brinley Pugh écrit que :
“Concernant la transmission d’énergie, les premières centrales électriques furent confrontées aux mêmes problèmes que les centrales hydrauliques ; le “voltage” de leurs lignes y était l’équivalent de la “pression de service” des conduites d’eau et, par analogie, la chute de tension liée à la résistance électrique des câbles correspondaient à la chute de pression causée par la friction du fluide à l’intérieur des tuyaux. Les premières centrales électriques publiques fournissaient un courant continu : la tension de production était alors à peine plus élevée (de l’ordre de la perte en ligne dans les câbles) que celle délivrée en sortie dans les locaux des usagers, laquelle, pour des raisons de sécurité, devait être inférieure à 250 volts. Du fait de cette contrainte, l’aire de distribution et la quantité d’énergie qui pouvait être fournie demeuraient restreintes.”
Le réseau d’Anvers était conçu pour la cogénération d’énergie mécanique et d’électricité.
La ville d’Anvers utilisait depuis 1865 un réseau d’eau motrice pour alimenter les grues, ponts et écluses de son port. Il vint s’y ajouter en 1893 un second réseau, qui distribuait de l’eau sous haute pression à des sous-stations électriques disséminées dans toute la ville (au nombre de douze d’après la carte – toutefois, seules trois d’entres elles furent effectivement construites). Des turbines hydrauliques y généraient de l’électricité, ensuite distribuée dans un rayon de 500 m via des lignes électriques enterrées – distance maximale à laquelle le courant basse tension pouvait alors être distribué avec un bon rendement.
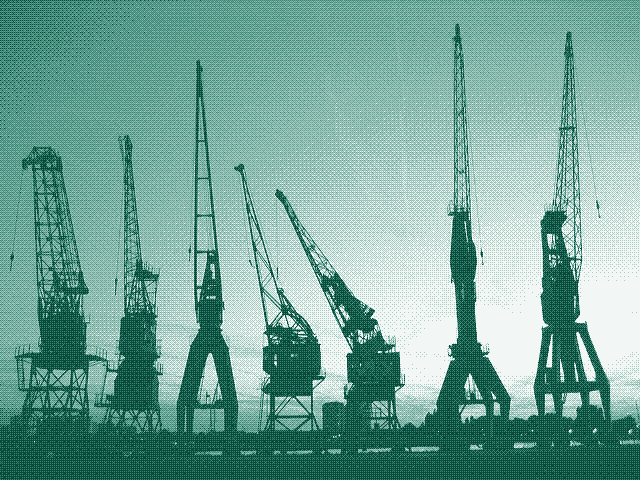
Le système anversois, utilisé pour l’éclairage public, réalisait ainsi à grande échelle ce que les moteurs à eau couplés à des dynamos assuraient à une petite échelle via le réseau d’eau courante (voir le précédent article. Environ 66 % de l’énergie hydraulique était convertie en électricité. À son apogée, le réseau atteignit 23 km de longueur totale, pour une puissance de 1200 CV. Il faut par ailleurs mentionner qu’à Londres, un certain nombre d’habitants utilisaient de petits générateurs domestiques pour produire de l’électricité directement à partir du réseau d’eau courante.
Force Motrice Hydraulique versus Electricité
Le développement fulgurant de la transmission d’électricité haute tension au tournant du siècle rendit immédiatement obsolète des systèmes comme celui d’Anvers. La partie du réseau dédiée à la production d’électricité disparut en 1900. En effet, comprimer de l’eau pour in fine générer de l’électricité induit une quadruple conversion énergétique – et par conséquent des pertes – qui s’avèrent inutiles dès lors que la production et le transport d’électricité deviennent efficaces.
La construction de nouveaux réseaux urbains de distribution de force motrice fut par ailleurs interrompue avant la fin du siècle par le déploiement rapide de réseaux électriques désormais efficaces. “Si le développement de ces systèmes avait démarré quelques années plus tôt, leur succès aurait pu être nettement plus important” écrit Ian McNeil dans son ouvrage Hydraulic Power (1972). “Quelques années plus tard, et ils n’auraient probablement jamais vu le jour.”
