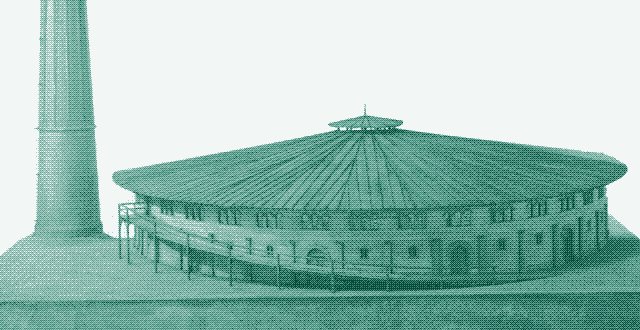
Il y a environ un an, nous avions présenté une technique constructive médiévale qui pourrait permettre d’importantes économie de matière, donc d’énergie grise, dans les constructions en briques : la voûte catalane. Or, il existe également une technique de production de briques et tuiles de terre cuite, inventée au cours du 19ème siècle, qui s’avère quant à elle particulièrement efficace sur le plan énergétique : le four Hoffman, version géante du poêle de masse.
On déplace le foyer de combustion au sein de l’édifice circulaire, dans un processus continu d’une très grande efficacité énergétique.
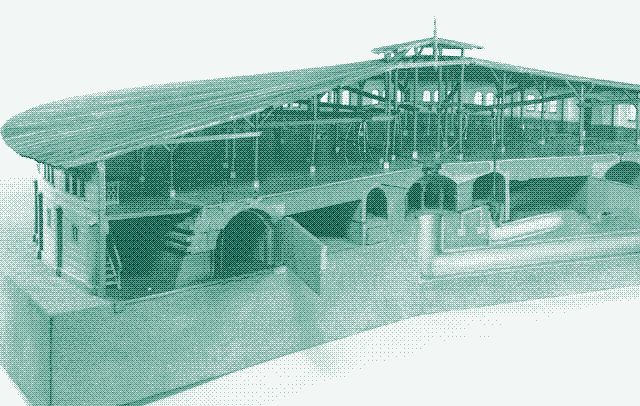
Un « four Hoffman », aussi appelé « four circulaire » ou « four continu à foyer mobile », était un immense four destiné à cuire de l’argile à une température d’environ 1000° Celsius (1830°F) pour la fabrication de briques, tuiles, carreaux et autres produits de terre cuite. De forme circulaire, ovale ou rectangulaire, la structure briquetée était constituée d’une galerie virtuellement infinie – d’où l’appellation de « four continu » – divisée en 12 à 24 chambres de cuisson. Ces chambres étaient à la fois connectées entre elles, et reliées par des carneaux à un conduit commun débouchant sur une grande cheminée. Chacune d’entre elles disposait en outre d’une ouverture en ogive sur l’extérieur, par laquelle enfourner et défourner les briques, fermée soit par une porte, soit par une cloison temporaire en briques.
Les chambres de cuisson étaient remplies de briques (25 000 environ) puis mises en chauffe l’une après l’autre. La chaleur contenue dans une chambre servait ainsi non seulement à cuire les briques qu’elle contenait, mais également à préchauffer les briques non cuites disposées dans les chambres suivantes. Dans le même temps, un courant d’air frais, introduit via la porte de la chambre en cours de défournement, parcourait la galerie dans le sens inverse par rapport à la progression du foyer, refroidissant ainsi les briques déjà cuites dans les chambres précédentes. Le feu était ainsi « chassé » vers l’avant de chambre en chambre, dans un processus continu d’une très grande efficacité énergétique. Selon la taille du four, il fallait entre une et six semaines au foyer pour effectuer une rotation complète autour de la galerie.
