![Dépulpeuse de café à énergie hydraulique directe. Image : Brian W. Raichle [^1]](https://solar.lowtechmagazine.com/fr/2013/08/back-to-basics-direct-hydropower/images/dithers/direct-hydropower-1_dithered.png)
Toutes les centrales hydrauliques actuelles produisent désormais de l’électricité. Convertir l’énergie en électricité semble être devenu la seule manière d’exploiter l’énergie hydraulique, ce qui n’est pas le cas. Depuis près de 2000 ans, des roues hydrauliques (aussi appelées roues à eau) alimentent des machines en énergie directement par transmission mécanique.
En Afrique du Sud, certaines petites installations à énergie hydraulique directe démontrent l’intérêt de combiner l’usage de matériaux modernes avec d’anciennes techniques de mécanisation de l’énergie hydraulique.
En réduisant la quantité d’eau nécessaire pour générer une quantité donnée d’énergie, cette approche présente un rendement énergétique plus élevé. Cela réduit le coût de l’énergie hydraulique, et permet d’envisager la production d’énergie à partir de très petits cours d’eau.
Les installations à énergie hydraulique utilisées de nos jours ont un rendement énergétique plus faible que celles des siècles précédents.
Au cours de l’histoire, le rendement des moteurs hydrauliques n’a cessé d’être amélioré. Les roues à eau en bois, apparues il y plus de 2000 ans, convertissaient une fraction relativement faible de l’énergie hydraulique en puissance mécanique. Le rendement était alors de 5 à 15 % pour une roue à aubes horizontale, de 20 à 30 % pour une roue verticale « en dessous » - alimentée par le bas, de 50 à 60 % pour une roue verticale « en dessus » - alimentée par le haut. 1
Apparues à la fin du 19ème siècle, les roues hydrauliques en métal ont porté le rendement des roues verticales « en dessus » à 65 voire 85 %. 1 Les turbines hydrauliques, qui furent développées au 19ème siècle et sont encore utilisées comme moteurs hydrauliques dans les installations actuelles, convertissent généralement plus de 85 % de l’énergie cinétique de la source d’eau en puissance mécanique au niveau de l’arbre de transmission de la turbine. 2
À puissance équivalente, les turbines hydrauliques sont 10 à 20 fois plus compactes que les roues à eau, un avantage qui a permis de concevoir des moteurs hydrauliques à la fois beaucoup moins coûteux et plus puissants. Les turbines ont un champ d’application plus vaste que les roues hydrauliques, car ces dernières ne peuvent tirer parti d’une hauteur de chute (la distance verticale parcourue par l’eau) supérieure à leur propre diamètre pour accroître leur rendement. 1
Pourquoi l’énergie hydroélectrique contemporaine est moins efficiente
Malgré des améliorations substantielles qu’elles ont connues, les centrales hydroélectriques actuelles sont en fait moins efficientes que celles des siècles précédents. La coupable est l’électricité. Peu après que les turbines hydrauliques aient été introduites, un autre changement se produisit. Au lieu d’être utilisées comme moteurs d’entraînement pour faire tourner des machines directement (comme cela avait été le cas pendant des siècles), les turbines hydrauliques furent (et sont toujours, depuis lors) utilisées pour générer de l’électricité. Cette approche moderne a introduit un déficit énergétique, annulant par avance tous les efforts de conception ultérieurs visant à améliorer le rendement des centrales hydrauliques.
![Dépulpeuse de café à énergie hydraulique directe. Image : Brian W. Raichle [^1]](https://solar.lowtechmagazine.com/fr/2013/08/back-to-basics-direct-hydropower/images/dithers/hydro-powered-coffee-depulper-1_dithered.png)
Dans une centrale hydroélectrique actuelle, une turbine hydraulique convertit l’énergie cinétique de l’eau en mouvement, en énergie de rotation au niveau de son arbre, laquelle est ensuite transformée en énergie électrique par le générateur couplé à la turbine. Puis, cette énergie électrique est reconvertie en énergie de rotation par le moteur électrique de la machine qu’alimente installation. Or, chaque conversion entraîne une perte d’énergie.