Néanmoins, la quasi-totalité des réseaux urbains de distribution d’eau motrice qui furent construits entre 1870 et 1890 restèrent en fonctionnement jusque dans les années 1960 voire 1970, utilisant sur la fin des moteurs électriques plutôt que des machines à vapeur pour le pompage. Le réseau exploité par la London Hydraulic Company fut le dernier à fonctionner : son exploitation perdura jusqu’en 1977. La plupart de ces réseaux publics continuèrent leur expansion au cours des premières décennies du 20eme siècle, et connurent leur âge d’or à la fin des années 1920. Le déplacement des usines vers l’extérieur des villes, à partir des années 1960 et 1970, porta le coup de grâce à leur inéluctable déclin.
Si l’électricité est le vecteur le plus pratique et efficace pour transporter et distribuer l’énergie, comment expliquer que la plupart des réseaux de force motrice hydraulique demeurèrent en service pendant près d’un siècle après son apparition ?
Ceci soulève deux questions. D’une part, pourquoi l’eau motrice n’est-elle pas devenue le vecteur universel de distribution de l’énergie comme l’avaient imaginé Joseph Bramah et William Armstrong ? D’autre part, si l’électricité est le vecteur le plus pratique et efficace pour transporter et distribuer l’énergie, comment expliquer que la plupart des réseaux de force motrice hydraulique demeurèrent en service pendant près d’un siècle après son apparition ?
Les Avantages de l’Énergie Électrique
En tant que vecteur de transmission d’énergie, la force hydraulique présente 3 principaux inconvénients par rapport à l’électricité. Tout d’abord, l’électricité peut être transportée efficacement sur des distances beaucoup plus grandes. La transmission hydraulique était (et demeure) au moins aussi efficace que la transmission électrique pour des distances comprises entre 15 et 25 km. Au-delà, l’électricité se démarque nettement par son meilleur rendement.

Un second inconvénient lié à la transmission de force hydraulique réside dans le fait qu’un réseau de distribution complexe et étendu induit nécessairement des pertes d’énergie supplémentaires. Chaque courbe ou angle dans le tracé des canalisations augmente en effet l’énergie dissipée par friction. Plus le réseau est sinueux, moins il est efficace. De son côté, la transmission électrique n’est pas confrontée à ce problème, ou du moins dans une moindre mesure. Le phénomène de friction au sein des canalisations limite ainsi la quantité de machines qui peuvent être raccordées à un réseau d’eau motrice, tandis qu’une production d’électricité peut virtuellement être divisée en autant d’usagers (points de distribution) que nécessaire.
La troisième contrainte de l’eau motrice est la capacité limitée du réseau de distribution. L’eau sous pression ne peut être transportée qu’au sein de conduites relativement étroites et à une vitesse lente – proche de celle de la marche à pied – afin d’éviter des pertes par friction excessives. En effet, ces pertes augmentent au carré de la vitesse de déplacement de l’eau : pour des vitesses plus élevées le rendement du dispositif chute alors drastiquement, et ce même sur des distances relativement courtes. Ceci impose une limite au débit global dans les conduites, et par conséquent à la puissance maximale fournie par un circuit hydraulique sous pression.
Dans le cas de tuyaux de 10 à 12 cm de diamètre – une taille couramment observée dans la plupart des réseaux d’eau motrice sous pression de l’époque – un système de transmission hydraulique pouvait délivrer une puissance maximale continue de 115 à 205 CV (85 à 150 kW). Des lignes électriques d’une dimension comparable peuvent fournir une puissance de plusieurs ordres de grandeur (puissances de 10) supérieur à cela.
Les Avantages de la Force Motrice Hydraulique
Toutefois, aucune des contraintes évoquées ci-dessus ne s’appliquait aux réseaux dont il a ici été question. Premièrement, tous étaient des systèmes décentralisés, dont le parc de machines desservies était situé dans un rayon n’excédant jamais 15 - 25 km de la source d’énergie. Deuxièmement, les engins hydrauliques alors en usage dans les ports, gares de triages, usines et immeubles se caractérisaient par de faibles vitesses de manœuvre ainsi qu’une fréquence d’utilisation irrégulière, la faible vitesse de transmission de l’hydraulique ne posait donc pas de problème particulier.