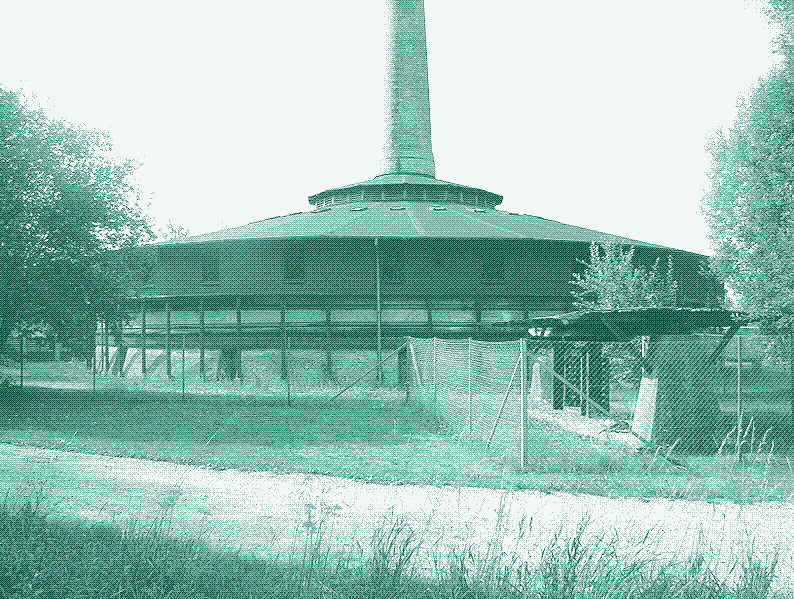
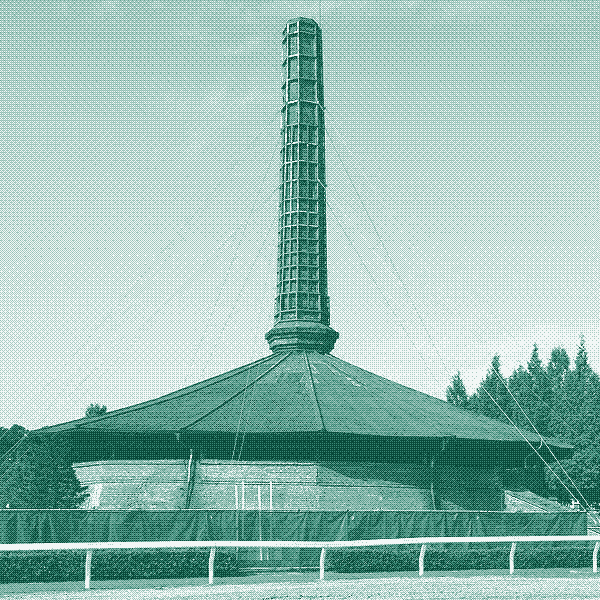
Le concept de four circulaire fut breveté en Allemagne par l’architecte berlinois Frederick Hoffmann en 1858. Il révolutionna l’industrie de production de briques et de tuiles en terre cuite pour de multiples raisons : en premier lieu, cette technique permis d’améliorer la qualité et l’homogénéité des articles en céramique ; elle était par ailleurs beaucoup plus économique à la fois en combustible et en main d’œuvre ; enfin, elle augmenta la production de façon spectaculaire – jusqu’à 10 millions de briques par usine et par an. Dans les premières décennies de la révolution industrielle, la croissance démographique était telle que les fabricants de briques peinaient à satisfaire la demande pour ce matériau. Le four Hoffmann permis de produire massivement briques et tuiles ; pourtant, en dépit de sa complexité, l’ensemble du processus de cuisson était réalisé sans aucune machine.
Une production ininterrompue
Le four Hoffman est un four dit « continu », c’est-à-dire que la cuisson est assurée 24 heures par jours, 7 jours par semaine, 365 jours par an (à l’exception des périodes d’entretien ou de réparation). Avant son invention, la cuisson des briques et tuiles était réalisée dans des fours dits « périodiques ». Les matériaux céramiques ne devant pas être chauffés ou refroidis trop rapidement, cette ancienne technique demandait beaucoup de temps et de main-d’œuvre. D’une part, l’intensité du feu devait être augmentée très lentement et avec précaution, d’autre part, les briques cuites devaient rester en place dans le four pendant sept jours à partir de l’extinction du feu. Pendant toute cette durée, le four périodique ne pouvait être utilisé pour cuire une nouvelle pile de briques. En outre, la structure du four en elle-même devait être montée en température à chaque cycle de cuisson, et l’essentiel de la chaleur générée lors du processus de combustion était dissipée par une cheminée ou par le toit, gaspillant d’importantes quantités de combustible.
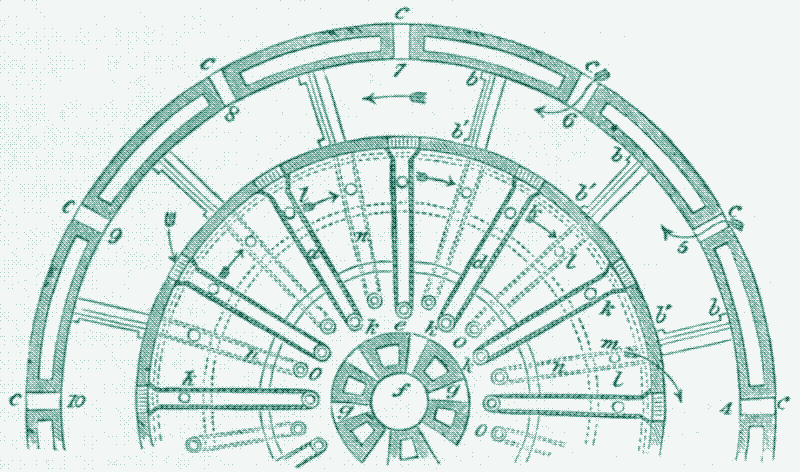
Le four Hoffmann original était de plan circulaire, avec une large cheminée disposée en son centre (illustration ci-dessus), mais cette forme fut assez rapidement abandonnée au profit d’une structure ovale, finalement remplacée par une forme oblongue avec deux galeries parallèles, adjacentes et réunies entre elles à chaque extrémité par deux canaux demi-circulaires (illustration plus bas). La cheminée pouvait se situer au centre, ou bien être attenante à l’édifice. Un plan rectangulaire présentait l’avantage de réduire l’emprise au sol du bâtiment, de faciliter l’utilisation du four, et permettait de plus une circulation plus homogène de l’air.