Cette perte d’énergie est causée par la friction, ce qui se manifeste par de la chaleur, des vibrations et du bruit. La friction se produit à chaque étape de la transmission d’électricité : dans la turbine, le générateur, et le moteur. Des composants supplémentaires, comme des batteries, systèmes électroniques ou onduleurs, peuvent augmenter encore les pertes d’énergie.
On peut ainsi calculer le rendement énergétique de chaque centrale hydroélectrique contemporaine en mesurant le rapport entre l’énergie fournie en sortie par le générateur électrique, et l’énergie reçue par la turbine. Une microcentrale hydroélectrique produisant du courant électrique alternatif a un rendement « de l’eau au réseau » de 60 à 70 % maximum. Des systèmes de plus petite taille à courant continu, requérant des onduleurs et des batteries, ont un rendement inférieur, de 40 à 60 %. 3
La perte d’énergie dans les moteurs électriques des appareils alimentés n’est pas considérée dans ce calcul, mais devrait également être prise en compte (rendement « de l’eau au moteur »). L’efficacité d’un moteur électrique est très variable – de moins de 60 % pour des petits moteurs à plus de 95 % pour les plus gros. Ainsi, en moyenne, une centrale hydroélectrique ne convertit que la moitié environ de l’énergie potentielle de l’eau en travail utile.
Au Nicaragua, une dépulpeuse de café à énergie hydraulique directe fonctionne parfaitement depuis 5 récoltes.
Cela signifie qu’une petite centrale hydroélectrique contemporaine a le même rendement qu’une installation séculaire construite avec une roue à aube verticale « en dessus » (50 – 60 %), et que cet équivalent moderne est largement moins efficient que les roues hydrauliques en métal du 18ème siècle (65 – 85 %).
Dans une installation hydraulique ancienne, une seule conversion d’énergie avait lieu ; une roue hydraulique convertissait l’énergie cinétique de l’eau en énergie de rotation au niveau de son arbre de transmission. Ce même arbre faisait tourner les machines, de sorte que la seule perte d’énergie significative avait lieu au niveau de la roue elle-même. 3
![Dépulpeuse de café à énergie hydraulique directe. Image : Brian W. Raichle [^1]](https://solar.lowtechmagazine.com/fr/2013/08/back-to-basics-direct-hydropower/images/dithers/direct-hydro-coffee-depulper-3_dithered.png)
Notons que cela ne représente pas le rendement global de l’installation hydraulique : des frottements entrent aussi en jeu dans la conduite d’adduction qui alimente la turbine en eau. La plupart des petits systèmes hydrauliques n’ont pas recours à une retenue d’eau. Au lieu de cela, une partie du cours d’eau est détournée dans une conduite forcée en pente. Les pertes de charge au sein de la conduite sont identiques pour une installation hydraulique directe ou hydroélectrique. Par conséquent, elles seront négligées aux fins de la comparaison qui nous intéresse ici.
Pourquoi l’énergie hydraulique directe a du sens
Parmi toutes les configurations possibles pour une installation hydraulique, il en est une qui mérite une attention particulière : il s’agit d’une turbine hydraulique alimentant un ensemble de machines, sans passer par l’étape intermédiaire de production d’électricité. Selon le type de turbine utilisée dans un tel système, la valeur correspondant au rendement « de l’eau au moteur » est de l’ordre de 80 à 95 %. L’implémentation de cette forme d’énergie hydraulique multiplie ainsi par deux l’efficience d’une microcentrale hydroélectrique. 4
Cette plus grande efficacité énergétique présente plusieurs atouts. En évitant l’étape intermédiaire de conversion en électricité, une plus grande quantité d’énergie peut être obtenue et utilisée à hauteur de chute (la distance verticale parcourue par l’eau) et débit (quantité d’eau qui s’écoule en un point donné d’un cours d’eau) constants. Cet avantage peut servir à augmenter la production d’énergie d’une installation existante. Cela permet aussi d’envisager un plus grand nombre de sites hydrauliques potentiels – de taille plus réduite, et signifie que des ruisseaux et rivières relativement petits peuvent être partagés entre plusieurs unités hydrauliques.