Exception faite du système de génération d’électricité déployé à Anvers – et rapidement abandonné – aucun des réseaux de type Armstrong ne fournissait d’énergie à un grand parc de machines en fonctionnement continu. (Mentionnons tout de même les réseaux hydrauliques moyenne pression en Suisse. Troisièmement, les pertes par friction causées par les angles et courbes des conduites étaient limitées, car un tel réseau servait généralement à alimenter un nombre relativement réduit de (très puissantes) machines.
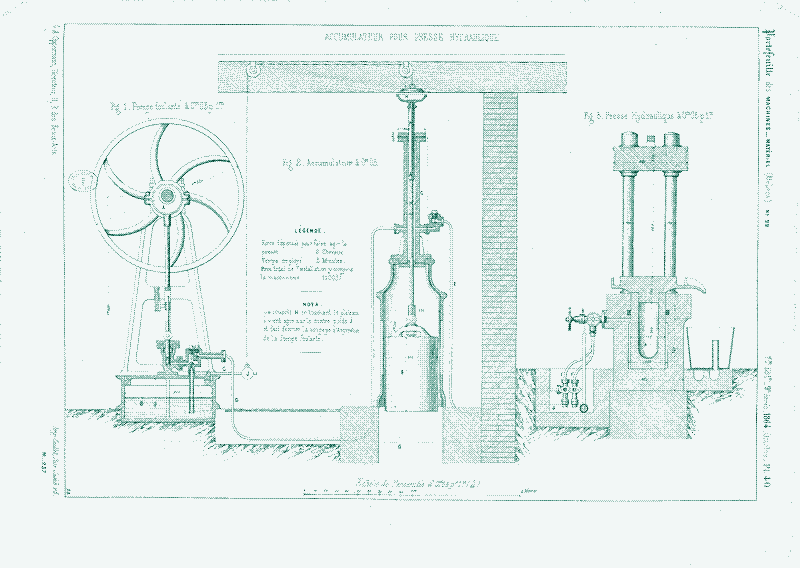
A la fin du dix-neuvième siècle, les limites intrinsèques à la transmission d’énergie hydraulique étaient désormais très bien connues. Ceci n’empêchera pas les ingénieurs de l’époque de se saisir des potentialités uniques offertes par cette technologie, qui sont toujours d’actualité. A titre d’exemple, citons les mots de Robert Zahner, promoteur en son temps d’une autre alternative à l’électricité, l’air comprimé. Dans son livre The Transmission of Power by Compressed Air (1890), il écrivait que :
“Le caractère virtuellement incompressible de l’eau rend la méthode hydraulique impropre au transport d’énergie en quantité constante. Elle peut être mise à profit uniquement dans les cas où la force motrice doit être accumulée et utilisée à intervalles, réguliers ou non, par exemple pour soulever des poids, réaliser des opérations de poinçonnement, de forgeage par compression ainsi que d’autres travaux de nature intermittente, qui requièrent l’application d’une grande force sur une courte distance ou surface.”
La distribution de la force motrice de l’eau est “merveilleusement adaptée aux machineries lourdes et aux engins dont les opérations requièrent la concentration de puissances élevées, des mouvements de va-et-vient linéaires, et un fonctionnement intermittent” écrit quant à lui Louis Hunter dans The Transmission of Power (1991). La principale qualité de l’accumulateur hydraulique est de permettre le fonctionnement de machines qui nécessitent une puissance grandement supérieure à celle que peut fournir la source d’énergie – selon le principe de Pascal de “multiplication des forces”.
A la fin du dix-neuvième siècle, les limites intrinsèques à la transmission d’énergie hydraulique étaient désormais très bien connues. Cela n’empêchera pas les ingénieurs de l’époque de se saisir des potentialités uniques offertes par cette technologie, toujours d’actualité
Lorsqu’une force ou un couple élevé sont nécessaires, les systèmes hydrauliques sont une solution beaucoup plus compacte et efficace énergétiquement que les mécanismes d’entraînement mécaniques ou électriques. En effet, les moteurs électriques comme les moteurs à combustion ont généralement besoin de composants mécaniques (boîtes de vitesse, chaînes, courroies) pour convertir leur vitesse de rotation élevée en une vitesse plus faible avec un couple plus important.