L’alimentation du four
Certains fours Hoffmann étaient alimentés au gaz, mais dans la majorité des cas c’est le charbon qui était utilisé comme combustible. La voûte d’un four circulaire était percée sur plusieurs rangées de petits orifices d’alimentation – hermétiquement couverts par des couvercles métalliques – appelés « puits de chauffe » ou « trous de charge » (voir dessin et image ci-dessous). Les « chauffeurs » 1 expérimentés introduisaient des fines de charbon (fines particules de charbon pulvérisé) en petites quantités précises par ces orifices situés à l’aplomb des chambres contenant les briques à cuire, en utilisant une petite pelle à charbon. 2
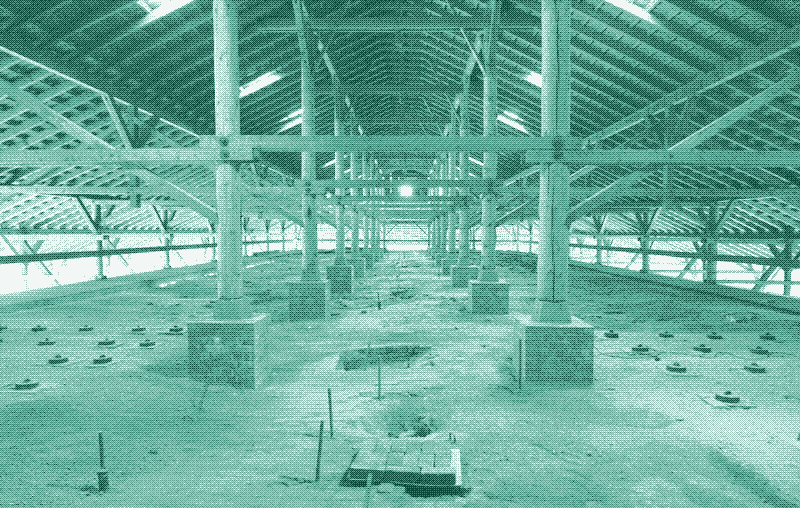
Ces ouvriers travaillaient de concert avec les « enfourneurs », ouvriers briquetiers qui réalisaient les piles de briques crues (aussi appelées « briques vertes ») au sein des chambres. Afin d’assurer une cuisson uniforme, les briques étaient agencées en quinconce, de manière à laisser des vides au sein des piles. En-dessous de chaque puits de chauffe aménagé dans la voûte de la galerie, les piles de briques formaient ainsi autant de « foyers » où introduire, successivement, le combustible. Au centre de ces piles, les nombreuses cavités recevaient le combustible assurant la cuisson, tandis qu’à la périphérie des briques disposées en saillie l’empêchaient de tomber directement au sol, assurant ainsi une répartition homogène sur toute la hauteur.
Une fois les piles réalisées, la chambre était fermée au moyen d’une porte ou d’une cloison temporaire en briques, qui ne serait ouverte que plusieurs semaines plus tard, au moment de défourner les briques. Il n’était pas nécessaire d’entrer dans la chambre pour y démarrer la cuisson : une fois que les gaz chauds issus des chambres voisines avaient suffisamment préchauffés la température, l’air ambiant y était assez chaud pour déclencher la combustion spontanée (c’est à dire sans flamme ni étincelle) du charbon versé via le puits de chauffe.
Le principe de fonctionnement
Dans son livre « Cement, concrete and bricks », publié en 1914, Alfred B. Searle fournit une description à la fois claire et détaillée du fonctionnement exact d’un four Hoffmann rectangulaire. Malgré sa longueur, son explication s’avère très instructive, la voici donc – avec quelques légères adaptations – dans son intégralité :
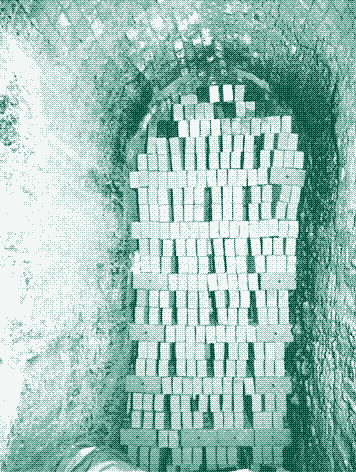
« En considérant que le four fonctionne déjà à plein régime, il se produit les étapes suivantes : le combustible est introduit dans les trous de chauffe à l’aplomb de trois chambres (1, 2 et 3). Chaque orifice reçoit une petite charge de combustible tous les quarts d’heure. La cuisson touchera bientôt à sa fin dans la chambre numéro 1. Un appel d’air va alors acheminer les gaz brûlants issus de la combustion jusqu’aux cinq chambres suivantes (4, 5, 6, 7 et 8) et préchauffera ainsi doucement les briques, sans que cela ne requière d’attention ou d’intervention particulière. Après quoi, la température des gaz sera redevenue si basse qu’ils ne seront plus d’aucune utilité, et seront alors évacués vers le conduit principal, pour ensuite rejoindre la cheminée. Pendant ce temps, tous les registres 3 entre les chambres 1 à 7 et le conduit central sont maintenus fermés, de sorte que l’intégralité de la chaleur disponible est utilisée pour préchauffer les briques crues, en attente de cuisson. »