Grâce à son plus haut rendement, une installation à énergie hydraulique directe est aussi moins chère qu’un système hydroélectrique. La quantité d’eau nécessaire pour générer une même puissance est moindre, ce qui signifie que l’ensemble des composants de l’installation peut être réduit en taille, en coût, et autres ressources nécessaires. Par exemple, les travaux de génie civil à mettre en place sont réduits. L’eau peut être acheminée jusqu’à la turbine à bas coût, basse pression, dans des tubes en plastique flexibles et facilement transportables, dont le diamètre est petit en comparaison des conduites forcées rigides et larges couramment utilisées dans les centrales hydroélectriques. Le raccordement souple de la conduite à la turbine simplifie également l’installation.
![Image : Dépulpeuse de café à énergie hydraulique directe. Source : Brian W. Raichle [^1]](https://solar.lowtechmagazine.com/fr/2013/08/back-to-basics-direct-hydropower/images/dithers/hydro-powered-coffee-depulper-4_dithered.png)
Enfin et surtout, le meilleur rendement de l’énergie hydraulique directe permet de limiter les impacts écologiques sur site. Un des fondements d’une production micro-hydraulique respectueuse de l’environnement consiste à maintenir un niveau d’eau suffisant au développement et l’épanouissement d’une flore aquatique dans le cours d’eau qui fournit l’énergie. Il est plus facile de parvenir à ce type d’équilibre écologique avec l’énergie hydraulique directe, car les quantités d’eau requises sont moindres.
Ancienne approche, nouveaux matériaux
Nombreuses sont les ONG qui développent de petites installations hydrauliques dans les pays en développement . La plupart visent à produire de l’électricité locale. Cependant, quelques-unes d’entre elles font exception à la règle. En 2007, une dépulpeuse de café hydraulique a été conçue, construite et installée au Nicaragua par une équipe de l’Université des Appalaches (Etats-Unis). D’après une étude récente parue dans la revue Energy for sustainable development, elle « fonctionne parfaitement depuis 5 récoltes ». 5
La quantité d’eau nécessaire pour générer une même puissance étant moindre, tous les composants du système sont de taille et coût réduits.
La majeure partie de l’énergie nécessaire à la collecte et la transformation du café est fournie par du travail manuel. Une des étapes les plus fastidieuses de la transformation des grains de café est le dépulpage, qui exige beaucoup de travail. Par le passé, cette opération était restreinte, pour son exécution, à une machine à manivelle, et demandait une nuit entière. Avec l’aide de techniques à énergie hydraulique directe, le dépulpage peut désormais être réalisé en seulement deux ou trois heures.
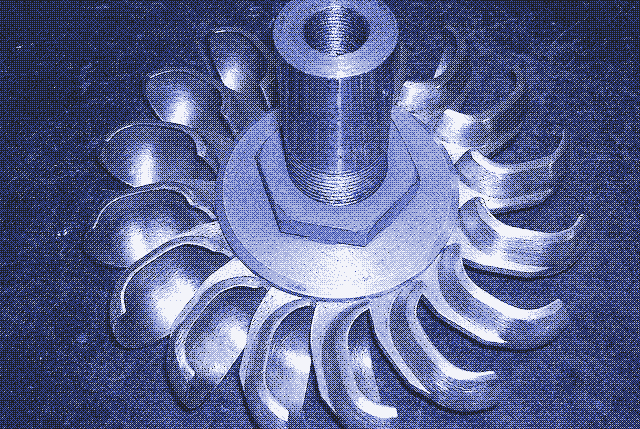
L’installation peut fournir un maximum de 800 watts avec une hauteur de chute de 35 m et un débit de 300 litres par minute. Le coût matériel estimé se limitait à 1900 $. En comparaison, l’ONG Practical Action indique qu’en ayant recours aux technologies appropriées, une microcentrale hydroélectrique coûte entre 1800 et 6000 dollars par kilowatt de puissance installée. Générer 1 kilowatt de puissance électrique demande environ 2 kilowatts de puissance mécanique, autrement dit l’énergie hydraulique directe est au moins deux fois plus rentable économiquement qu’une installation hydroélectrique pour une même capacité de production énergétique.