De même, les systèmes hydrauliques permettent de générer assez facilement un mouvement linéaire (translation) via le recours à des vérins hydrauliques tandis que l’énergie électrique doit recourir pour cela à de coûteux moteurs linéaires ou à des dispositifs mécaniques, de type transmission à pignon-crémaillère. C’est en ce sens que les énergies hydrauliques et électriques s’avèrent complémentaires : une des contraintes liées à la transmission hydraulique était la relative difficulté à convertir un mouvement linéaire en mouvement rotatif.
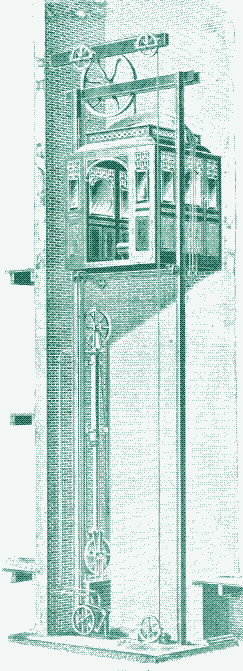
Les turbines Pelton constituaient pour cela la solution la plus évidente. Leur vitesse de rotation élevée impliquait cependant l’ajout de mécanismes d’engrenages pour faire fonctionner des machines à faible vitesse. On disposait alors de systèmes hydrauliques de type vérin, capables de fournir une énergie rotative à des vitesses variables ou faibles, mais ces dispositifs offraient peu d’avantages comparés à des boîtes de vitesse mécaniques ou électriques.
Un troisième avantage conséquent de l’hydraulique est que l’énergie est toujours à disposition au sein des conduites et de l’accumulateur, mais ne subit aucune perte même quand la demande est nulle. Lorsqu’aucune des machines reliées au réseau n’était en fonctionnement, les accumulateurs hydrauliques maintenaient les conduites sous pression sans utiliser d’énergie supplémentaire. Ce dernier point constitue un avantage considérable dans le cas de machines utilisées de manière intermittente.
L’Hydraulique Aujourd’hui
L’énergie hydraulique est toujours utilisée de nos jours, en particulier pour des équipements d’industrie lourde qui impliquent des mouvements linéaires lents mais puissants, ainsi que dans des engins de travaux ou terrassement comme les pelleteuses. Mais les accumulateurs hydrauliques et réseaux publics de force motrice sous pression ont pour leur part disparu.
Le fluide sous pression n’est désormais plus de l’eau mais de l’huile, mélangée à des additifs. (L’huile végétale avait déjà été utilisée comme medium hydraulique au 19ème siècle). Contrairement à l’eau, l’huile ne gèle pas et n’est pas corrosive. Ceci augmente toutefois le coût de l’énergie hydraulique et ne permet évidemment plus le rejet du fluide dans les égouts, le port ou la mer en cas de maintenance ou de fuite.
C’est en partie du fait de la conversion à l’huile que furent développés des systèmes hydrauliques embarqués, circuits autonomes généralement composés d’une pompe, d’un accumulateur et d’un circuit de bouclage, prêts à être couplés à un moteur électrique ou diesel. Dans ce type de technologies les accumulateurs hydrauliques sont en principe beaucoup plus petits, utilisent un gaz pour compresser le fluide, et ne garantissent pas une pression constante au sein du circuit.
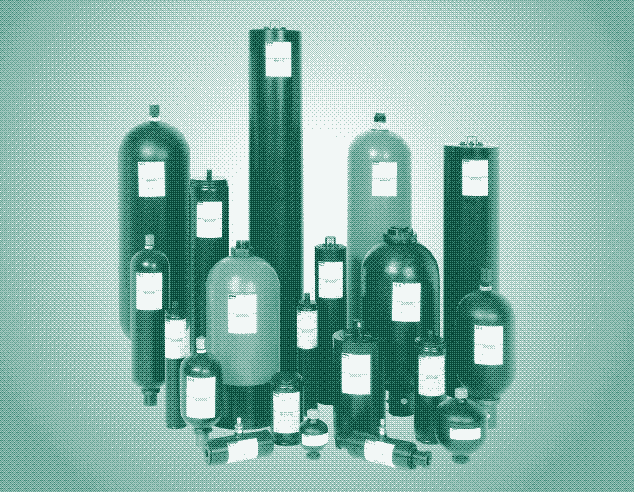
Si elle conserve une partie des avantages pratiques de l’hydraulique – à savoir de pouvoir transférer une grande quantité d’énergie et la restituer de manière précise, au moyen de composants très compacts – la version moderne de cette technologie élimine cependant un des principaux avantages propres aux réseaux de force motrice plus centralisés des dix-neuvième et vingtième siècles en termes d’efficacité. En effet, au sein d’un réseau municipal, déployé à l’échelle urbaine, une source relativement réduite d’énergie – en l’occurrence, une poignée d’accumulateurs hydrauliques – suffisait à assurer le fonctionnement d’un grand nombre de machines très puissantes. Les moteurs des stations de pompage n’avaient donc pas besoin d’être surdimensionnés pour couvrir les pics de charge.