« Les chambres 9, 10 et 11 contiennent des briques crues fraîchement disposées, lesquelles doivent être séparées du reste du four. Leur température doit être élevée à un minimum de 120 degrés Celsius, (248°F) par une autre source de chaleur. Les chauffer au moyen des gaz résiduaires (issus de la combustion) entraînerait l’apparition d’une écume blanchâtre (kiln scumming) en réaction au dioxyde de soufre ; selon l’usage, cette esthétique plus irrégulière peut ne pas être un problème, auquel cas les briques peuvent directement « entrer dans la ronde du four » (round of the kiln), sans être préchauffées. En règle générale, néanmoins, les briques doivent être chauffées avec un air aussi pur que possible, jusqu’à atteindre une température suffisante pour qu’il ne puisse s’y former aucun condensat à leur surface. L’air chaud le plus pur à disposition est celui qui parcourt les chambres contenant les briques en cours de refroidissement (14, 15 et 16) ; c’est pourquoi, dans de nombreux fours, des conduits ont été spécifiquement aménagés à cette fin. »
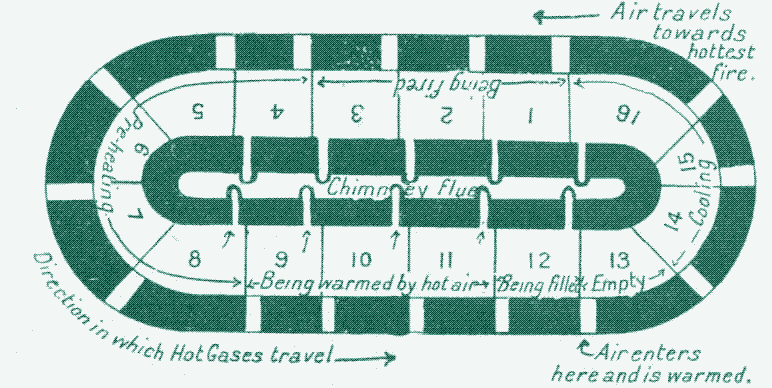
« Dès lors que les briques ont atteint une température d’environ 120 degrés Celsius (248°F), la cloison séparant les chambres 8 et 9 est ôtée. Le registre vers la cheminée est fermé dans la chambre 8 et l’arrivée d’air chaud interrompue dans la chambre 9. Les gaz chauds produits par le combustible arrivent alors dans la chambre 9, dont on dit qu’elle « entre dans la ronde du four ». Pendant ce temps, la chambre 12 a été remplie, et la chambre 13 a été vidée ou est en train de l’être. »
« Les chambres 14, 15 et 16 contiennent des briques en cours de refroidissement, action réalisée automatiquement par le tirage thermique du four, qui génère un appel d’air frais via la porte de la chambre 13. Cet air neuf entre dans un premier temps en contact avec des briques quasiment froides et, au fil de sa progression, est graduellement réchauffé par la chaleur des briques en cours de refroidissement ; lorsqu’il atteint les chambres 1, 2 et 3, où le combustible se consume encore, cet air se trouve à la même température que le briques les plus chaudes, assurant ainsi – sous réserve d’une utilisation rigoureuse du dispositif – une combustion complète avec récupération de pratiquement toute la chaleur. »
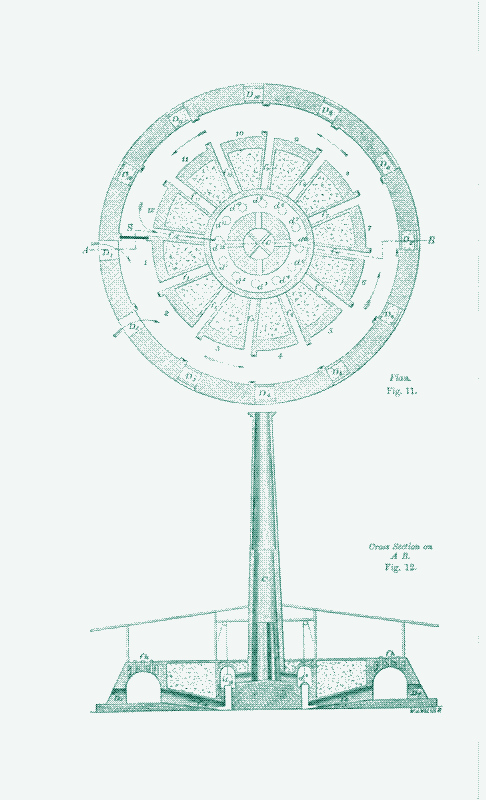
« Si la description d’un four continu peut faire paraître son fonctionnement compliqué, il est en réalité assez simple. Dès lors qu’une chambre est remplie, son contenu est d’abord préchauffé par de l’air chaud, avant d’entrer dans la ronde du four, comme décrit plus haut. Aucune surveillance particulière n’est requise jusqu’à ce que la température n’y soit devenue suffisamment élevée pour que l’introduction d’une petite quantité de combustible suffise à démarrer la cuisson. Dès que le contenu de la chambre est suffisamment monté en température, l’alimentation en fines de charbon est interrompue, une autre chambre entre dans la ronde, et ainsi de suite ; il se trouve ainsi en permanence une chambre en train d’être vidée et une autre en train d’être remplie, tandis que le feu circule autour de la galerie du four dans un mouvement continu et parfaitement régulier. »
Un fonctionnement délicat
Il est évident que la conduite d’un four Hoffmann nécessitait un savoir-faire ainsi qu’une attention accrue. Si la température était trop élevée, les briques sortaient alors déformées. Si, à l’inverse, la température était trop basse, les briques étaient poreuses et fragiles. Si le préchauffage ou le refroidissement des briques s’effectuait trop rapidement, il en résultait une production fendillée. Le chef cuiseur, ouvrier briquetier en charge du four, s’assurait que la cuisson était complète par une série d’essais, mesures de rétrécissement et cônes pyroscopiques (image ci-dessous). Dans un four Hoffman bien exploité, le taux de briques défectueuses était de 3 % seulement, mais pouvait atteindre 50 % dans le cas d’une utilisation peu rigoureuse.