Un contrôle précis
La turbine utilisée par la dépulpeuse à café hydraulique est une turbine Turgo de marque Watermotor modèle 90, commercialisée par Campo Nuevo en Bolivie. D’après le fabricant, cet engin compact (16 x 16 x 32 cm) est « la seule turbine moderne » conçue pour faire tourner des machines courantes directement à l’énergie hydraulique.
La turbine est équipée d’une roue type Turgo de diamètre 9 cm, qui convertit l’énergie de l’eau en énergie mécanique avec un rendement de 80 à 85 %. Elle adaptée à des hauteurs de chute moyennes à élevées. Le modèle 150, plus grand, dispose d’une roue de 15 cm de diamètre et génère une puissance trois fois plus élevée.
Un moteur hydraulique est aussi aisé à commander et régler qu’un moteur électrique. Il dispose d’un interrupteur permettant de basculer en marche / arrêt instantanément, ce qui s’avère pratique pour faire fonctionner des machines qui ont besoin d’être fréquemment allumées et éteintes pendant leur utilisation. Un mécanisme appelé « déflecteur » dévie l’eau de la roue de la turbine, de sorte que la puissance du débit ne fasse pas augmenter la pression au sein de la conduite forcée.
La puissance délivrée en sortie par la turbine peut être modulée avec précision. Comme toutes les turbines « à action », la turbine Turgo est entraînée par des jets d’eau à haute vitesse. Un collecteur divise le débit d’eau issu de la conduite en 4 tubes plus petits, les injecteurs, chacun des flux débouchant sur un des 4 jets d’eau qui entraînent la turbine.
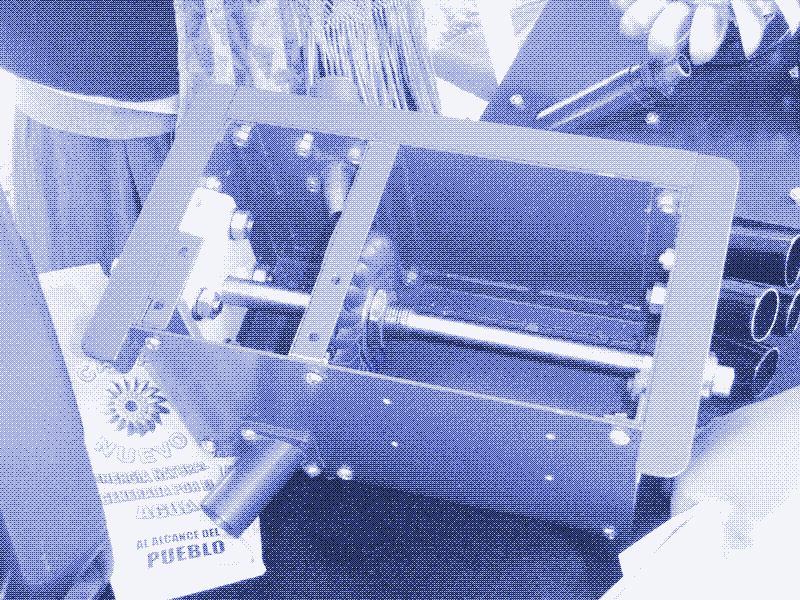
Chacune des 4 buses dispose d’une valve permettant de faire varier son débit, de sorte que le moteur peut être alimenté avec 1 à 4 jets en même temps. En outre, chaque jet peut être modulé individuellement sur une plage de débit donnée. Ce mécanisme permet de faire mesurer et d’ajuster de façon précise la puissance délivrée en sortie par le moteur et de s’adapter ainsi aux éventuelles variations saisonnières de débit d’eau.
Un atelier hydraulique de travail du bois
Sur le site démonstrateur de Campo Nuevo dans les Andes, le moteur hydraulique fait fonctionner un large spectre des machines, dont un petit atelier de travail du bois (avec scie circulaire fixe, meuleuse, rainureuse, foreuse, et disque abrasif), un bétonnière et un moulin à grains. Quand aucune de ces machines n’utilise la puissance mécanique (par exemple la nuit), le moteur alimente un générateur qui stocke l’énergie électrique dans des batteries pour l’éclairage, ainsi que d’autres usages auxiliaires. Le moteur hydraulique peut aussi faire marcher un compresseur d’air pour outils pneumatiques. (En principe, il pourrait tout aussi bien alimenter le compresseur d’un réfrigérateur). 6
Une petite cuve de stockage permet de faire tourner des machines encore plus puissantes
Le moteur hydraulique du site démonstrateur, alimenté par une chute verticale de 18 m et un débit d’eau moyen de 310 litres par minute, fournit une puissance équivalente à celle d’un moteur électrique O,75 CV (560 Watts) à 1450 tr/min. Loin d’être idéales pour une centrale hydroélectrique, ces conditions n’en sont pas moins parfaites pour la production d’énergie hydraulique directe.