Un avantage des réseaux de force motrice hydraulique était qu’une source d’énergie de relativement faible puissance suffisait à assurer le fonctionnement d’un grand nombre de machines très puissantes, distribuées dans toute une ville.
Brinley Pugh déplore ainsi cette évolution dans The Hydraulic Age (1980) :
“Il y a un siècle, seules quelques très grandes machines – les ponts à bascules et, ponctuellement, certaines presses hydrauliques – étaient équipées de leur propre système de pompage. On a vu ces derniers temps cette tendance s’étendre à des machines alimentées par la force motrice de toutes tailles et fonction, au point de devenir une pratique courante. Avec les systèmes hydrauliques embarqués, chaque composant sera bientôt actionné par son propre moteur et disposera de ses propres instruments de contrôle, filtres, etcetera, avec le contrôle périodique et la maintenance que cela implique.”
“Le moteur fonctionnera en continu tant que le circuit est en fonctionnement, quel que soit la pression dans la pompe qu’il alimente. Dans le cas où plusieurs unités sont installées, elles ne fonctionneront pas toutes à pleine puissance simultanément. Des économies substantielles d’énergie pourraient être réalisées en y substituant une usine de pompage centralisée alimentant plusieurs unités ; du fait de la diversification des machines, la puissance maximale requise à un instant donné sera toujours inférieure à la somme des puissances individuelles.”
“L’avantage d’une station centralisée par rapport à plusieurs unités plus modestes réside dans sa capacité à répondre à une demande variable. De petites stations autonomes doivent chacune disposer d’une capacité suffisante pour satisfaire la demande crête (maximale) dans leur aire de distribution, or ces pics de charge n’interviennent pas au même moment. A contrario, une centrale regroupant toutes les aires géographiques des sous-stations se contentera de répondre au pic de demande totale simultanée, lequel sera normalement inférieur à la somme des pics de puissance locaux.”
Des Alternatives à l’Électricité
Comme dans le cas d’autres techniques de transmission de l’énergie mécanique – tels que les systèmes de pompes avec tige à saccades et les courroies de transmission sans fin – c’est la meilleure efficacité de la transmission électrique sur de longues distances qui a en grande partie causé la disparition des réseaux urbains de distribution de force motrice. Toutes ces alternatives à l’électricité, aujourd’hui oubliées, mériteraient d’être réétudiées aux fins d’applications spécifiques, dans la perspective d’un système énergétique plus décentralisé et basé sur les énergies renouvelables. On peut ainsi imaginer que les accumulateurs hydrauliques à poids puissent être alimentés à l’énergie solaire, éolienne, voire musculaire (à pédale).
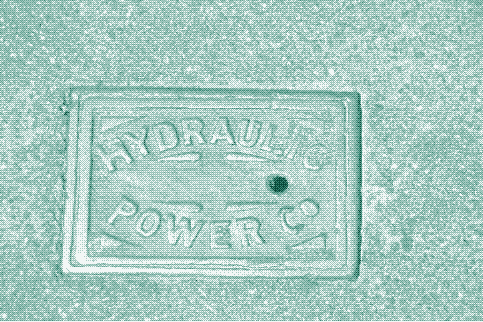
Au tournant des années 1900, la supériorité de l’électricité pour la transmission d’énergie sur de très grandes distances faisait désormais consensus. Sur de moyennes distances, toutefois, quelques auteurs mettaient en doute sa pertinence. R. Kennedy écrivait par exemple dans Modern Engines and Power Generators (1905) :
“L’électricité offre, en matière de transmission d’énergie, un grand nombre d’avantages dans la plupart des cas. Les ingénieurs électriciens idéalisent cependant la chose. Ils sont en effet bien souvent prompts à oublier d’autres technologies, lesquelles disposent, dans bon nombre de cas, d’avantages considérables par rapport à l’électricité.”