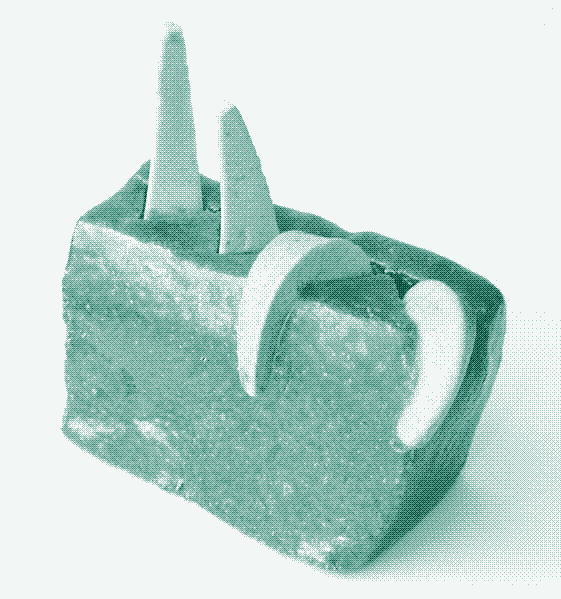
Un tunnel infini
Outre une mauvaise gestion du four, les conditions météorologiques représentaient un autre risque. Lorsqu’on utilise une cheminée pour créer un phénomène de tirage, les perturbations atmosphériques que créé localement un orage entraînent nécessairement une cuisson moins homogène. C’est pourquoi, dans certains fours plus tardifs, de grandes soufflantes furent installées, afin d’obtenir une ventilation à la fois plus puissance et plus constante (accélérant par la même occasion la cadence du procédé). Les grands deltas de température entre l’intérieur et l’extérieur compliquaient également le fonctionnement du four.
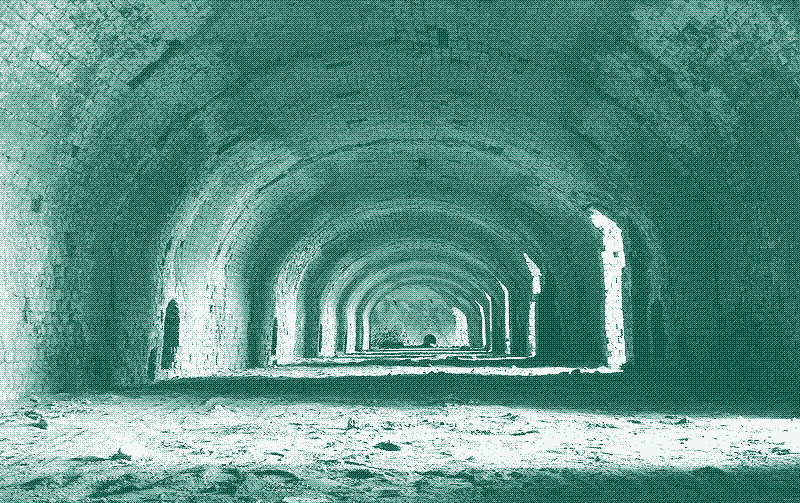
La plupart des fours à cuisson continue n’étaient en réalité pas constitués de 12 ou 24 chambres séparés – même si cela rend l’explication du système Hoffmann plus commode. Lesdites chambres (ou « cellules de cuisson ») n’étaient en fait que des portions théoriques d’un seul et même tunnel, qui pouvaient effectivement être séparées les unes des autres par de grands registres en tôle (relevés et abaissés de l’extérieur) ou, plus tard, par des toiles de papier kraft ou de tissu, enflammées au moment opportun par le courant d’air brûlant en provenance des chambres précédentes.