Un petit réservoir de stockage relié à l’unité hydraulique permet d’alimenter ponctuellement des machines plus puissantes. Etant donné que le fonctionnement de la scie circulaire requière 500 litres d’eau par minute (un débit qui bien souvent n’est pas disponible), une cuve de stockage de 6 000 litres, de dimensions 2 x 2 x 1,5 m, a été installée. Elle permet ainsi d’utiliser la scie en continu pendant 15 minutes. Cette puissance additionnelle disponible ajoute jusqu’à 2 h de temps d’utilisation sur une journée de travail de 10 h.
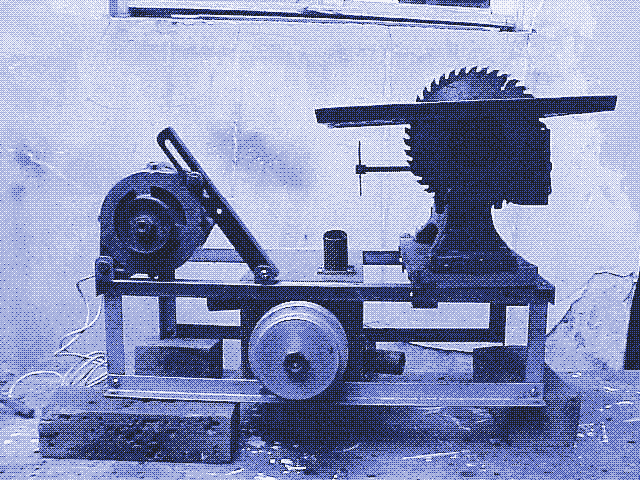
Toutes les machines (y compris le générateur et le compresseur d’air) sont placées directement sur le boîtier de la turbine, ou à côté. Ces outils peuvent être reliés à (et sont entraînés par) la même courroie. L’énergie n’étant pas distribuée, le moteur hydraulique ne peut faire fonctionner qu’une seule machine à la fois. Ce mode s’avère particulièrement adapté dans un atelier, où beaucoup d’outils et de machines sont utilisés par intermittence.
La même configuration est utilisée pour la dépulpeuse de café au Nicaragua, décrite plus haut. Les grains sont récoltés de décembre à février, et doivent être dépulpés dans les 24 heures qui suivent la cueillette. Cette contrainte dans le processus de transformation fait que la dépulpeuse est utilisée uniquement de nuit sur une courte période de l’année.
En conséquence, l’installation hydraulique est souvent disponible pour d’autres utilisations (comme faire fonctionner une scie, une perceuse, un compresseur d’air ou un générateur électrique). La turbine qui alimente la dépulpeuse de café peut fournir jusqu’à 800 watts de puissance mécanique, néanmoins, la dépulpeuse elle-même n’utilise qu’un quart de cette puissance – et un des quatre jets d’eau – pour obtenir les 200 watts nécessaires à son fonctionnement.
Perfectionner les moulins à eau médiévaux.
Assisterons-nous à un renouveau de l’énergie hydraulique directe ? Peut-être, mais il n’en demeure pas moins que, dans les faits, cette source d’énergie n’a jamais complètement disparu. Dans certaines régions montagneuses, on trouve encore des roues hydrauliques en fonctionnement, de conception similaire aux moulins à eau si couramment utilisés dans l’Europe médiévale. L’arbre en rotation entraîne directement la machinerie, qui de nos jours consiste principalement en moulins à grains pour la production de farine.