W.C. Unwin, auteur au dix-neuvième siècle de l’ouvrage le plus complet de l’époque sur la transmission d’énergie (On the Development and Transmission of Power from Central Stations), exprima en 1894 des réserves similaires :
“Bien que la distribution d’électricité soit indéniablement amenée à jouer un rôle prochain dans le développement des réseaux de distribution de l’énergie, on observe ces temps-ci une tendance à ne considérer que l’option électrique, et à négliger d’autres moyens de transport de l’énergie qui ont été utilisés avec succès par le passé et seront, dans des conditions adéquates, toujours employés à l’avenir. Dans le cas de la transmission sur moyenne distance, on dispose de plusieurs alternatives crédibles, et la transmission électrique n’a pas, dans un tel cas et jusqu’à ce jour, établit sa supériorité d’aucune manière.”
Le prochain épisode de notre série sur la transmission d’énergie s’intéressera à l’air comprimé, qui est probablement l’alternative à l’électricité la plus crédible.
Kris De Decker
Cet article est dédié à Charles Steele. RIP.
Sources (par ordre d’importance) :
The Hydraulic Age, B. Pugh, 1980
Hydraulic Power (Industrial Archaeology), Ian McNeil, 1972
On the Development and Transmission of Power from Central Stations, W.C. Unwin, 1894. Also here.
Hydraulic Machinery, with an introduction to hydraulics, R.G. Blaine, 1897
A History of Industrial Power in the U.S., 1780-1930: Vol 3: The Transmission of Power, Louis C. Hunter and Lynwood Bryant (1991)
Modern Engines and Power Generators; a Practical Work on Prime Movers and the Transmission of Power, Steam, Electric, Water and Hot Air – Volume One, R. Kennedy, 1905
Modern Engines and Power Generators; a Practical Work on Prime Movers and the Transmission of Power, Steam, Electric, Water and Hot Air – Volume Six, R. Kennedy, 1905
Power and Power Transmission, E.W. Kerr, 1908
Remnants of Early Hydraulic Power Systems (PDF), J.W. Gibson, 3rd Australasian Engineering Heritage Conference 2009
L’eau à Genève et dans la région Rhône-Alpes: XIXe-XXe siècles, Serge Paquier, 2007
L’eau des villes: Aux sources des empires municipaux, Géraldine Pflieger, 2009
Revue technique de l’Exposition universelle de 1889, Section II, récepteurs hydrauliques (PDF), 1893
L’usine des forces motrices de la Coulouvrenière à 100 ans: 1886-1986, Services industriels, 1986
Waterdruk in Antwerpen. Een stroom van elektriciteit", Dirk De Vleesschauwer and Noël Kerckhaert, 1993
Kroniek van de stroomverdeling van Antwerpen-stad tot de Rupelstreek tot de Eerste Wereldoorlog, Geschiedkundige Studiegroep Ten Boome. (website)
Het Zuiderpershuis, een monument. Brochure bij de tentoonstelling n.a.v. Open Monumentendag 2010 (PDF), Steunpunt Industrieel en Wetenschappelijk Erfgoed, 2010.
The Centrifugal Pump, Turbines, and Water Motors, Including the Theory and Practice of Hydraulics, Charles Herbert Innes, 1898
Metropolitan Works: Collected Papers on London History, Ralph Turvey, date unknown.
Hydraulic Power Company, The Vauxhall Society, 2012 (website)
London Hydraulic Power Co, Grace’s Guide, date unknown (website)
Hydraulic Power, NSW HSC Online (website)
The Transmission of Power by Compressed Air, Robert Zahner, 1890
Water Engines, The Museum of Retrotechnology, 2011 (website)
The History of Cranes (The Classic Construction Series), Oliver Bachmann,1997.
On the employment of a column of water as a motive power for propelling machinery, William Armstrong, 1840