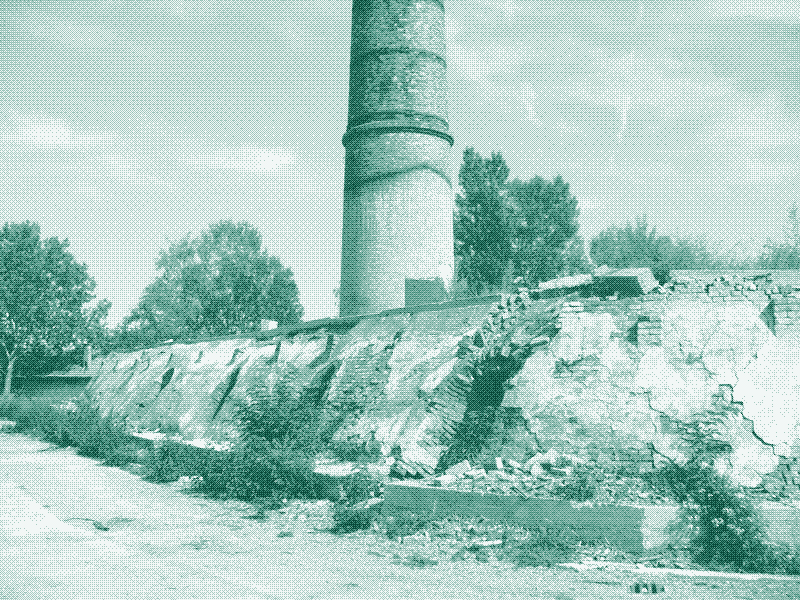
Néanmoins, à n’importe quelle étape du procédé, on comptait un maximum de trois cloisons (shutters) en place, de sorte qu’un four Hoffmann ne comprenait jamais simultanément plus de 3 chambres – l’une d’entre elles étant de grande dimension. La fonction de ces cloisons ou rideaux séparatifs était essentiellement de bien maîtriser le tirage des fumées, notamment en empêchant l’air entrant de circuler dans le mauvais sens au sein de la galerie.
Une version géante du poêle de masse
Assez étonnamment, le fonctionnement d’un four Hoffmann s’avère très similaire à celui d’un poêle en faïence (aussi appelé « poêle de masse ») – un dispositif très efficient utilisé depuis l’époque médiévale pour chauffer l’intérieur des bâtiments. Dans les deux cas, un système complexe de conduits et tuyaux conserve les gaz chauds à l’intérieur de l’enveloppe aussi longtemps que possible. Ces gaz ne peuvent s’échapper par la cheminée qu’après avoir suffisamment baissé en température pour n’être plus utiles sur le plan énergétique.
Ceci rend le processus de combustion extrêmement efficient (la quasi-totalité de la chaleur produite étant mise à profit) et relativement propre (du fait de la combustion complète, la cheminée ne rejeté que très peu de fumées).
Dans un four Hoffmann, les gaz sortent de la cheminée à une température inférieures à 130 degrés Celsius (266°F), tandis qu’ils peuvent atteindre 800 degrés Celsius (1472°F) voire plus dans un four périodique – gaspillant alors une importante quantité d’énergie, donc de combustible, comme dans un poêle à bois à faible rendement. En moyenne, la consommation en combustible d’un four Hoffmann représente environ un tiers de la consommation d’un four périodique.
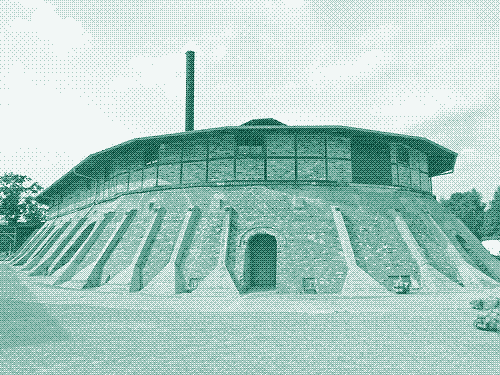
D’autres points communs sont à trouver entre les poêles de masse et les fours Hoffmann. Tous deux émettent de la chaleur en continu et ne doivent être alimentés que de temps en temps afin de prolonger la combustion. De même que pour un poêle, le rendement énergétique d’un four Hoffmann augmente avec sa taille. En conséquence, un des rares inconvénients des fours Hoffmann était le grand terrain qu’impliquait leur emprise au sol. Le périmètre minimum de 68 mètres (224 pieds) pouvait atteindre 100 à 200 mètres (328 à 656 pieds) pour certains fours rectangulaires.
Il existait néanmoins une différence majeure entre les fours circulaires et les poêles de masse : un four Hoffmann disposait d’une bonne isolation grâce à des murs massifs (environ un mètre d’épaisseur), empêchant ainsi la chaleur de se dissiper de l’intérieur de l’édifice vers l’extérieur. Ce n’est pas le cas d’un poêle de masse, dont la fonction est précisément de réchauffer l’air ambiant.
Malgré leur haut rendement, les fours Hoffmann n’étaient pas pour autant des usines particulièrement saines et agréables. Les ouvriers chauffeurs couverts de suie n’étaient pas plus satisfaits de cet environnement que les habitants des alentours. Néanmoins, ces externalités négatives sont plus liées à l’ère industrielle qui a vu se développer les fours Hoffmann qu’à cette technique en tant que telle – l’usage du charbon était alors largement répandu et les cheminées n’étaient pas équipées d’épurateurs de gaz.
Certains fours circulaires étaient alimentés au gaz (ici encore, comme certains poêles en faïence) ; ils pourraient en principe fonctionner avec divers combustibles issus de la biomasse, ou à l’électricité (propre). Il n’y a aucune raison pour qu’un four Hoffmann actuel soit plus énergivore et polluant qu’une briqueterie ou une cimenterie moderne.