Dans des villages isolés au Népal, nombreux sont les paysans qui utilisent des types de moulins à eau de tous types pour moudre leurs grains. Environ 25 000 à 30 000 moulins sont encore en fonctionnement aujourd’hui. Dans le cas du Népal, l’objectif n’est donc pas de réintroduire l’énergie hydraulique directe, mais bien de faire en sorte que son usage perdure. C’est pourquoi l’ONG Central for Rural Technology Nepal (CRT/N) mène un programme de modernisation de ces moulins. Une fois améliorées, les roues hydrauliques peuvent moudre le grain plus efficacement et voient leur durée de vie allongée, ce qui les rend plus compétitifs vis-à-vis des moulins à moteur diesel.
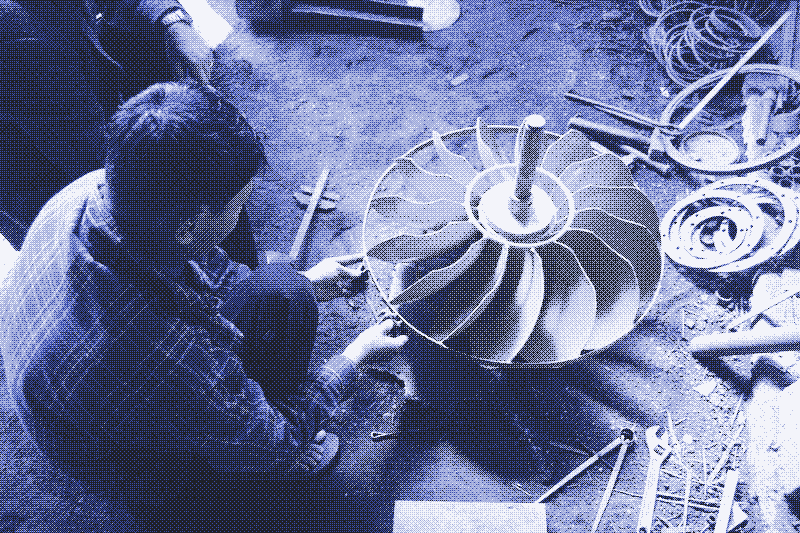
Pour faire simple, CRT/N perfectionne des roues à eau de type médiévales en roues hydrauliques de type 19ème siècle, en remplaçant certains composants clés en bois, comme l’arbre de transmission et la roue, par des éléments de précision en métal, produits localement. La conduite en bois qui alimente les moulins en eau est remplacée par un tuyau en polyéthylène haute densité (PEHD) qui réduit les fuites, entres autres problèmes évitables.
Au Népal, une ONG a modernisé plus de 5 000 moulins à eau intégralement en bois et encore en fonctionnement, au niveau technique équivalent aux roues du 19ème siècle, doublant leur rendement et leur permettant ainsi de rivaliser avec les moteurs diesel.
CRT/N a baptisé sa technologie le moulin hydraulique modernisé (en anglais Improved Water Mill, IWM). Selon certaines estimations, le rendement de meulage de ces moulins modernisés a doublé, ce qui correspond très précisément aux chiffres présentés en introduction de cet article. Grâce à un meilleur rendement, la quantité d’eau nécessaire est moindre, et le moulin peut fonctionner sur une plus grande période de l’année.
Remplacer les moteurs diesel.
L’ONG a modernisé 5 700 moulins entre 1990 et 2009. Dans certains cas, (237 pour être précis), les moulins existants ont en outre été adaptés, de manière à ce qu’ils puissent faire fonctionner d’autres machines, telles que des pressoirs à huile, décortiqueuses de riz, machines à coudre, ou un générateur électrique. Pour parvenir à cette modularité, il faut installer un arbre plus long, qui dissocie la roue des meules. Au lieu d’être directement relié aux meules, le long arbre principal est relié par une courroie à un second arbre pour le meulage, laissant ainsi la possibilité à d’autres machines d’être alimentées à l’énergie hydraulique directe.