Fours Hoffmann à foyers multiples
Le four Hoffmann se diffusa rapidement – en 1870, soit une décennie après la construction du premier four de ce type, on dénombrait déjà 639 unités en fonctionnement dans le monde entier. Il demeura, pendant un siècle, la principale technologie de cuisson de briques, tuiles et conduits en céramique. Le dessin d’origine fut par la suite adapté en différentes formes, dont certaines assez spectaculaires.
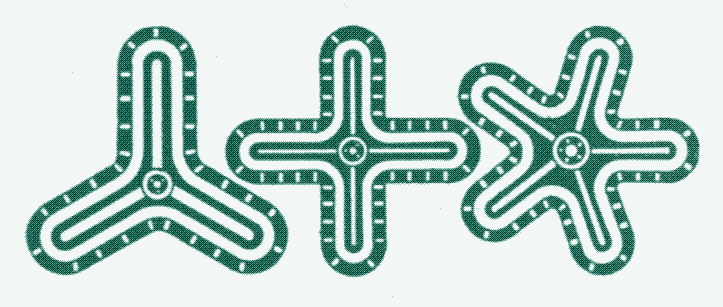
En Suisse, Jacob Bührer apporta une amélioration considérable au four Hoffman. En concevant un four dont le tunnel était presque deux fois plus long et deux fois plus étroit que dans la configuration traditionnelle, il parvint à un très haut rendement énergétique ainsi qu’à une forte augmentation de la production. Afin de surmonter les difficultés constructives d’une part, et d’autre part les déperditions de chaleurs inhérentes à cette forme extrêmement allongée et étroite, Bürher eut l’idée de faire serpenter le tunnel en zigzag. Tandis que le four présente une emprise extérieure carrée, la longueur effective de la galerie est presque deux fois plus élevée que dans un four Hoffmann classique.
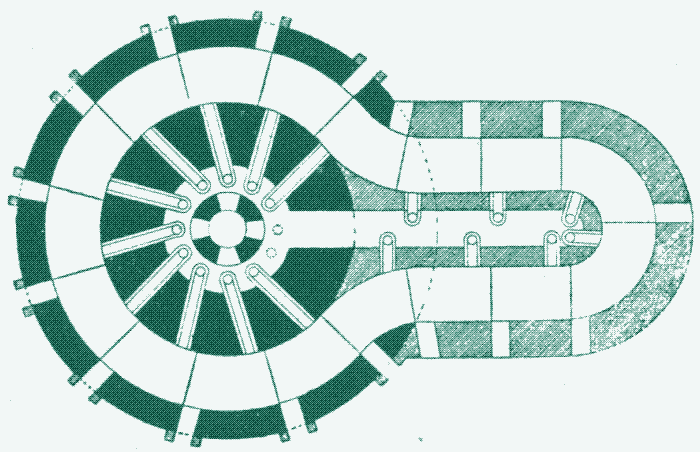

Lorsque le volume à produire était très conséquent, on construisait des fours en zigzag (shank kilns), de formes similaires à l’un des plans ci-dessus. Grâce à cette forme particulière, plusieurs foyers pouvaient être entretenus simultanément avec une moindre main-d’œuvre, tandis que le coût de construction était inférieur à celui de la construction de plusieurs fours continus d’une capacité totale équivalente. Au tournant du 20ème siècle, on dénombrait déjà plus de 200 de ces fours à travers tout le continent, avec une production de 5 à 50 millions de briques par an pour chacun d’entre eux.
Il arrivait qu’un four soit agrandi selon le principe « zigzag » décrit plus haut : l’illustration à gauche est un exemple de ce type de modification, ici apportée à un ancien four Hoffmann circulaire. En agrandissant le four de la sorte, il devenait absolument nécessaire d’augmenter la capacité de tirage de la cheminée par un ventilateur. Certains fours continus de grande dimension disposaient en outre de plusieurs cheminées. Ci-dessous : un four à 40 chambres de cuisson avec deux cheminées.
Fours Hoffmann (toujours) en activité
Les fours circulaires (et leurs quelques variantes) sont toujours utilisés de nos jours dans les pays en développement (la première image ci-dessous en montre un exemple en Chine, la seconde un autre en Mongolie), ainsi que par quelques rares producteurs artisanaux de briques traditionnelles dans les pays développés – leurs produits étant principalement destinés à la rénovation de bâtiments patrimoniaux ou anciens.
Dans certains pays en développement, on peut observer l’utilisation d’une version low-tech du four Hoffmann, dans laquelle la galerie voûtée est remplacée par une simple couverture faite de briques et de sable. Appelé four Bull du nom de son inventeur britannique W. Bull, ce type de four est d’usage courant au Pakistan, en Inde, au Bangladesh, au Népal (some great pictures here) ou encore à Myanmar.
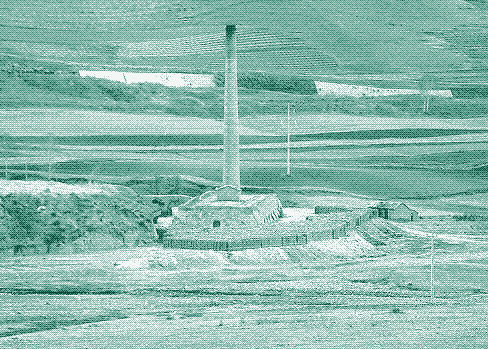
Ces fours semi-continus mesurent entre 100 et 150 mètres de long, et prennent généralement la forme d’une tranchée creusée dans le sol, qui fait office de galerie, le toit étant reconstruit à chaque passage du feu. Ils produisent des briques de même résistance mécanique, bien que d’une qualité esthétique moindre. Dans un four Bull les cheminées légères, faites de feuilles métalliques, sont déplacées toutes les 24 heures par une équipe d’ouvriers afin de mettre en cuisson une autre partie du tunnel.
Bien que moins efficients énergétiquement qu’un vrai four Hoffman, ces fours demeurent sur ce plan meilleurs que les fours périodiques. Leur principal avantage tient à coût de construction plus faible. Dans un four Hoffman traditionnel, le seuil de rentabilité – soit le moment à partir duquel les économies en combustible ont compensé l’investissement initial lié à la construction de l’édifice – n’est atteint qu’après la cuisson de six à dix millions de briques dans l’ouvrage.
Au cours de la seconde moitié du 20ème siècle, la plupart des fours existants dans les pays développés furent supplantés par des fours tunnel (brevetés dès 1877 par un autre Allemand, Otto Bock). Dans un four tunnel, le process du four Hoffmann est inversé.
La production contemporaine de briques: les fours tunnel
Dans un four Hoffmann, les briques demeurent en place et le foyer se déplace circulairement ; dans un four tunnel, le foyer reste statique tandis que les briques se déplacent, traversant lentement le tunnel. Le foyer est positionné au centre, et les briques avancent disposées sur un chariot ou un tapis roulant, de sorte que les briques au début du tunnel sont graduellement préchauffées à mesure que le foyer s’approche, tandis que celles étant dans la seconde moitié du tunnel peuvent redescendre lentement en température.
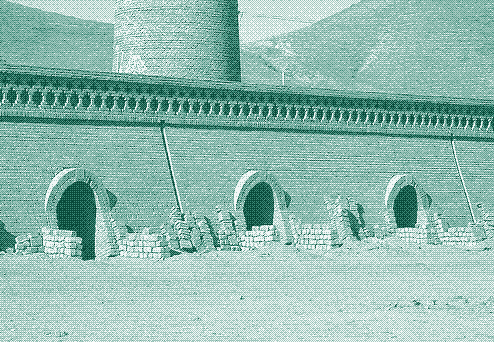
Si les fours tunnels sont bien plus chers à construire que les fours Hoffmann, leurs coûts de main d’œuvre en exploitation sont bien moins élevés, puisqu’ils peuvent être en grande partie automatisés – ils fonctionnent aujourd’hui sans la moindre intervention humaine. Pourtant, malgré tout ce déploiement de high-tech, ils ne sont pas plus économes en énergie que les fours Hoffmann – dans les deux cas, la cuisson d’un kilogramme de brique nécessite environ 2,000 kilojoules.
Comparés à certaines versions améliorées du four Hoffmann, les fours tunnels s’avèrent même plus énergivores. En outre, dans les briqueteries modernes, les gains d’efficacité énergétique sont trop souvent sacrifiés au profit d’une augmentation de la cadence, les étapes de séchage et de refroidissement étant accélérées en ayant recours à de l’énergie supplémentaire (généralement électrique, voir les caractéristiques d’un four tunnel contemporain).
La raison d’être des fours tunnels est bien l’accélération du procédé de production, dont résulte mécaniquement une augmentation conséquente de la quantité de briques produites. Il nous faut par ailleurs probablement y voir l’aspect le plus néfaste de la production contemporaine de briques de terre cuite. Il semble en effet y avoir une intime corrélation entre la cadence de la production et la facilité déconcertante avec laquelle nous construisons et démolissons aujourd’hui les bâtiments.
Sources (par ordre d’importance):
- “Cement, concrete and bricks”, Alfred B. Searle, 1914.
- “Modern brickmaking”, Alfred B. Searle, 1911. Le chapitre 8 (p.243-367) contient des informations complémentaires au sujet des fours Hoffmann.
- “Le grand four”, Musée des arts et métiers.
- “Notes on building construction”, Henry Fidler, 1889.
- “Dictionary of arts, manufactures, and mines containing a clear exposition of their principles and practice”, Vol.III, 1875.
- “Hoffmann kilns”, German Appropriate Technology Exchange (GATE).
- “Hoffmannscher Ringofen”, German Wikipedia. Note: la description du four Hoffmann sur la page anglaise est erronée. Elle y fait l’objet d’une confusion avec le four tunnel.
- “Hoffmann kiln, Craven Lime Works”, Out of Oblivion.
- “Architectural pottery: bricks, tiles, pipes, enamelled terra-cottas, ordinary and incrusted quarries, stoneware mosaics, faïences, and architectural stoneware”, Leon Lefêvre, K.H. Bird and W. Moore Binns, 1900.
- “Brickworks” par tarboat (images). Voir aussi le catalogue de briques and the other industrial sets. - “Ring-Ofen” par Karls Enkel (image).
- “Ziegeleipark Mildenberg” par Matthias 17 (images). - Briqueterie DeWulf & Schlot.at (pictures).