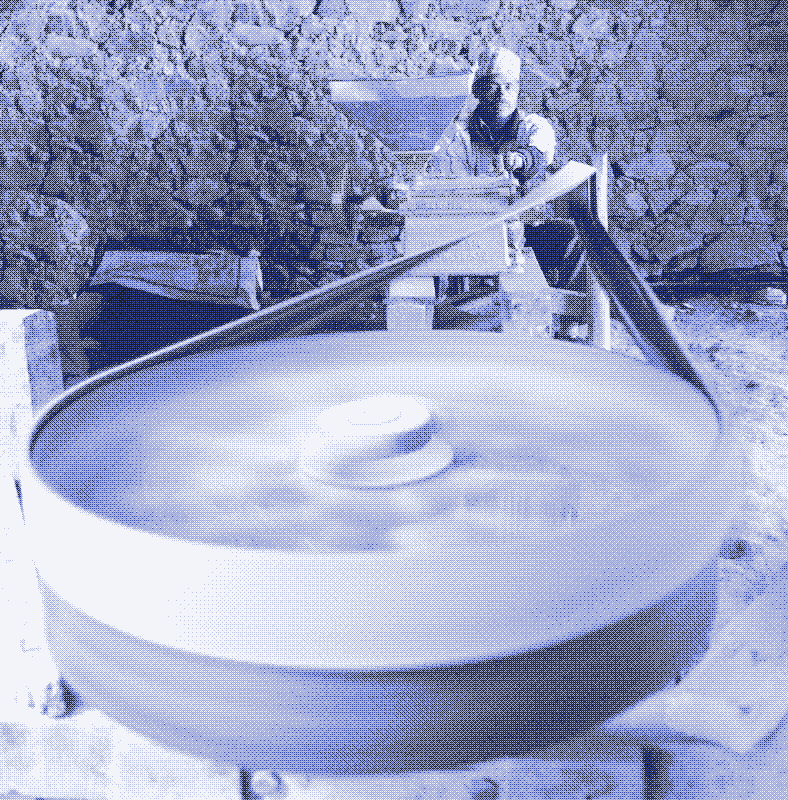
Ces roues hydrauliques modernisées n’atteignent certes pas le haut rendement des centrales d’énergie hydraulique directe qui utilisent des turbines, mais elles sont moins coûteuses. La modernisation « basique » d’un moulin à eau coûte 350 $, tandis que la version « modulaire » permettant de faire fonctionner plusieurs machines élève le coût total entre 900 et 1 200 $. En définitive, moderniser un moulin à eau traditionnel demeure au moins deux fois plus économique que de le remplacer par une installation hydraulique neuve à turbine. Au Népal, des moulins hydrauliques modernisés ont même remplacé certains moulins à grains au diesel, car il se révèlent moins coûteux en fonctionnement et produisent une farine de meilleure qualité. Le projet de modernisation des moulins à eau est toujours en cours. D’autres projets similaires mais à plus petite échelle ont été mis en œuvre, également en Himalaya par IT Power India (70 moulins modernisés pour un coût unitaire de 200 $), et aux Philippes par SITMo (en tant que composante d’un programme d’énergie en majeure partie hydroélectrique).
Le meilleurs des deux mondes
Ce plaidoyer en faveur de l’énergie hydraulique directe ne signifie en aucun cas qu’il faudrait arrêter d’utiliser l’électricité. Certains usages sont impossibles à alimenter en énergie mécanique, à commencer par l’éclairage et les équipements électroniques. De plus, nombre d’habitants de pays en développement n’ont aucun accès à l’électricité, ce qui les oblige à recourir à des lampes à pétrole, néfastes à leur santé.
Bien au contraire, les exemples décrits plus haut montrent la pertinence qu’il y aurait à combiner les deux approches. On obtiendra ainsi les meilleurs résultats avec une installation hydraulique produisant de l’énergie mécanique pour alimenter des machines, et stockant de l’énergie électrique dans des batteries pour l’éclairage et les autres usages quand la puissance mécanique n’est pas requise (par exemple la nuit). En comparaison avec un système purement mécanique, celui-ci offrirait des avantages supplémentaires non négligeables. En comparaison avec un système purement électrique, il fournirait une puissance plus importante, avec un meilleur rendement.
Mais les moteurs hydrauliques peuvent aussi fonctionner dans le cas où vous ne disposeriez pas d’un cours d’eau à proximité de votre maison, ferme ou manufacture. C’est précisément l’objet du prochain article : L’eau courante comme vecteur d’énergie : les moteurs à eau.